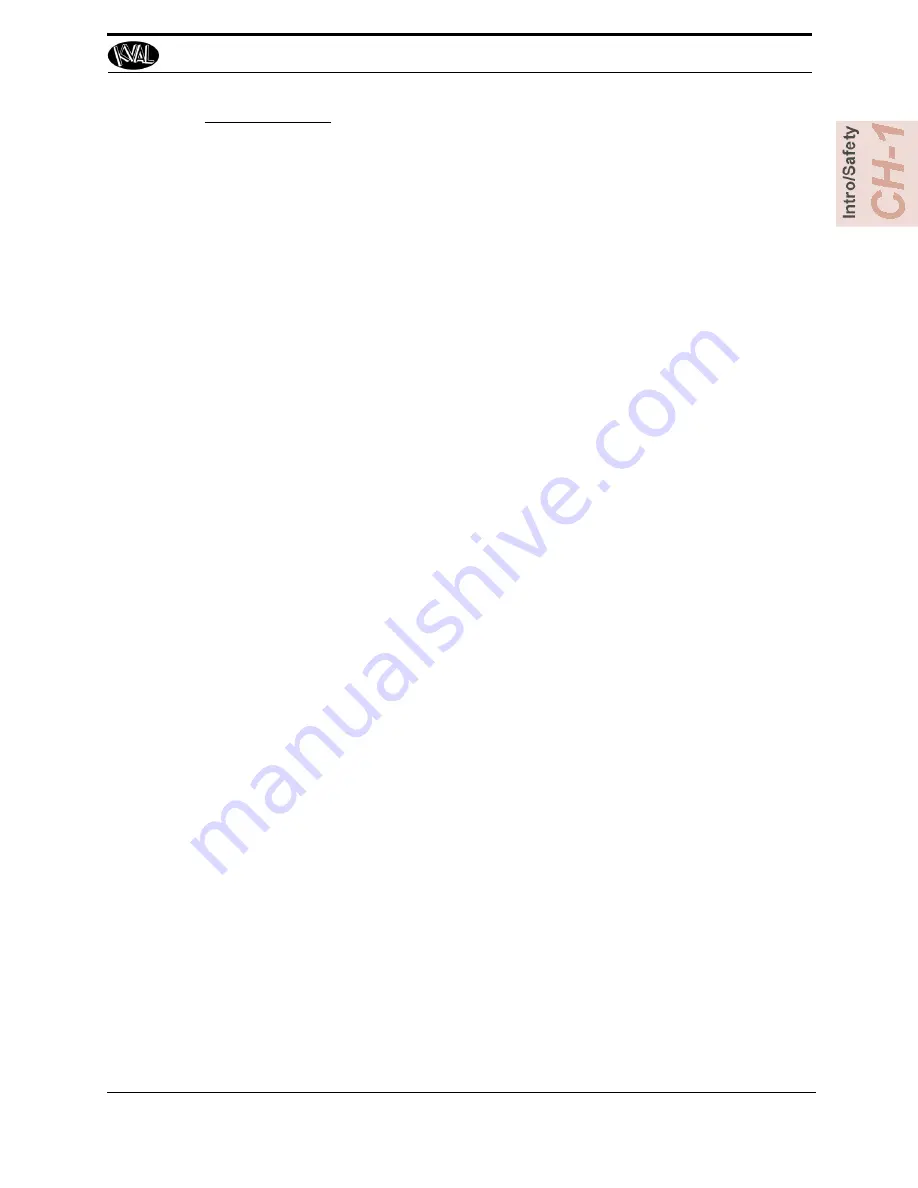
Getting Help from KVAL
KVAL 558 Operation Manual
1-13
2.
Reason for return: Before you return the unit, have someone from your organization
with a technical understanding of the machine and its application include answers to
the following questions:
• What is the extent of the failure/reason for return? What are the relevant error mes-
sages or error codes?
• How long did it operate?
• Did any other items fail at the same time?
• What was happening when the unit failed (e.g., installing the unit, cycling power,
starting other equipment, etc.)?
• How was the product configured (in detail)?
• Which, if any, cables were modified and how?
• With what equipment is the unit interfaced?
• What was the application?
• What was the system environment (temperature, spacing, contaminants, etc.)?
3.
Call Kval customer support for a Return Material Authorization (RMA). When you
call:
• Have the packing slip or invoice numbers available.
• Have the documented reason for return available.
4.
Send the merchandise back to Kval.
• Make sure the item(s) you are returning are securely packaged and well protected
from shipping damage
• Include the packing slip or invoice numbers.
• Include the documented reason for return.
• Include the RMA number with the parts package.
Summary of Contents for 558
Page 4: ...KVAL 558 Operations Manual ...
Page 24: ...Safety Sign Off Sheet 1 18 KVAL 558 Operation Manual ...
Page 51: ...Description of User Interface Screens 2 27 KVAL 558 Operation Manual ...
Page 58: ...Description of User Interface Screens 2 34 KVAL 558 Operation Manual ...
Page 62: ...System IT Administration 3 4 KVAL 558 Operation Manual ...
Page 66: ...Notes ...
Page 67: ...Notes ...