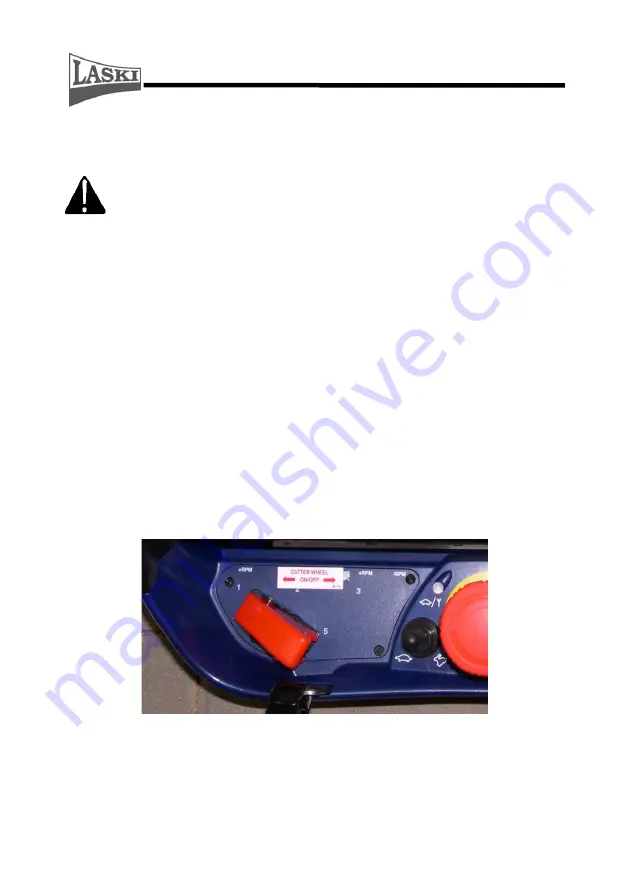
Predátor P 56RX
29
Handling and Storage
-
The stump cutter is allowed to be transported to site either on a
trailer or on a low-bed truck. It is not designed to go on public roads.
-
As an option you can get a special trailer directly by the machine manufacturer.
-
When loading the cutter on a trailer, fasten retention chains, straps or cables to
the machine chassis. Do not put them over or against hydraulic hoses. Make
sure that they do not cause damage to rubber tracks. Fasten each corner of the
machine and fasten the front arm to the trailer / vehicle bed with a chain / strap
or a suitable anchor.
-
Remember to use a purpose-designed ramp or a loading platform for loading
and unloading the stump cutter. The ramp must be strong enough to support the
weight of the machine (min. carrying capacity of 2000 kg).
-
Do not load the machine by means of ramps and emergency controls if the
height of loading area exceeds 750 mm. Otherwise these controls should get
beyond the reach of your hands - accident risk.
-
Before loading expand the track base to maximum.
-
Avoid any handling with inclination exceeding the permissible limit of 11
o
.
-
While loading and transporting the cutter never operate any control levers
except for the drive control levers when going up or down a ramp. Actuating
other levers can cause the machine to become unbalanced and tip over.
The
switch for cutting head control must be closed by its red cover
(fig. 12)
.
Fig. 12 - Driver running milling cutter
-
When going to another working site always ascend and descend slopes very
carefully and with the cutting head up hill. Before going on hilly terrain expand
the track base to maximum.
Summary of Contents for Predator
Page 1: ...Orig version 07 2020 OPERATING INSTRUCTIONS STUMP CUTTER Pred tor P56 RX...
Page 5: ...Pred tor P 56RX 5...
Page 6: ...Pred tor P 56RX 6...
Page 54: ...Pred tor P 56RX 54 ELECTRIC CIRCUITRY...
Page 55: ...Pred tor P 56RX 55...
Page 56: ...Pred tor P 56RX 56 HYDRAULICS...