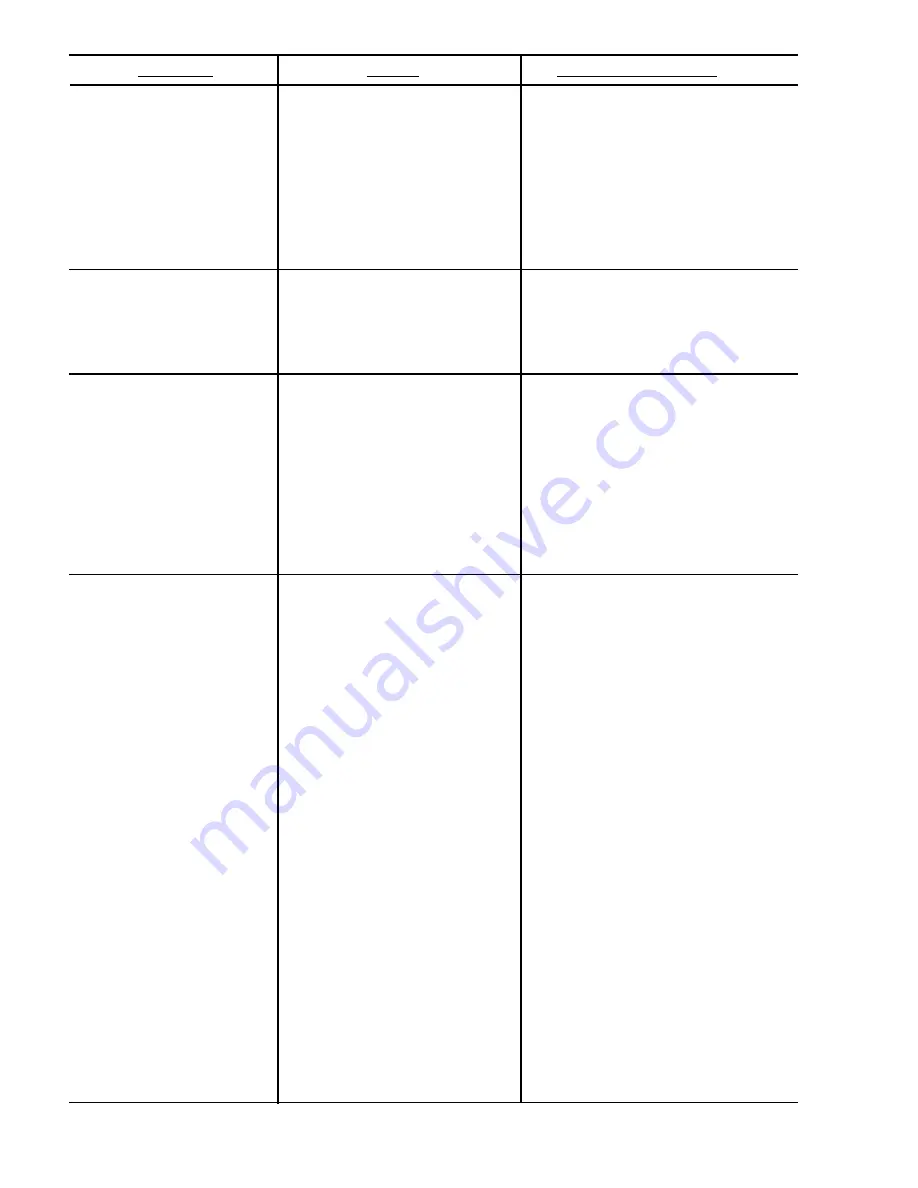
(Continued from previous page)
F. Dip tube in syrup tank blocked. F. Remove both quick disconnects
from syrup container. Depressurize
tank through relief valve. Remove
syrup and wash tank. Interchange
quick disconnects and pressurize to
the syrup out connection to remove
debris from dip tube. Clean tank
again. Upon completion, restore
disconnects to their original
locations.
G. Dispensing valve port blocked. G. Back-flush system.
3.
Only syrup dispensed,
A. Water mounting block shutoff
A. Open valve.
no water.
valve closed.
B. Water supply off.
B. Open water supply valve.
C. Inadequate water supply
C. Check pressure. Consider
pressure.
installation of water pressure
booster kit.
4.
Ratio cannot be set.
A. Inadequate water supply
A. Turn water flow control (left side) to
pressure.
full open (CW). Measure flow rate.
If greater than 2.5 oz/sec
(74 ml/sec), adjust water to
2.5 oz/sec., then adjust syrup. If
less than 2.5 oz/sec with flow
control at maximum setting, adjust
syrup to proper ratio with water at
maximum setting.
B. Product lines not installed
B. Ensure water supply is connected
properly.
to water inlet and syrup supply is
connected to syrup inlet.
5.
Bad taste or odor.
A. Dirty valve.
A. Clean nozzle and diffuser
thoroughly.
B. Foreign substance in water.
B. If water is free of impurities, it is
tasteless and odorless. Clean and
flush the system, and service the
water filter. (If the system does not
have a water filter, consider
installing one.)
C. Contaminated ice.
C. Same conditions may exist in ice as
in plain water. Check with ice
machine service personnel to have
filter installed. Clean ice bin or
chest.
D. Contaminated syrup.
D. Clean and sanitize lids, lid gaskets,
tanks and syrup/CO
2
couplers per
tank manufacturers or maintenance
instructions.
E. Impure CO
2
gas.
E. Carbon dioxide gas is odorless,
colorless and tasteless. If CO
2
gas
should contain any oil or sludge
from filling tanks, a bad taste could
result. Use only beverage grade
CO
2
. Welding grade CO
2
can be
contaminated.
F. Plumber's pipe compound.
F. Some of these compounds impart a
taste to the water. Remove piping
and clean joints. *Replace piping,
using only teflon tape.
G. Improper sealing of conduit
G. *Be sure conduit and chases are
and floor chases.
properly caulked and sealed with
approved materials.
*Servicing must be performed by
qualified service personnel.
PROBLEM
CAUSE
CORRECTIVE ACTION
6