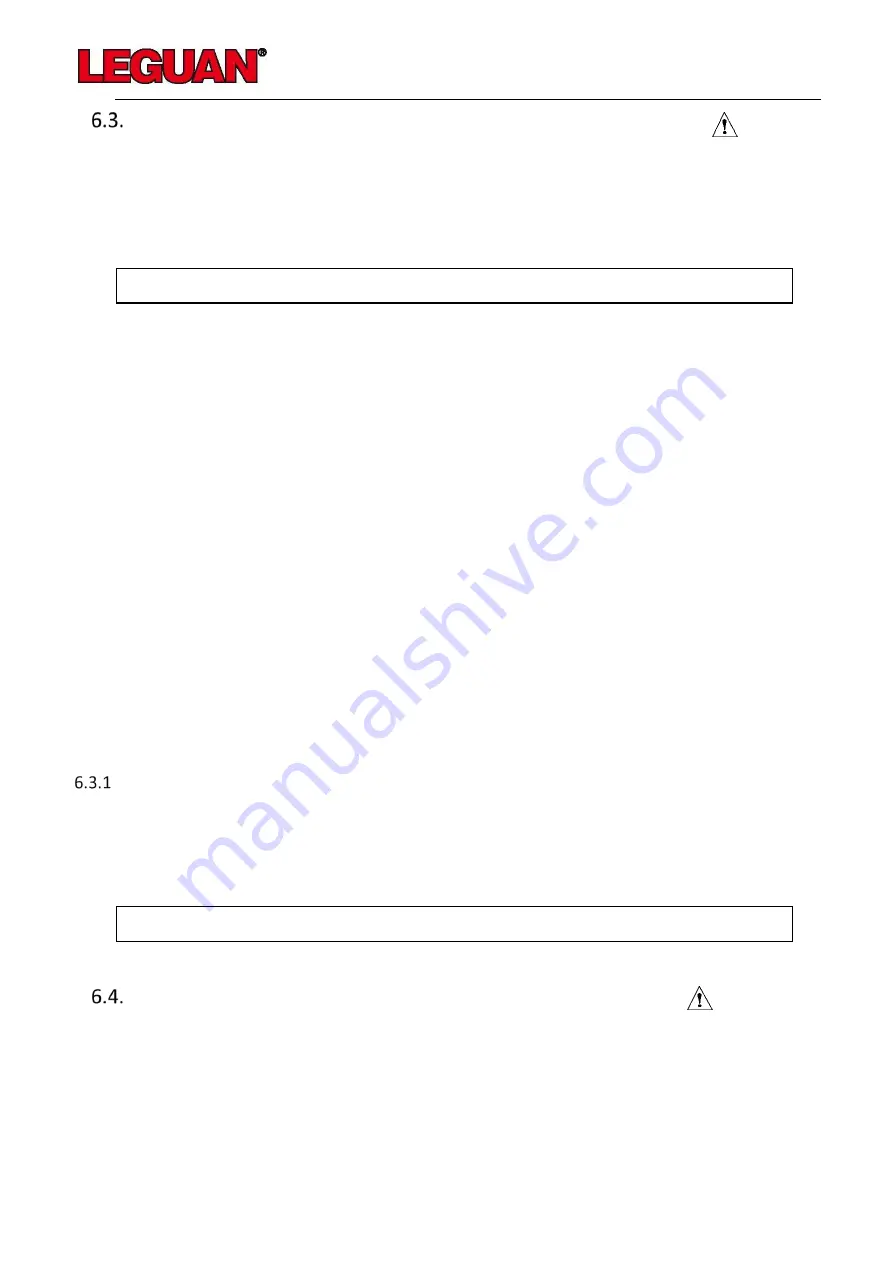
32
Override of boom safety functions when motor is running
For possible emergencies this access platform is equipped with a safety functions override
switch (p. 20, figure 8, switch 2), which enables boom movements without outriggers being
correctly set down. This function can be used for example in a situation when booms have
moved off their transport support during transportation.
To use the switch in the lower controls panel:
1.
Loosen the screws (lower controls, screws A and B) to detach the protecting plate
2.
Turn the override switch clockwise and hold it turned
3.
Turn on combustion engine or electric motor
4.
Lower the booms
slowly with caution
5.
Release the override switch
6.
Turn off engine / motor
7.
Attach the override switch
’s protecting plate (screws
A and B)
The function bypasses / allows:
-
overrides overload
-
decreases outreach monitoring by 62,5 kg
-
overrides platform levelling monitoring (automatic platform levelling is operational)
-
overrides telescope chain monitoring
-
overrides outrigger monitoring
-
overrides speed selector switch (dead
man’s
switch)
-
allows telescope in movement to remove overload
Override of boom safety functions using the hand pump
This function is activated from the lower controls panel with the emergency stop switch pushed
down and the only available power supply is the hand pump. Allows boom operation manually
from the lower control switches without safety functions or automatic aides.
Override of drive and outrigger safety functions
This function is activated from the lower controls panel (p. 20) when platform controls are
selected. Normal power supplies or alternatively the hand pump can be used. Movements are
controlled from the platform control panel. Hand pump can be used to operate outriggers.
When an engine/motor is running both drive and outriggers can be used.
This function overrides:
-
transport position monitoring
Override switch should only be used in extreme emergencies!
NOTE! Hand pump can only be used to operate outriggers and booms.
Summary of Contents for 135 NEO
Page 1: ...Operator and Service manual Version 7 2020 July 2020 ...
Page 9: ...9 Main dimensions Figure 2 135 NEO Main dimensions side Figure 3 135 NEO main dimensions rear ...
Page 10: ...10 Reach diagram and support dimensions Figure 4 Reach diagram Figure 5 Support dimensions ...
Page 59: ...59 Figure 37 Load control of the platform Figure 38 Boom position monitoring ...
Page 60: ...60 Figure 39 Platform levelling monitoring Figure 40 Outrigger monitoring ...
Page 61: ...61 Figure 41 Transport position monitoring Figure 42 Prevention of drive function ...
Page 64: ...64 Figure 47 Platform load monitoring override Figure 48 Override of Safety Functions ...