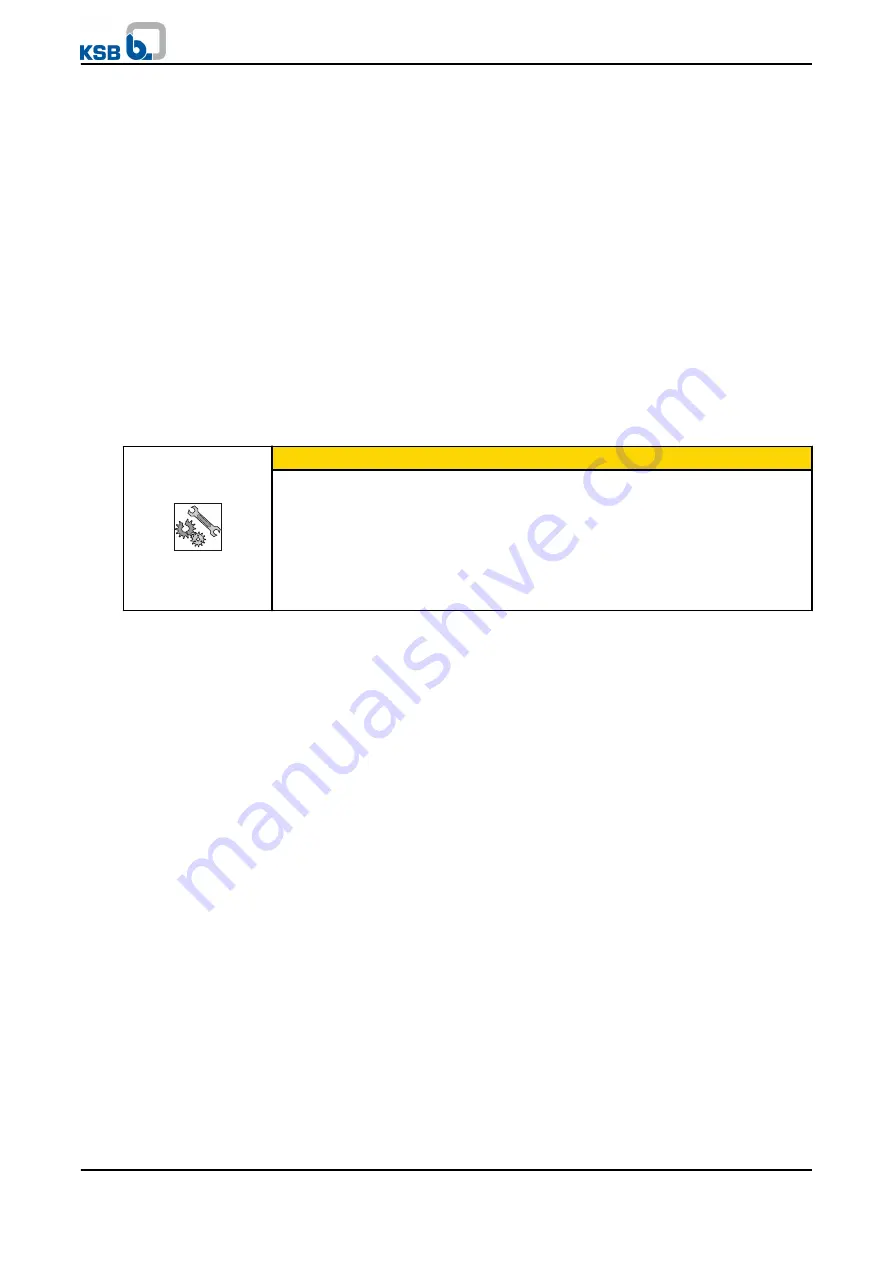
6
Commissioning/Start-up/Shutdown
6.1
Commissioning/start-up
6.1.1 Prerequisites for commissioning/start-up
Before starting up the pump set make sure that the following requirements are met:
▪
The pump set has been properly connected to the electric power supply and is
equipped with all protection devices.
▪
The pump has been primed with the fluid to be handled. (
▪
The direction of rotation has been checked. (
▪
All auxiliary connections required are connected and operational.
▪
After prolonged shutdown of the pump (set), the activities described in (
Section 6.4 Page 33) have been carried out.
6.1.2 Priming and venting the pumpe
CAUTION
Increased wear due to dry running
Damage to the pump set!
▷
Before starting up the pump set, vent the pump and prime it with the fluid to
be handled.
▷
Never operate the pump set without liquid fill.
▷
Never close the shut-off element in the suction line and/or supply line during
pump operation.
Pump without barrier fluid (standard version)
1. Open the shut-off elements in suction and discharge line.
2. Vent the pump and suction line and prime both with the fluid to be handled (for
at least 5 minutes).
3. Close the shut-off element in the discharge line.
4. Make sure that the pump does not drain through the suction line.
Pump with barrier fluid (option)
1. Open the shut-off element in the discharge line (suction line closed).
2. Fill the pump with barrier fluid through connection 10E (for at least five
minutes).
3. Close connection 10E.
4. Close the shut-off element in the discharge line.
5. Open the suction head/suction lift line.
6. For suction head operation: Vent the system up to the discharge-side shut-off
element.
7. For suction lift operation: Evacuate the pump and the suction line.
The min. permissible pressure is 0.1 bar (absolute).
8. Close all auxiliary connections (barrier fluid, flushing liquid, etc).
6 Commissioning/Start-up/Shutdown
28 of 60
Etaseco/Etaseco I
Summary of Contents for Etaseco C
Page 59: ......