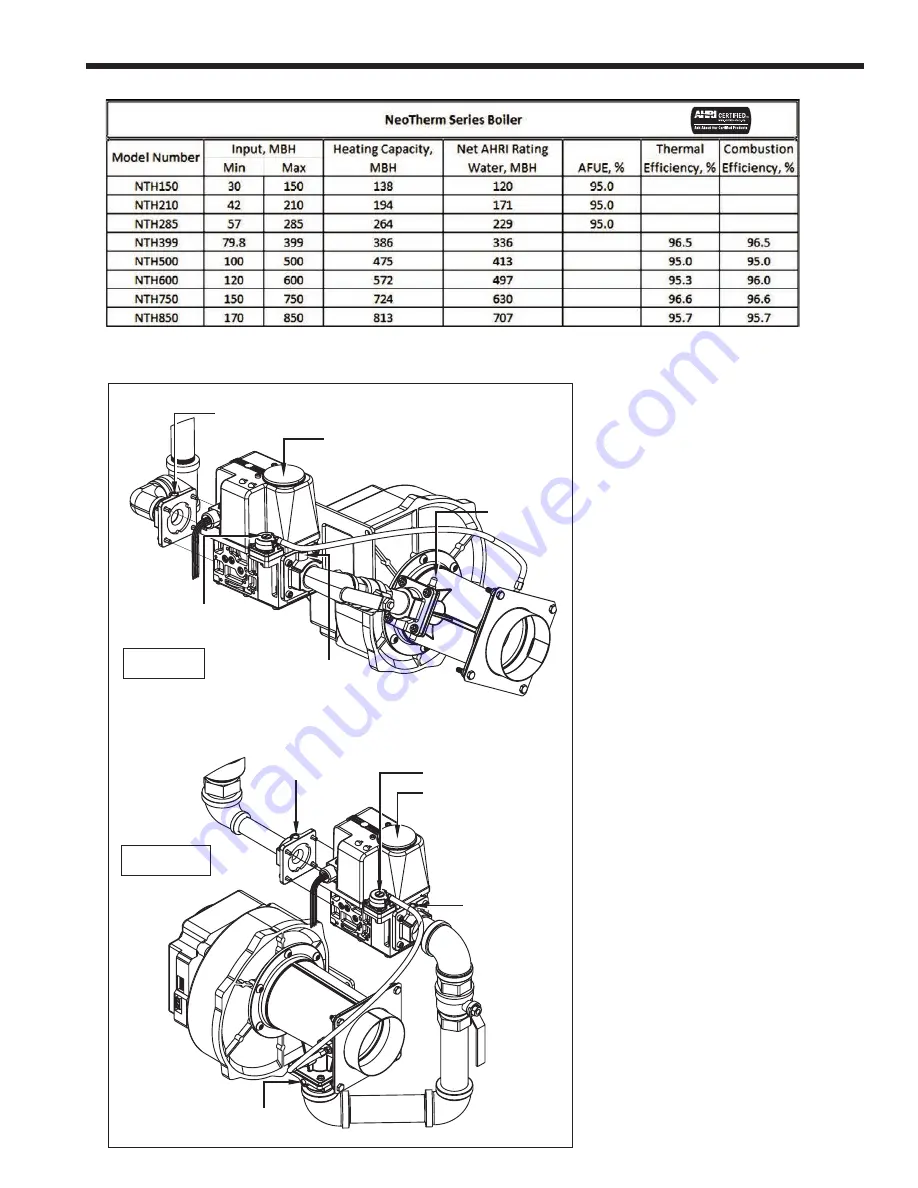
Page 59
N
EO
T
HERM
Boilers and Water Heaters
600
750, 850
Inlet gas pressure
High fire CO
2
adjustment
(under cap)
Gas
pressure
tap
Low fire CO
2
adjustment
Outlet gas
pressure
Inlet gas
pressure
Low fire CO
2
adjustment
High fire CO
2
adjustment
(under cap)
Outlet
gas pressure
Gas pressure tap
Outlet Gas
Pressure
(manifold
pressure)
Table 19. NeoTherm Boiler Efficiencies
Summary of Contents for NTH
Page 4: ...LAARS Heating Systems...
Page 13: ...Page 9 NEOTHERM Boilers and Water Heaters 38 1 2 98 8 3 4 22 7 1 2 19 64...
Page 30: ...Page 26 LAARS Heating Systems Figure 21 Hydronic Piping Single Boiler Zoning with Circulators...
Page 86: ...Page 82 LAARS Heating Systems Parts Illustration 1 Jacket Components...
Page 88: ...Page 84 LAARS Heating Systems Parts Illustration 4 Internal Components Sizes 750 850...
Page 90: ...Page 86 LAARS Heating Systems Parts Illustration 6 Gas Train Components Sizes 600 850...
Page 93: ...Page 89 NEOTHERM Boilers and Water Heaters Notes...
Page 94: ...Page 90 LAARS Heating Systems Notes...
Page 95: ...Page 91 NEOTHERM Boilers and Water Heaters Notes...