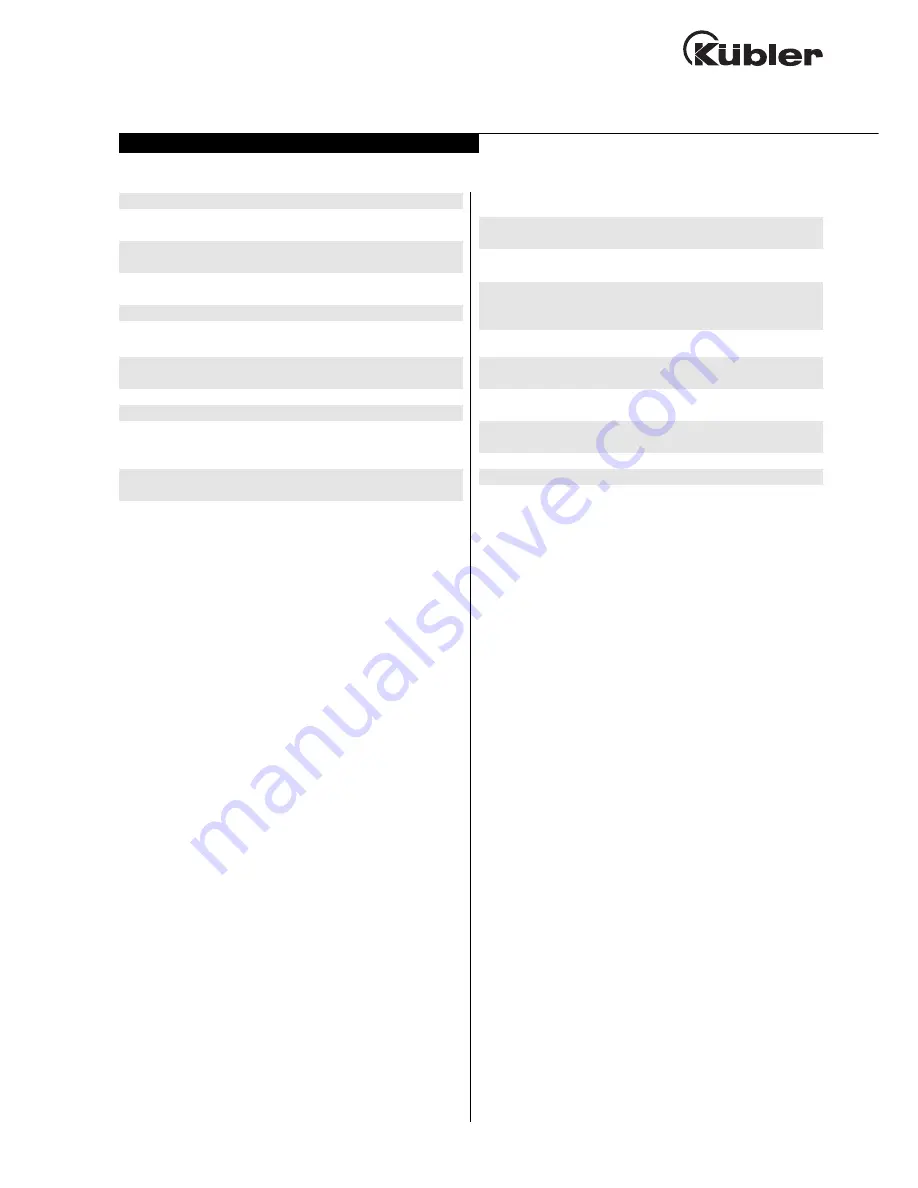
w
ww
ww
w..kku
ue
eb
blle
err..c
co
om
m
55
N
Ne
ew
w ffo
orr 22000066
Rotary Measuring Technology
Absolute hollow shaft encoder, Multiturn, CANopen/CANlift
S
Se
en
nd
diixx A
Ab
bsso
ollu
utte
e,, M
Mu
ullttiittu
urrn
n T
Tyyp
pe
e 55888888,, C
CA
AN
No
op
pe
en
n//C
CA
AN
Nlliifftt
G
Ge
en
ne
erra
all e
elle
ec
cttrriic
ca
all c
ch
ha
arra
ac
ctte
erriissttiic
css::
Supply voltage:
10 ... 30 V DC
Current consumption
24 V DC, max. 65 mA
(w/o output load):
Reverse polarity protection Yes
at power supply (Ub):
Conforms to CE requirements acc. to EN 61000-6-1, EN 61000-6-4
and EN 61000-6-3
IIn
ntte
errffa
ac
ce
e c
ch
ha
arra
ac
ctte
erriissttiic
css C
CA
AN
No
op
pe
en
n//C
CA
AN
Nlliifftt::
Singleturn resolution
1 ... 65536 (16 bits), default scale value is
(max, scaleable):
set to 8192 (13 bits)
Number of Revolutions:
4096 (12 bits), (scaleable 1 ... 4096)
Code:
Binary
IIn
ntte
errffa
ac
ce
e::
CAN High-Speed according ISO 11898,
Basic- and Full-CAN
CAN Specification 2.0 B
P
Prro
otto
oc
co
oll::
CANopen profile DS 406 V3.1 with
manufacturer-specific add-on's
or
CANlift profile DS 417 V1.1
Baud rate:
10 ... 1000 kbits/s
(set by DIP switches/software configurable)
Node address:
1 ... 127 (set by rotary switches / software
configurable)
Termination switchable:
Set by DIP switches
Software configurable
Protected against accidental activation, can only be pushed in with
the tip of a ball pen or similar.
S
SE
ET
T c
co
on
nttrro
oll b
bu
utttto
on
n ((zze
erro
o o
orr d
de
effiin
ne
ed
d vva
allu
ue
e,, o
op
pttiio
on
n))
LED on at:
optical sensor path faulty (code error, LED error), low voltage and
overtemperature
D
Diia
ag
gn
no
ossttiic
c LLE
ED
D ((yye
ellllo
ow
w))
G
Ge
en
ne
erra
all iin
nffo
orrm
ma
attiio
on
n a
ab
bo
ou
utt C
CA
AN
N//C
CA
AN
Nlliifftt
The CANopen encoders of the 5888 series support the latest
CANopen communication profile according to DS 301 V4.02. In
addition, device-specific profiles like the encoder profile DS 406
V3.1 and the profile DS 417 V1.1 (for lift applications) are available.
The following operating modes may be selected: Polled Mode,
Cyclic Mode, Sync Mode and a High Resolution Sync Protocol.
Moreover, scale factors, preset values, limit switch values and
many other additional parameters can be programmed via the
CAN-Bus. When switching the device on, all parameters, which
have been saved on an EEPROM to protect them against power
failure, are loaded again.
The following output values may be combined in a freely variable
way as PDO (PDO mapping): p
po
ossiittiio
on
n,, ssp
pe
ee
ed
d,, a
ac
cc
ce
elle
erra
attiio
on
n, as well
as the status of the working area.
As a price-effective variant, encoders with a connector or a cable
connection are available, for which the device address and baud
rate are modified by means of software. The models with bus
terminal cover and integrated T-shaped coupler allow a
particularly easy installation: bus and power supply are connected
very simply thanks to M12 connectors; the device address is set by
means of two hexadecimal rotary switches. Furthermore, another
DIP switch allows setting the baud rate and switching on a
termination resistor. Three LED’s located on the back indicate the
operating or fault status of the CAN bus, as well as the status of
an internal diagnostic.
C
CA
AN
No
op
pe
en
n C
Co
om
mm
mu
un
niic
ca
attiio
on
n P
Prro
offiille
e V
V44..0022
Among others, the following functionality is integrated:
Class C2 Functionality
NMT Slave • Heartbeat Protocol • High Resolution Sync Protocol
Identity Object • Error Behaviour Object • Variables PDO Mapping
self-start programmable (Power on to operational)
3 Sending PDO’s • 1 Receiving PDO for synchronous preset opera-
tion with minimal jitter • Knot address, baud rate and CANbus
Programmable termination
C
CA
AN
No
op
pe
en
n E
En
nc
co
od
de
err P
Prro
offiille
e V
V33..11
The following parameters can be programmed:
• Event mode
• Units for speed selectable
(Steps/Sec or RPM)
• Factor for speed calculation (e.g. measuring wheel periphery)
• Integration time for speed value of 1...32
• 2 work areas with 2 upper and lower limits and the corresponding
output states
• Variable PDO mapping for position, speed, acceleration, work
area status
• Extended failure management for position sensing with integrated
temperature control
• User interface with visual display of bus and failure status - 3
LED’s
• optional - 32 CAM’s programmable
• Customer-specific memory - 16 Bytes
C
CA
AN
No
op
pe
en
n LLiifftt P
Prro
offiille
e D
DS
S 441177 V
V11..11
Among others, the following functionality is integrated:
• Car Position Unit
• 2 virtual devices
• 1 virtual device delivers the posititon in absolute measuring steps
(steps)
• 1 virtual device delivers the posititon as an absolute
travel information in mm
• Lift number programmable
• Independent setting of the knot address in relation with
the CAN identifier
• Factor for speed calculation (e.g. measuring wheel periphery)
• Integration time for speed value of 1...32
• 2 work areas with 2 upper and lower limits and the corresponding
output states
• Variable PDO mapping for position, speed, acceleration, work
area status
• Extended failure management for position sensing with integrated
temperature control
• User interface with visual display of bus and failure status
- 3 LED’s
All profiles stated here: K
Ke
eyy--ffe
ea
attu
urre
ess
The object 6003h “Preset” is assigned to an integrated key,
accessible from the outside
“Watchdog-controlled” device