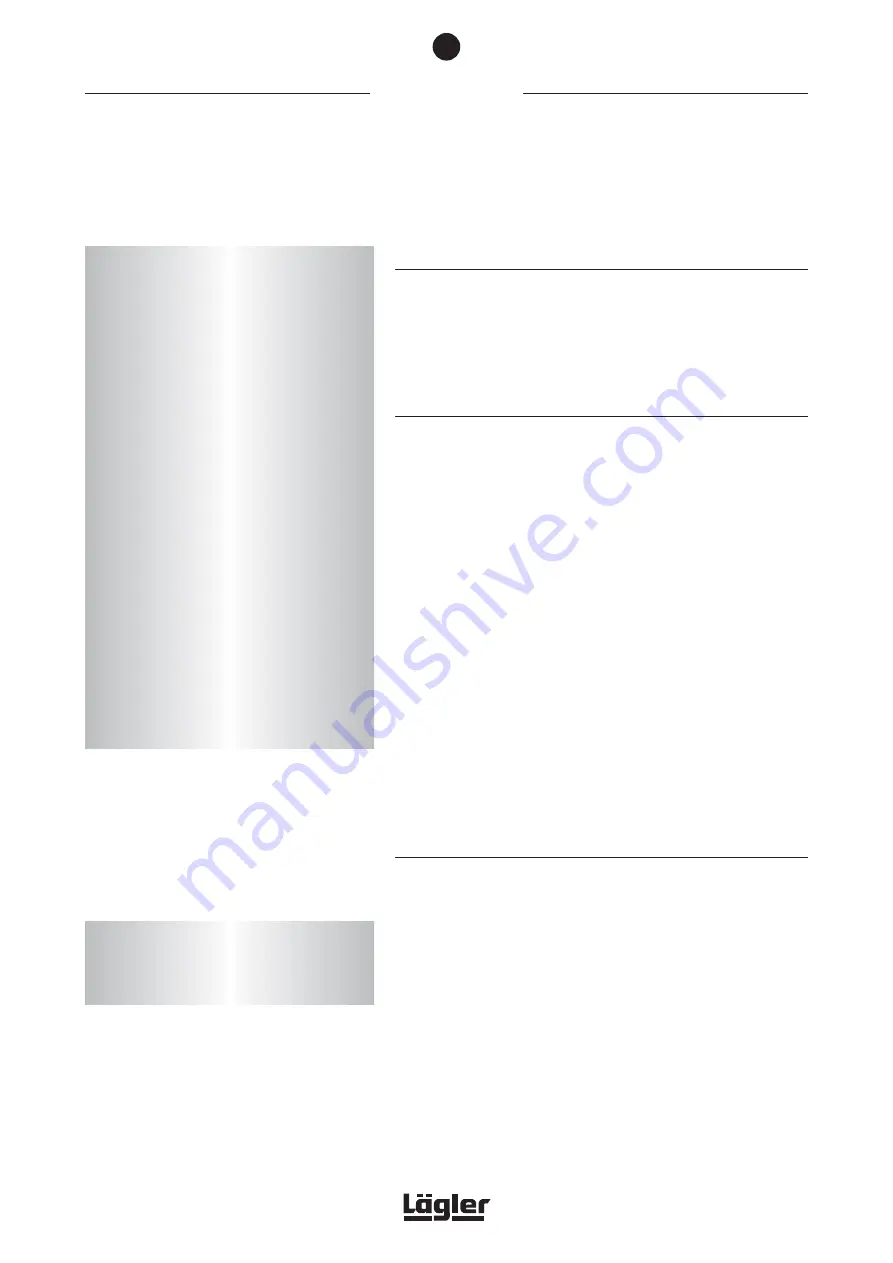
4
The belt sanding machine HUMMEL is only us-
able for dry processing. Never use your HUMMEL
for wet processing (Danger!).
INTRODUCTION
1.1 FEATURES OF THE MACHINE
Fig. 1 (page 2) shows the most important assemblies which make up
the HUMMEL. We recommend that you take some time to become
familiar with the machine.
1.2 DESCRIPTION OF THE MACHINE
The HUMMEL belt sanding machine operates with a contact sand-
ing drum featuring a specially profiled rubber coating. The belt
tensioning fixture with integrated automatic belt guidance is located
vertically above the sanding drum. The work zone is covered by
the machine housing and detachable side cover. On the machine
housing, the electric motor is fixed in a motor bearing bracket. The
plug for connection to the mains is located at the switch box of the
motor. The motor switch with the switch positions START / WORK-
ING and TEST is located at the switch box. On the left under the
belt guard is the belt drive unit. The machine is moved by means of
a steering wheel at the back and two lateral wheels. Two handles
are attached to the guide tube, where the drum lowering lever is
also located and the cables and dust bag are attached.
The HUMMEL belt sanding machine is intended for dry use only.
Never attempt to use the HUMMEL for any wet process (risk of
fatal accidents)!
1.3 INTENDED USE OF THE MACHINE
The HUMMEL belt sanding machine is suitable for sanding wooden
and cork floors, plastic skating rinks and tartan running tracks. A
specially equipped version of the machine can be used to sand
sheet metal surfaces.
Any application other than that described here is inadmissible
without the consent of the manufacturer. Never use for wet sand-
ing processes!
Introduction
1
You are now the owner of a high-quality
product from LÄGLER. We wish you every
success with the HUMMEL. This machine
has been manufactured using state-of-
the-art production techniques. All LÄGLER
products are subjected to thorough controls
before they leave the factory.
Please read right through these operat-
ing instructions before working with the
HUMMEL for the first time. The operating
instructions contain important information
relating to working safety and will answer
many of your questions, permitting you to
work confidently and safely with the ma-
chine. If you require information which is not
provided in these instructions, refer to your
sanding manual or consult our Customer
Services Department, which will be pleased
to advise you. Our fully trained and qualified
service technicians are highly familiar with
the HUMMEL and will be able to provide any
assistance you may need.
Summary of Contents for HUMMEL
Page 34: ...34 SPARE PARTS 10...
Page 36: ...36 SPARE PARTS 10...
Page 38: ...38 SPARE PARTS 10...
Page 40: ...40 up to May 2000 from May 2000 Please state the machine number with each order SPARE PARTS 10...
Page 42: ...42 SPARE PARTS 10...
Page 44: ...44 SPARE PARTS 10...
Page 46: ...46 NOTES...