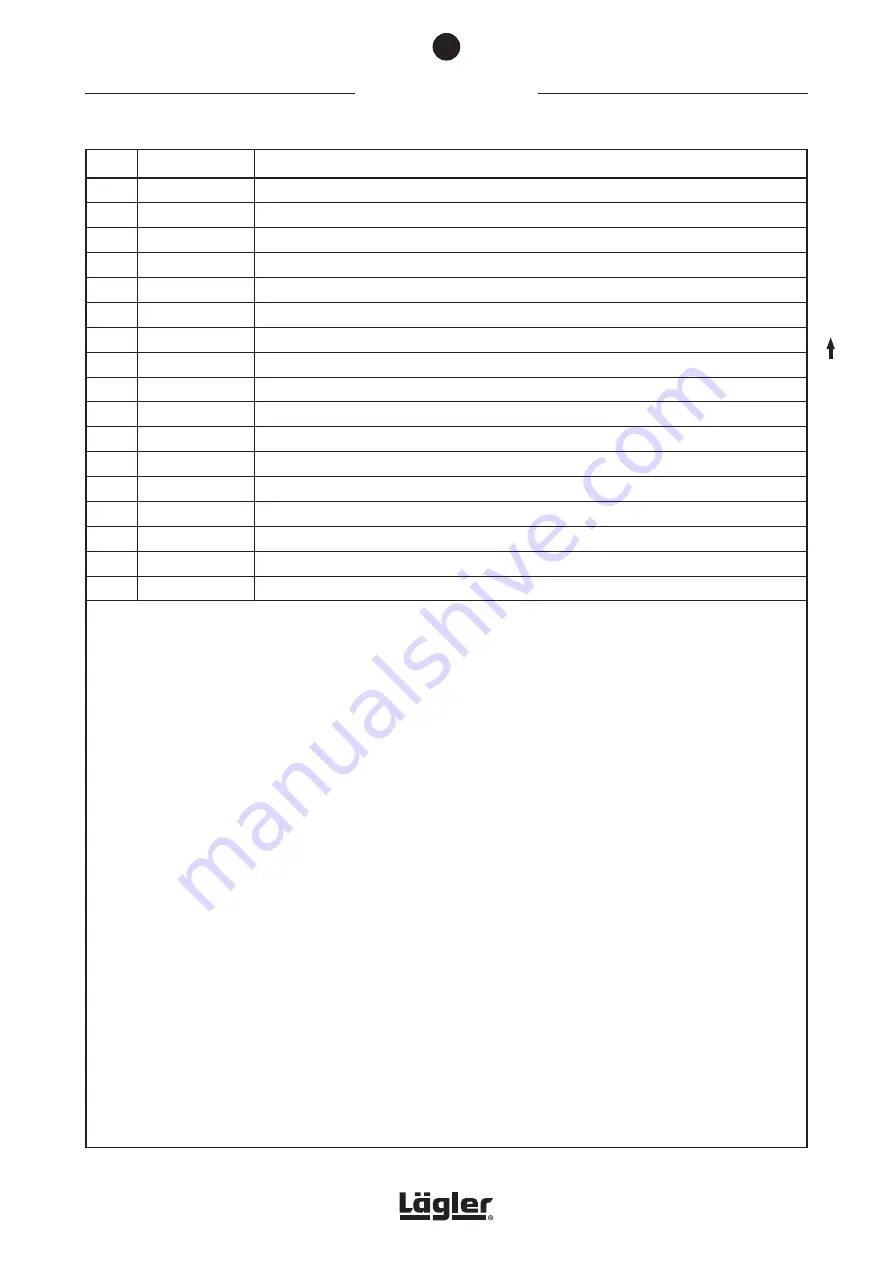
TRIO 01.04.2015
English / Englisch
SPARE PARTS TRIO
Item
Part number
Description
1
900.70.05.100
Frame, complete
2
900.70.25.105
Bumper felt
3
900.70.80.105
Protective rubber
4
900.70.36.100
Wheel, complete
6
900.70.34.100
Wheel holder
7
900.70.32.105
Wheel
8
0125.1008.000
Washer
9
7380.1008.055
Screw
10
0980.1008.000
Nut
14
0912.1008.020
Screw
15
900.70.70.300
Handle
17
000.20.40.081
Clamping device
18
900.70.52.105
Rubber buffer
19
7500.1005.012
Screw
20
900.00.16.100
Dust separator, complete
21
9021.0208.000
Washer
22
900.70.00.100
Chassis, complete
67
A
TTENTION: Please specify in inquiries and spare part orders always the serial numbers of your machines (
Section 3.1
)!
11