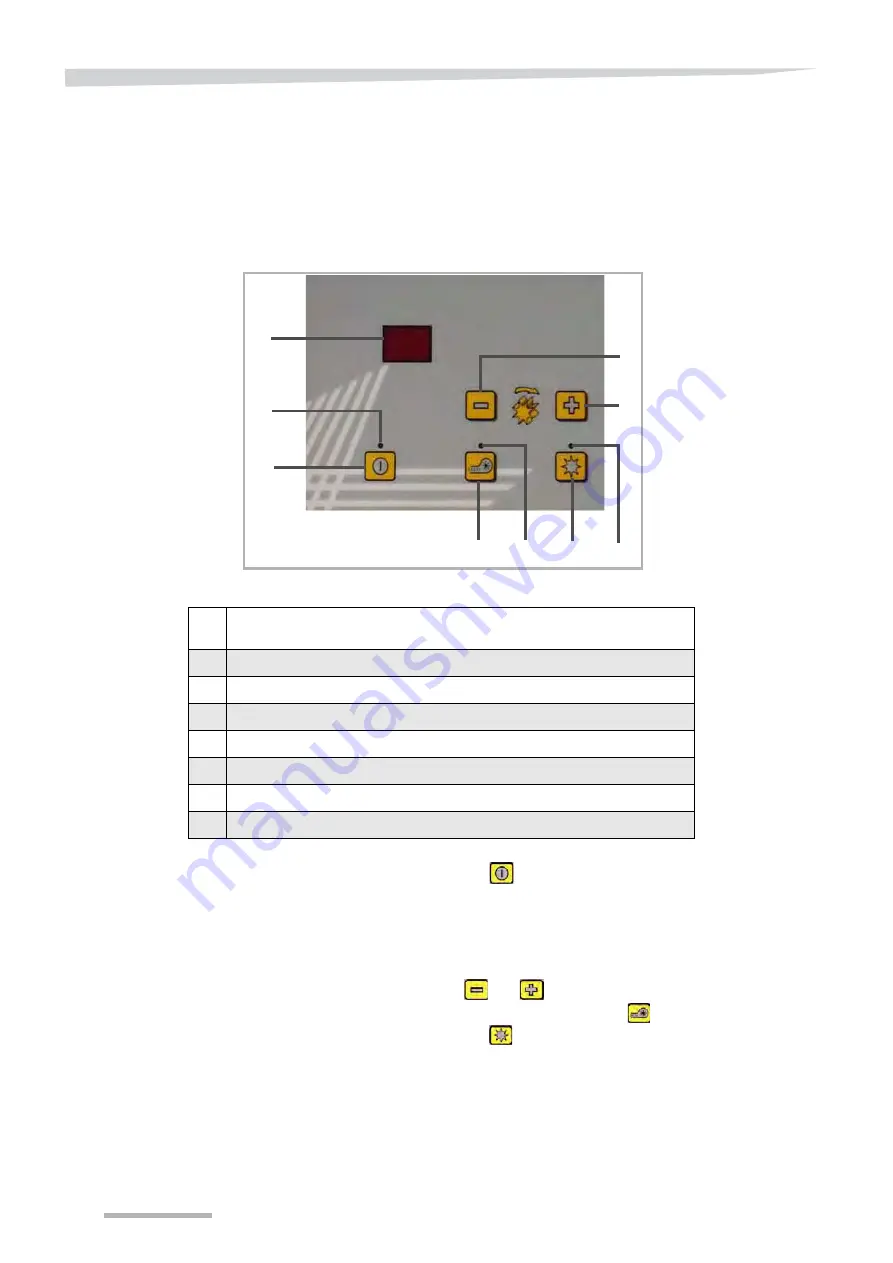
Adjustments
90
Adjustments
Using the seed drill with
the box 3.2
Description of the control
module
Switching on
Press on button XX to switch on the box.
The box version is displayed.
The indicator above the button lights.
The current rotor rotation speed in percentage of its maximum
speed is displayed.
Use buttons XX and XX to adjust the rotor rotation speed.
On electrical blowers, use the button XX to start the blower.
Press on button XX to switch on the distribution rotor.
A
B
C
D
E
F
G
H
H
A
Displays the actual rotor rotation speed as a percentage
of its maximum speed (from 1 to 99%).
B
Box power on indicator. Lights if the box is activated.
C
"On/Off" button: Activates or deactivates the box.
D
Activates the blower (only on models with electrical blower).
E
Blower power on indicator. Lights if it is activated.
F
On / off button for the distribution rotor.
G
Rotor on indicator. Lights when the rotor is operating.
H
Rotation speed adjustment buttons for the distribution rotor.
Summary of Contents for a-drill
Page 80: ...Seed drill adjustment 80 Sowing tables ...
Page 81: ...Seed drill adjustment 81 ...
Page 82: ...Seed drill adjustment 82 ...
Page 83: ...Seed drill adjustment 83 ...
Page 84: ...Seed drill adjustment 84 ...
Page 85: ...Seed drill adjustment 85 ...
Page 89: ...Filling the seedbox 89 Qualidisc and Qualidisc Farmer Unfold the machine Fill in the seedbox ...
Page 95: ...Adjustments 95 Main display Organisation of the menus ...