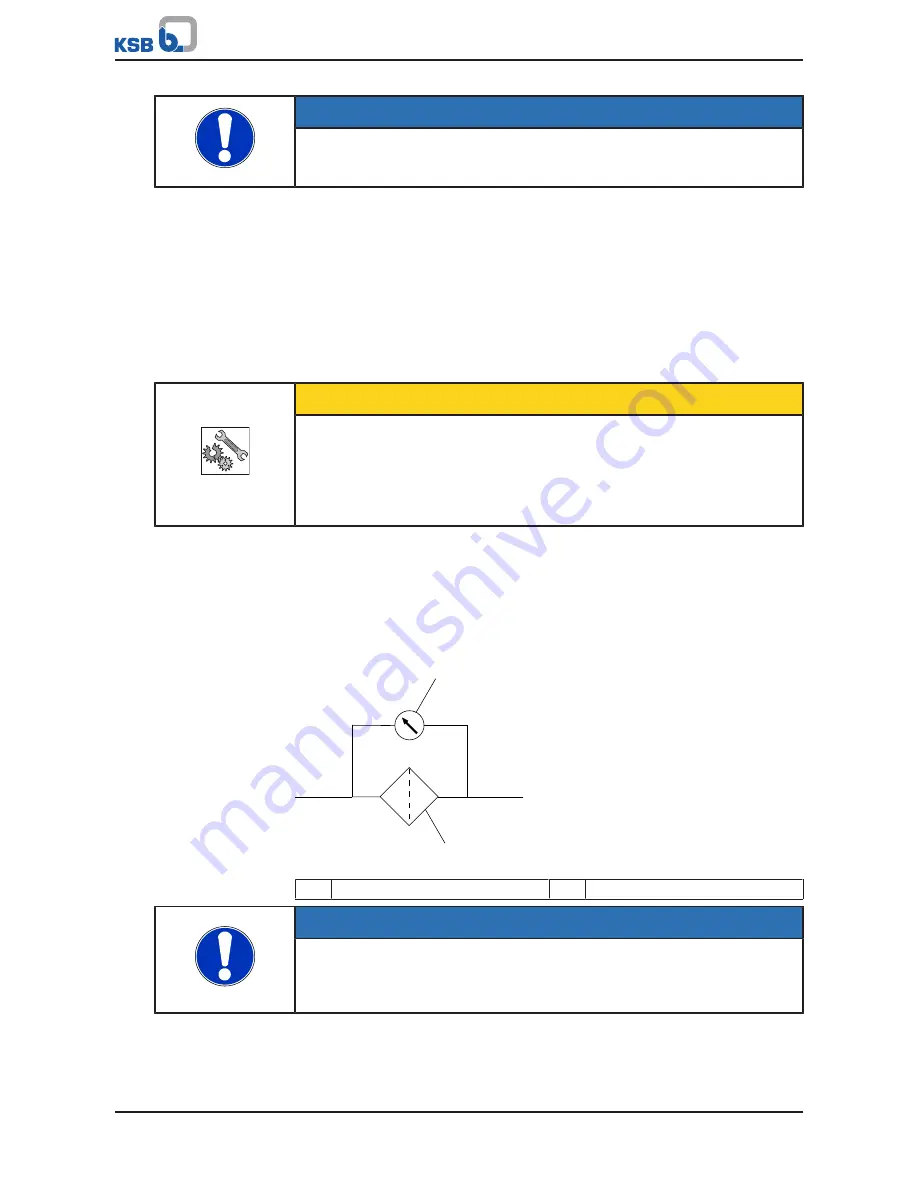
5 Installation at Site
26 of 72
HPK
NOTE
Installing check and shut-off elements in the system is recommended, depending on
the type of plant and pump. However, such elements must not obstruct proper
drainage or hinder disassembly of the pump.
ü
Suction lift lines
have been laid with a rising slope, suction head lines with a
downward slope towards the pump.
ü
A flow stabilisation section having a length equivalent to at least twice the
diameter of the suction flange has been provided upstream of the suction flange.
ü
The nominal diameters of the pipelines are at least equal to the nominal
diameters of the pump nozzles.
ü
Adapters
to
larger diameters have a diffuser angle of approximately 8° to
prevent excessive pressure losses.
ü
The pipelines have been anchored in close proximity to the pump and connected
without transmitting any stresses or strains.
CAUTION
Welding beads, scale and other impurities in the piping
Damage to the pump!
▷
Free the piping from any impurities.
▷
If necessary, install a filter.
▷
Comply with the instructions set out in
(
ð
Section 7.2.2.3, Page 48)
.
1.
Thoroughly clean, flush and blow through all vessels, pipelines and connections
(especially of new installations).
2.
Before installing the pump in the piping, remove the flange covers on the
suction and discharge nozzles of the pump.
3.
Check that the inside of the pump is free from any foreign objects. Remove any
foreign objects.
4.
If required, install a filter in the piping (see figure: Filter in the piping).
1
2
Fig. 9:
Filter in the piping
1
Differential pressure gauge
2
Filter
NOTE
Use a filter with laid-in wire mesh of 0.5 mm x 0.25 mm (mesh size x wire diameter)
made of corrosion-resistant material.
Use a filter with a filter area three times the cross-section of the piping.
Conical filters have proved suitable.
5.
Connect the pump nozzles to the piping.
Summary of Contents for HPK
Page 71: ......