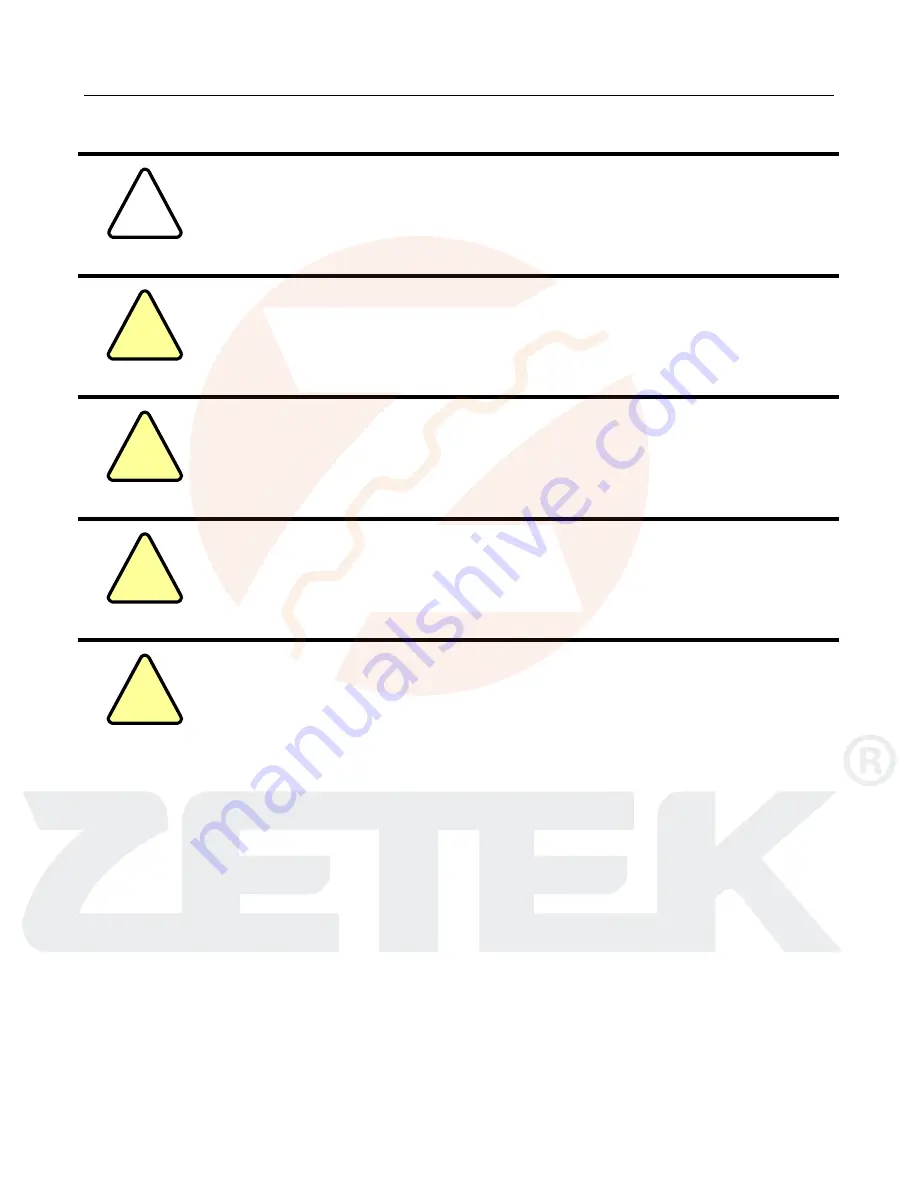
ii
Safety Items
!
Notice
Read this manual carefully before trying to install the stepper drive into your
system. Uses who setup the stepper drive should have a better understanding on
electronics and mechanics. Contact Leadshine technical guys when you have
questions on this document.
!
Caution
Make sure the power supply voltage dose not exceed the drive
’
s input range.
Double check the connections and make sure the power lead polarity is correct.
!
Warning
Do not set high current for small stepper motor. It is possible that the motor will be
damaged.
!
Caution
Disconnect the motor from the load if you are not sure the move direction. Adjust
the axis in the center before trying to run the motor.
!
Warning
Never disconnect the motor lead when the power source is energized.
www.servosystem.ru +7(495) 407-01-02