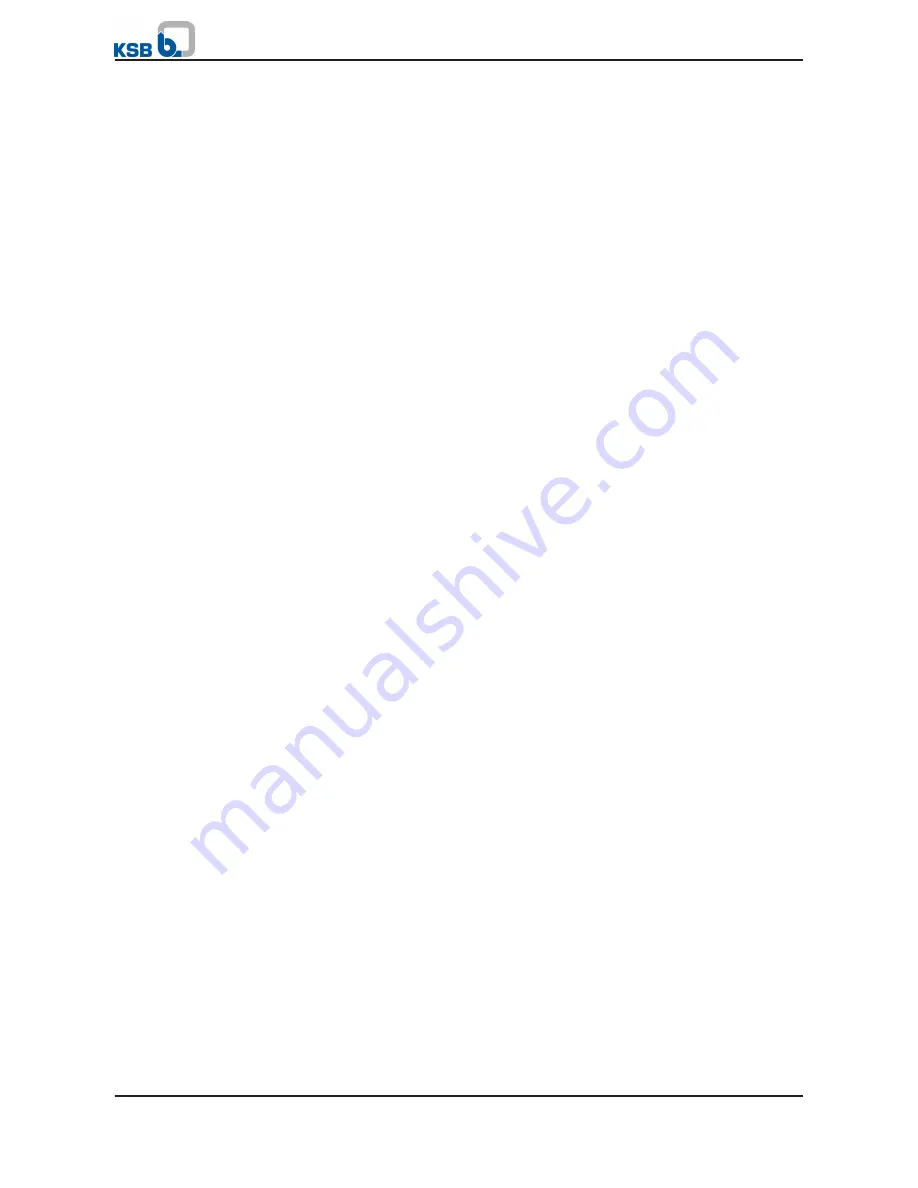
6
Commissioning/Start-up/Shutdown ........................................................................................... 24
6.1
Commissioning/start-up ...............................................................................................................................24
6.2
Operating limits ............................................................................................................................................24
6.3
Shutdown/storage/preservation ..................................................................................................................27
6.4
Returning to service .....................................................................................................................................28
7
Servicing/Maintenance ............................................................................................................... 29
7.1
Safety regulations .........................................................................................................................................29
7.2
Servicing/inspection ......................................................................................................................................30
7.3
Drainage/disposal .........................................................................................................................................33
7.4
Dismantling the submersible mixer .............................................................................................................34
7.5
Reassembling the submersible mixer ..........................................................................................................36
7.6
Tightening torques .......................................................................................................................................39
7.7
Spare parts stock ...........................................................................................................................................39
8
Trouble-shooting ........................................................................................................................ 42
9
Related Documents .................................................................................................................... 43
9.1
General assembly drawing with list of components ..................................................................................43
9.2
Flamepaths on explosion-proof motors ......................................................................................................47
9.3
Wiring diagrams ...........................................................................................................................................49
9.4
Forcing screws ...............................................................................................................................................51
10
Certificate of Decontamination ................................................................................................. 52
Index ............................................................................................................................................ 53
Contents
4 of 54
Amamix