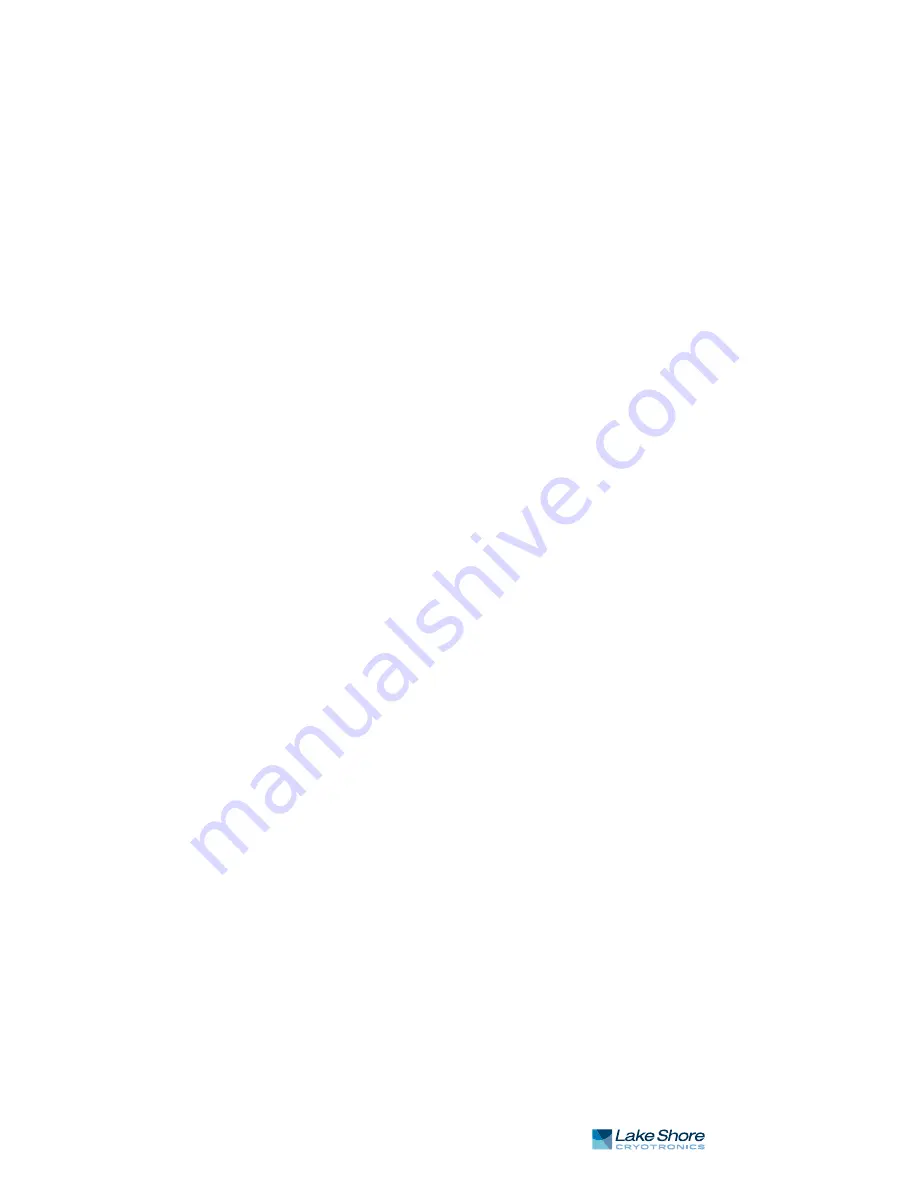
2.8.4 Tuning Derivative
29
|
www.lakeshore.com
2.8.4 Tuning Derivative
If an experiment requires frequent changes in setpoint, derivative should be consid-
ered. See FIGURE 2-2(e). A derivative setting of 0, off, is recommended when the con-
trol system is seldom changed and data is taken when the load is at steady state.
The derivative setting is entered into the Model 336 as a percentage of the integral
time constant. The setting range is 0–200% where 100% = ¼ I seconds. Start with a
setting of 50% to 100%.
Again, do not be afraid to make some small setpoint changes; halving or doubling this
setting to watch the affect. Expect positive setpoint changes to react differently from
negative setpoint changes.
2.9 Autotuning
Choosing appropriate PID control settings can be tedious. Systems can take several
minutes to complete a setpoint change, making it difficult to watch the display for
oscillation periods and signs of instability. With the Autotune feature, the Model 336
automates the tuning process by measuring system characteristics and, along with
some assumptions about typical cryogenic systems, computes setting values for P, I,
and D. Autotune works only with one control loop at a time and does not set the man-
ual output or heater range. Setting an inappropriate heater range is potentially dan-
gerous to some loads, so the Model 336 does not automate that step of the tuning
process.
When Autotune is initiated, step changes are applied to the setpoint and the system
response is observed to determine the best tuning parameters.
The Autotuning message appears when autotuning, and the display is configured to
show the output of the control loop being tuned. The message blinks to indicate that
the algorithm is still processing, and displays the current stage of the process, such as
Stage 3 of 7. If the tuning process completes successfully, then the message is
removed and the new PID parameters are configured. If the algorithm fails, the mes-
sage stops blinking to indicate that it is no longer processing, and a failure message
appears to indicate which stage of the process failed.
There are situations where Autotune is not the answer. The algorithm can be fooled
when cooling systems are very fast, very slow, have a large thermal lag, or have a non-
linear relationship between heater power and load temperature. If a load can reach a
new setpoint in under 10 sec (with an appropriate I-setting >500), the cooling system
is too fast for Autotuning. Systems with a very small thermal mass can be this fast.
Adding mass is a solution, but is unappealing to users who need the speed for fast
cycle times. Manual tuning is not difficult on these systems because new settings can
be tested very quickly. Some systems are too slow for the Autotune algorithm. Any
system that takes more than 15 min to stabilize at a new setpoint is too slow (with an
appropriate I-setting <5).
Thermal lag can be improved by using the sensor and heater installation techniques
discussed in section 2.4 to section 2.6. Lag times up to a few seconds should be
expected; much larger lags can be a problem. System nonlinearity is a problem for
both autotune and manual tuning. It is most commonly noticed when controlling
near the maximum or minimum temperature of a temperature control system. It is
not uncommon; however, for a user to buy a cryogenic cooling system specifically to
operate near its minimum temperature. If this is the case, try to tune the system at 5
degrees above the minimum temperature and gradually reduce the setpoint, manu-
ally adjusting the control settings with each step. Any time the mechanical cooling
action of a cryogenic refrigerator can be seen as periodic temperature fluctuations,
the mass is too small or temperature too low to autotune.
Summary of Contents for 336
Page 4: ...Model 336 Temperature Controller...
Page 6: ...Model 336 Temperature Controller...
Page 26: ...14 cHAPTER 1 Introduction Model 336 Temperature Controller...
Page 54: ...42 cHAPTER 3 Installation Model 336 Temperature Controller...
Page 84: ...72 cHAPTER 4 Operation Model 336 Temperature Controller...
Page 104: ...92 cHAPTER 5 Advanced Operation Model 336 Temperature Controller...
Page 164: ...152 cHAPTER 7 Options and Accessories Model 336 Temperature Controller...
Page 178: ...166 cHAPTER 8 Service Model 336 Temperature Controller...