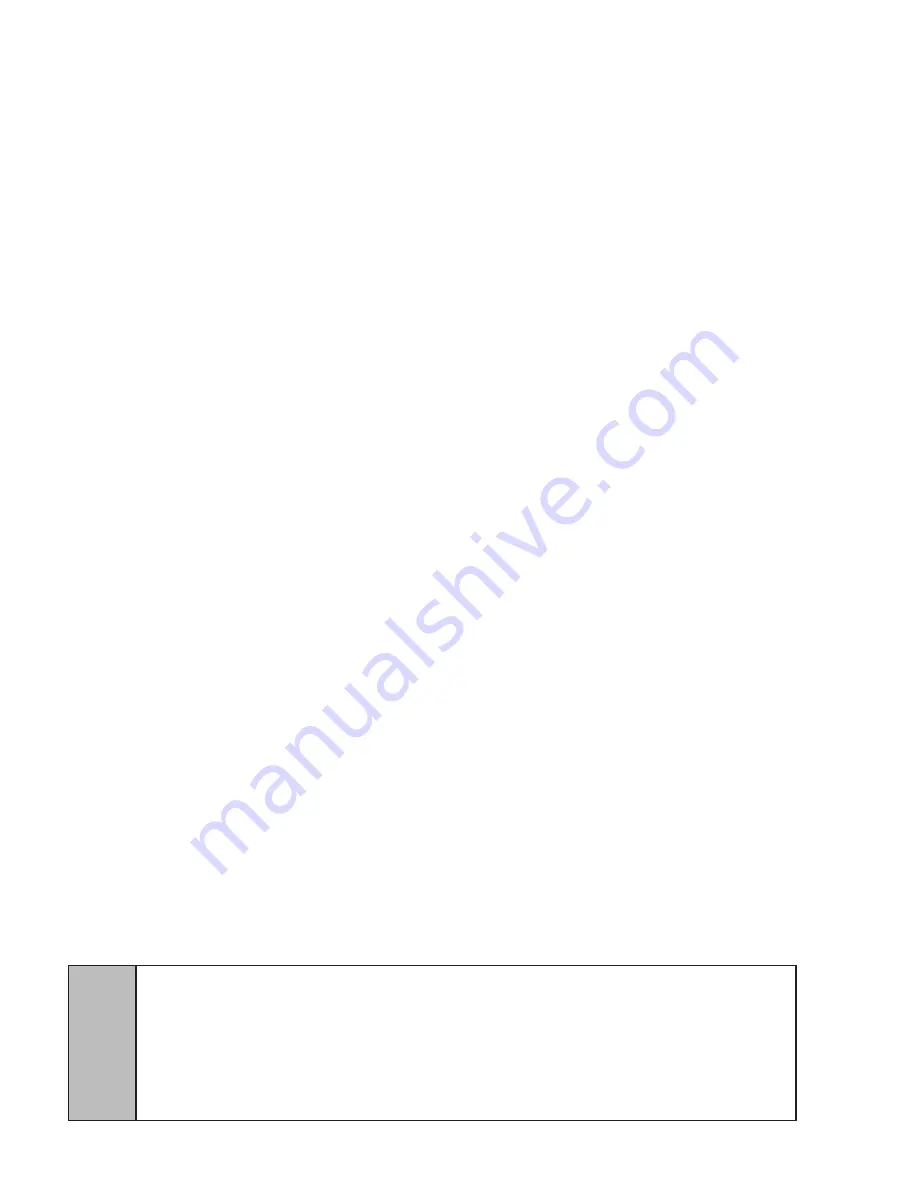
2.5 YEARLY
A. Clean water bath interior, including evaporator coils and refrigeration components.
B. Clean the entire exterior of the unit.
C. Sanitize syrup lines.
D. Check water pump screen for debris and/or clogging.
NOTE:
Because of difficulty in rinsing, detergent solution should not be introduced into the
carbonator.
3. DISPENSER CLEANING AND SANITIZATION
3.1 GENERAL INFORMATION
A. Lancer equipment (new or reconditioned) is shipped from the factory cleaned and sanitized
in accordance with NSF guidelines. The operator of the equipment must provide continuous
maintenance as required by this manual and/or state and local health department guidelines to
ensure proper operation and sanitation requirements are maintained.
NOTE:
The cleaning procedures provided herein pertain to the Lancer equipment identified by
this manual. If other equipment is being cleaned, follow the guidelines established by the manu
facturer for that equipment.
B. Cleaning should be accomplished only by trained personnel. Sanitary gloves are to be used
during cleaning operations. Applicable safety precautions must be observed. Instruction
warnings on the product being used must be followed.
3.2 CLEANING AND SANITIZING SOLUTIONS
CLEANING SOLUTION:
Mix a mild, non-abrasive detergent (e.g. Sodium Laureth Sulfate, dish
soap) with clean, potable water at a temperature of 90°F to 110°F (32°C to 43°C). The mixture
ratio is one ounce of cleaner to two gallons of water. Prepare a minimum of five gallons of cleaning
solution. Do not use abrasive cleaners or solvents because they can cause permanent damage to
the unit. Ensure rinsing is thorough, using clean, potable water at a temperature of 90°F to 110°F.
Extended lengths of product lines may require additional cleaning solution.
SANITIZING SOLUTION:
Prepare sanitizing solutions in accordance with the manufacturer’s writ-
ten recommendations and safety guidelines. The solution must provide 100 parts per million (PPM)
chlorine (e.g. Sodium Hypochlorite or bleach). A minimum of five gallons of sanitizing solution
should be prepared. Any sanitizing solution may be used as long as it is prepared in accordance
with the man- ufacturer’s written recommendations and safety guidelines, and provides 50 to 100
parts per million (PPM) chlorine.
3.3 AMBIENT PROCESS
The ambient process is the most common method for cleaning and sanitizing dispenser equipment.
A. Prepare the Cleaning Solution,referred to in Section 3.2.
B. Fill lines at pump inlet with Cleaning Solution ( Section 3.2). The solution should be prepared in
accordance with the manufacturer’s recommendations. Make sure the lines are completely filled
and allow to stand for at least ten (10) minutes.
C. Flush the detergent solution from the lines with clean water.
D. Prepare the Sanitizing Solution, referred to in Section 3.2.
E. Fill the lines with Sanitizing Solution. Make sure that lines are completely filled and allow to
stand for ten (10) minutes.
F. Draw drinks to refill lines and flush solution from the dispenser.
G. Taste the beverage to verify that there is no off taste. If off-taste is found, flush the syrup
system again.
16
!
CAUTION
FOLLOWING SANITIZATION, RINSE WITH END-USE PRODUCT UNTIL THERE IS NO AFTERTASTE. DO
NOT USE A FRESH WATER RINSE. THIS IS A NSF REQUIREMENT. RESIDUAL SANITIZING SOLUTION LEFT IN THE
SYSTEM CREATES A HEALTH HAZARD.
PRECAUCIÓN
DESPUÉS DE LA ESTERILIZACIÓN, ENJUAGUE CON EL PRODUCTO FINAL HASTA QUE
ELIMINAR EL SABOR QUE QUEDA. NO ENJUAGUE CON AGUA FRESCA. ÉSTA ES UNA EXIGENCIA DE NSF. SI
QUEDA SOLUCIÓN DE ESTERILIZACIÓN EN EL SISTEMA, GENERA UN PELIGRO PARA LA SALUD.
ATTENTION
DÉFENSE DE RINCER L’OUTIL À L’EAU FRAICHE IMMÉDIATEMENT APRÈS UN TRAITEMENT
SEPTIQUE.EN CAS DE APRÈS-GOÛT, NE PURGER AVEC LE PRODUIT FINAL UNE EXIGENCE NSF.
Summary of Contents for 605
Page 25: ...25 NOTES...
Page 28: ...28 5 2 MINIPUMP ASSEMBLY FIVE FLAVOR PN 82 3900 2 4 11 5 6 8 7 9 10 1 3...
Page 30: ...30 5 3 FOAM TANK CABINET ASSEMBLY 10 7 8 5 6 18 19 12 13 17 14 15 16 2 11 9 3 4 1...
Page 32: ...32 5 4 CARBONATOR WATER SYRUP LINE ASSEMBLIES 3 13 12 11 1 10 4 5 6 7 8 9 9 2...