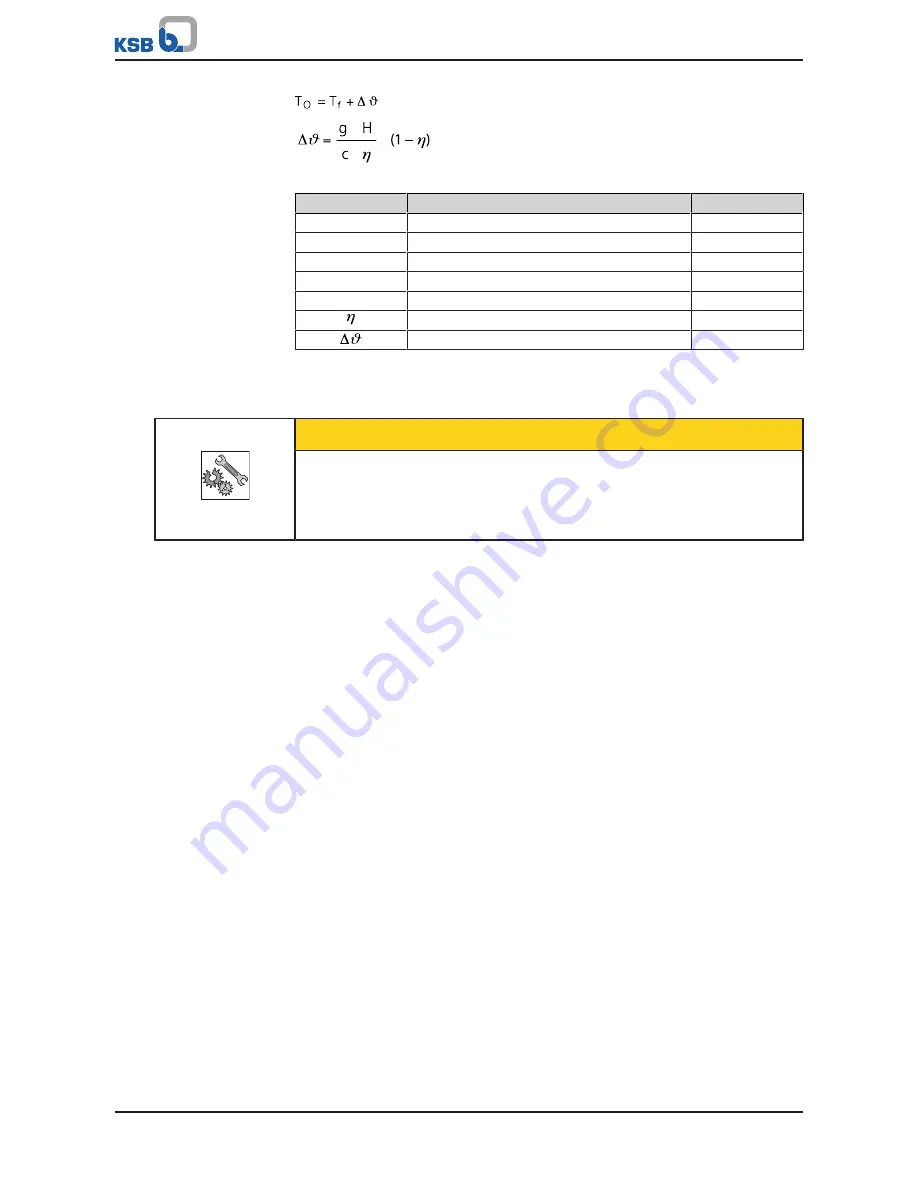
6 Commissioning/Start-up/Shutdown
36 of 72
HPK
×
×
×
Table 16:
Key
Symbol
Description
Unit
c
Specific heat capacity
J/kg K
g
Gravitational constant
m/s²
H
Pump discharge head
m
T
f
Fluid temperature
°C
T
O
Temperature at the casing surface
°C
Pump efficiency at duty point
-
Temperature difference
K
6.2.3.2 Density of the fluid handled
The pump input power changes in proportion to the density of the fluid handled.
CAUTION
Impermissibly high density of the fluid handled
Motor overload!
▷
Observe the information on fluid density in the data sheet.
▷
Make sure the motor has sufficient power reserves.
6.2.3.3 Abrasive fluids
Do not exceed the maximum permissible solids content specified in the data sheet.
When the pump handles fluids containing abrasive substances, increased wear of the
hydraulic system and shaft seal are to be expected. In this case, reduce the commonly
recommended inspection intervals.
6.3 Commissioning/start-up
6.3.1 Prerequisites for commissioning/start-up
Before commissioning/starting up the pump set, make sure that the following
conditions are met:
▪
The pump set has been mechanically connected as specified.
▪
The pump set has been properly connected to the power supply and is equipped
with all protection devices.
(
ð
Section 5.8, Page 31)
▪
The pump has been primed with the fluid to be handled. The pump has been
vented.
(
ð
Section 6.3.4, Page 39)
▪
The direction of rotation has been checked.
(
ð
Section 5.9, Page 33)
▪
All auxiliary connections required are connected and operational.
▪
The lubricants have been checked.
▪
After prolonged shutdown of the pump (set), the activities required for returning
the pump (set) to service have been carried out.
(
ð
Section 6.4, Page 44)
6.3.2 Filling in lubricants
Fill the bearing bracket with lubricating oil.
Oil quality see
(
ð
Section 7.2.3.1.2, Page 49)
Oil quantity see
(
ð
Section 7.2.3.1.3, Page 49)
Summary of Contents for HPK
Page 71: ......