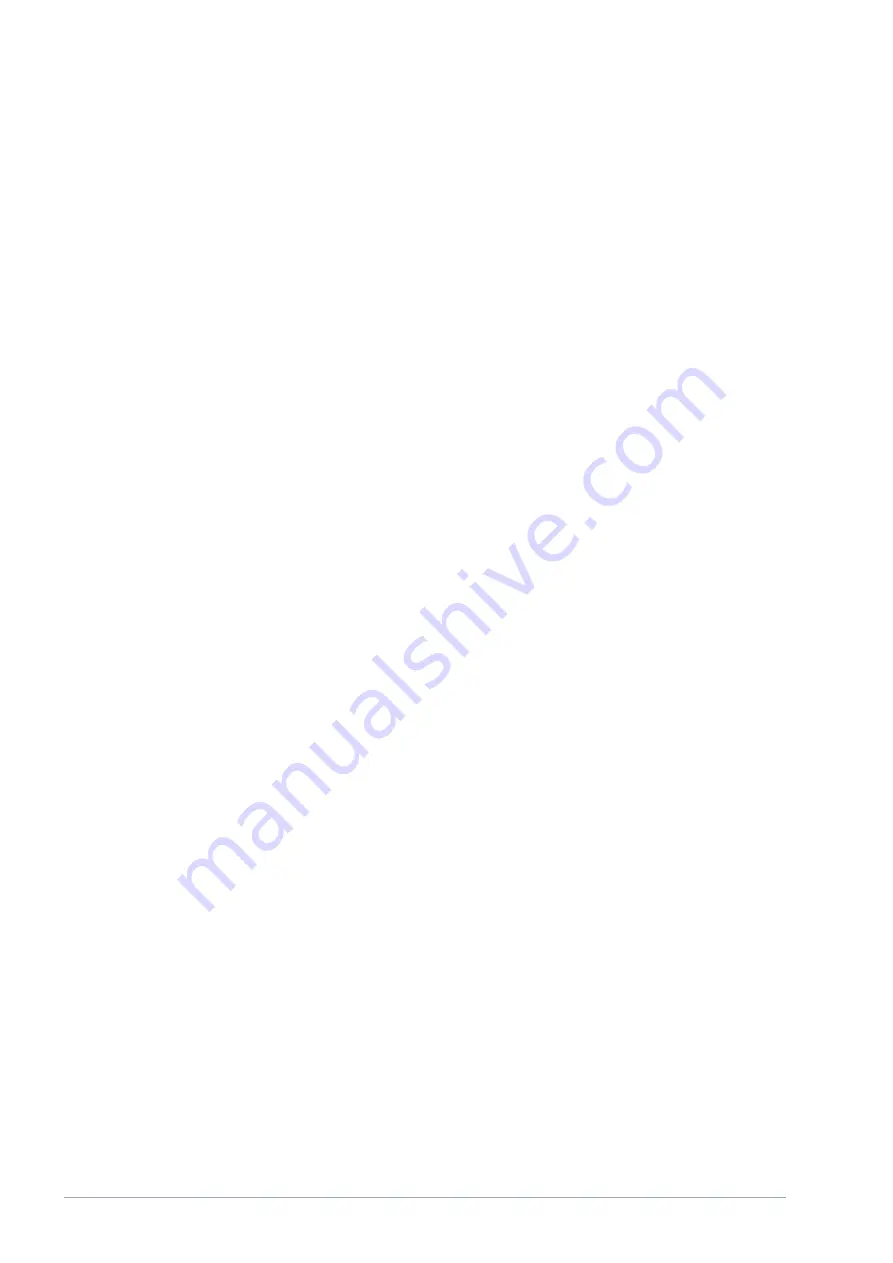
Terminal program . . . . . . . . . . . . . . . . . . . . . . . . . . . 31
U
Update . . . . . . . . . . . . . . . . . . . . . . . . . . . . . . . . . 14
W
Warning . . . . . . . . . . . . . . . . . . . . . . . . . . . . . . . . 33
Warranty . . . . . . . . . . . . . . . . . . . . . . . . . . . . . . . . . 6
V1
Interface module LRZ 930
38 / 38