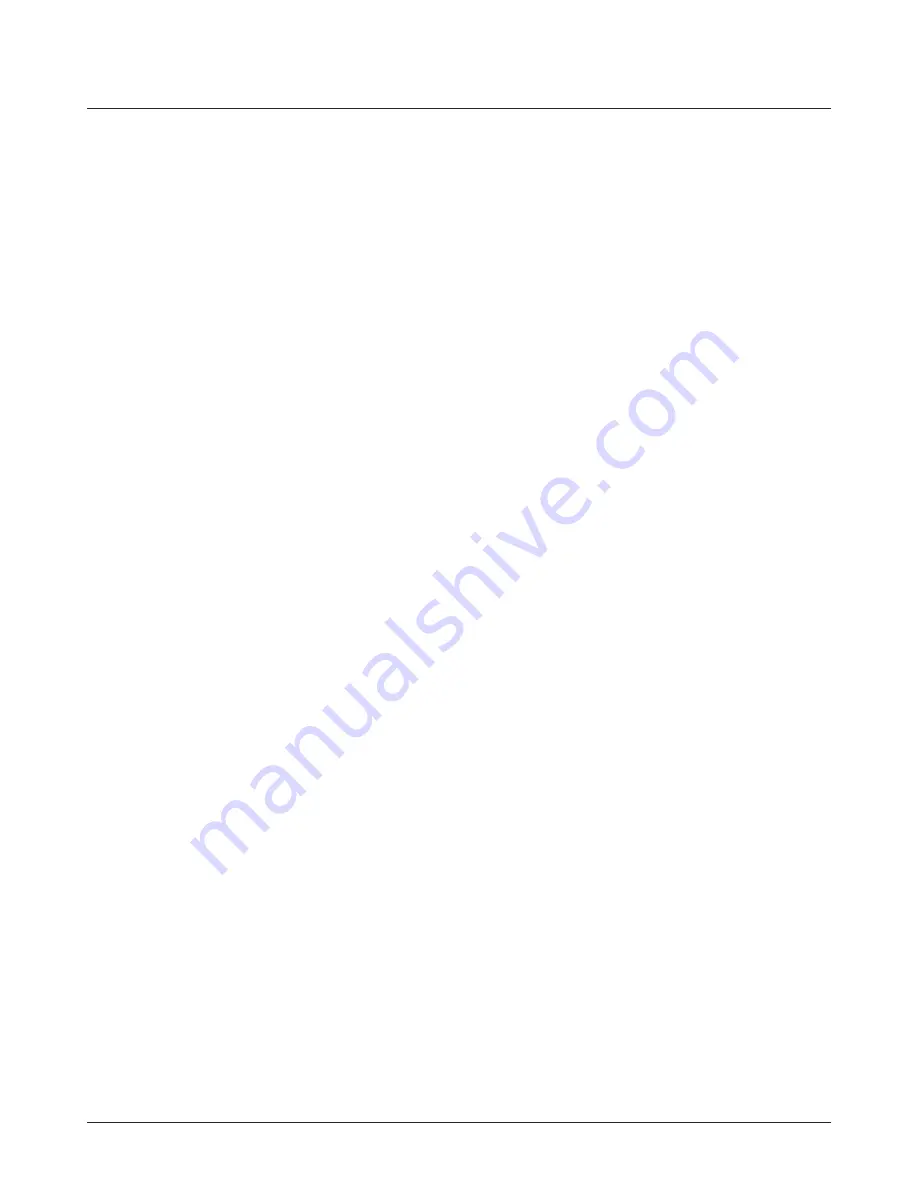
16
Cooktop ignition or cooktop burners faulty
Is the power on?
Are the sparker (ignition electrode) or burner holes
blocked by debris?
Are the burner heads correctly located? See the section
entitled
‘Cleaning’
.
Remember that each cooktop burner has a special
safety device that stops the flow of gas if the flame goes
out. When lighting a cooktop burner the safety device
has to be overridden by holding in the control knob so
that the gas can flow. This allows the flame sensor to
heat up and operate the safety device. Keep holding the
knob pressed in to let the gas through to the burner for
few seconds. The igniter should spark and light the gas.
If, when you let go of the control knob, the burner goes
out, the safety device has not held in. Turn the control to
the off position and wait one minute, then try again this
time holding in the control knob for slightly longer.
Cooktop burners will not light
If only one or all the cooktop burners will not light,
make sure that the parts have been replaced correctly
after wiping or removing for cleaning.
Check that there is not a problem with your gas
supply. You can do this by making sure that other gas
appliances you may have are working.
Do the burners spark when you push in the control
knob? If not check the power is on.
Steam is coming from the oven
When cooking foods with a high water content (e.g.
oven fries) there may be some steam visible at the rear
grille. Take care when opening the oven door, as there
may be a momentary puff of steam when the oven
door is opened. Stand well back and allow any steam to
disperse.
An oven fan is noisy
The sound of the oven fan may change as the oven
heats up – this is perfectly normal.
What cleaning materials are recommended for the range?
See the
‘Cleaning’
section for a full list of recommended
cleaning materials.
We
do not recommend corrosive or caustic cleaners
as these may damage your range.
The knobs get hot when I use the oven, can I avoid this?
Yes, this is caused by heat rising from the oven, and
heating them up. Do not leave the oven door open.
If there is an installation problem and I don’t get my
original installer to come back to fix it who pays?
You do. Service organizations will charge for their
5. Troubleshooting
service if they are correcting work carried out by your
original installer. It is in your interest to track down your
original installer.
Current Operated Ground Fault Circuit Breaker
Where the range installation is protected by a 30 mA
sensitivity residual current device (RCD), the combined
use of your range and other domestic appliances may
occasionally cause nuisance tripping.
Food is cooking too slowly, too quickly, or burning
Cooking times may differ from your previous
oven. Check that you are using the recommended
temperatures and rack positions. See the oven cooking
guide section of the instructions. The oven control
settings and cooking times are intended to be used
only as a guide. Individual tastes may require the
temperature to be altered either way, to get the results
you want. Try cooking at a higher temperature setting.
The oven is not cooking evenly
If you are cooking a large item, be prepared to turn it
round during cooking.
If two racks are used, check that space has been left for
the heat to circulate. When a baking sheet is put into the
oven, make sure it is placed centrally on the rack.
Check that the door seal is not damaged.
A dish of water when placed on the rack should be the
same depth all over. (For example, if it is deeper at the
back, then the back of the range should be raised up or
the front lowered).
If the range is not level arrange for your supplier to level
it for you.
Oven not coming on
Is the power on?
If not there may be something wrong with the power
supply. Is the range supply on at the circuit breaker?
Have you set a cooking function?
Oven temperature getting hotter as the range gets older
If turning the knob down has not worked or only
worked for a short time then you may need a new
thermostat. This should be installed by a service
technician (see the
‘Service and Parts’
section of the
instructions).
An oven light is not working
The bulb has probably burnt out. You can buy a
replacement bulb (which is not covered under the
warranty) from a good electrical shop. Ask for a 15W
125–130V lamp, FOR OVENS. It must be a special bulb,
heat resistant to 570°F (300°C)
(Fig.5-1)
.
Turn off the power at the circuit breaker.