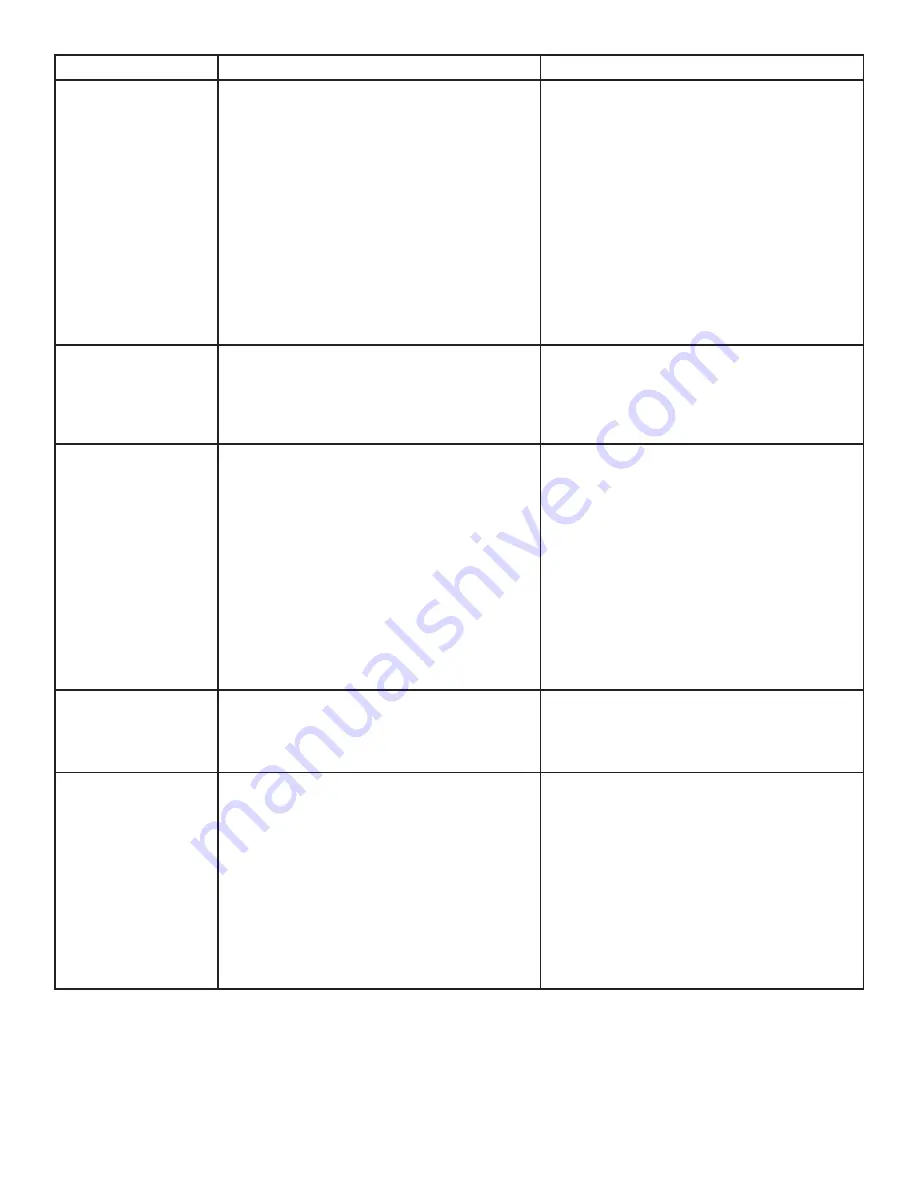
11
TROUBLE
CAUSE
REMEDY
Water only dispensed;
no syrup; or syrup only
dispensed, no water
1.
Water or syrup shutoff on mounting block not
fully open.
2.
Improper or inadequate water or syrup flow.
3. BIB supply too far from dispenser.
4. CO
2
pressure too low.
5. Stalled or inoperative BIB pump
6. Kinked line.
1.
Open shutoff fully.
2. Remove valve from mounting block, open
shutoffs slightly and check water and syrup
flow. If no flow, check dispenser for freeze-up
or other problems. Ensure BIB connection is
engaged.
3. Check that BIB supply is within six (6) feet of
the dispenser.
4. Check the CO
2
pressure to the pump manifold
to ensure it is between 70 and 80 psi (0.483
and 0.552 MPa).
5. Check CO
2
pressure and/or replace pump.
6. Remove kink or replace line.
Valve will not shut off.
1. Cup lever may be sticking or binding.
2. Switch not actuating freely.
3. Solenoid armature not returning to bottom
position.
1. Correct or replace lever.
2. Check switch for free actuation.
3. Replace defective armature or spring.
Excessive foaming.
1. Incoming water or syrup temperature too high.
2. CO
2
pressure too high.
3.
Water flow rate too high.
4.
Nozzle and diffuser not installed.
5.
Nozzle and diffuser not clean.
6. Air in BIB lines.
7. Poor quality ice.
8. High beverage temperature.
1. Correct prior to dispenser. Consider larger
dispenser or pre-cooler.
2. Adjust CO
2
pressure downward, but not less
than 70 psi.
3.
Re-adjust and reset ratio. Refer to “Adjust
Water Flow Rate & Syrup/Water Ratio” Section.
4. Remove and reinstall properly.
5. Remove and clean.
6. Bleed air from BIB lines.
7. Check quality of ice used in drink.
8. Check refrigeration system.
Water continually over
-
flows from water bath
into drip tray.
1. Loose water connection(s).
2. Flare seal washer leaks.
3. Faulty water coil.
1. Tighten water connections.
2.
Replace flare seal washer.
3. Replace water coil.
Warm drinks.
1. Dispenser was recently installed.
2.
Restricted airflow.
3. Dispenser connected to hot water supply.
4. Condenser fan motor not working.
5. Dirty condenser, air vents clogged.
6. Dispenser capacity exceeded.
1. It may take up to 5 hours, after install, to reach
the desired temperature.
2. Check clearances around sides, top, and
inlet of unit. Remove objects blocking airflow
through grill.
3. Switch to cold water supply.
4. Replace condenser fan motor.
5. Clean condenser and air vents of any
blockage.
6.
Add pre-cooler or replace with larger dispenser.