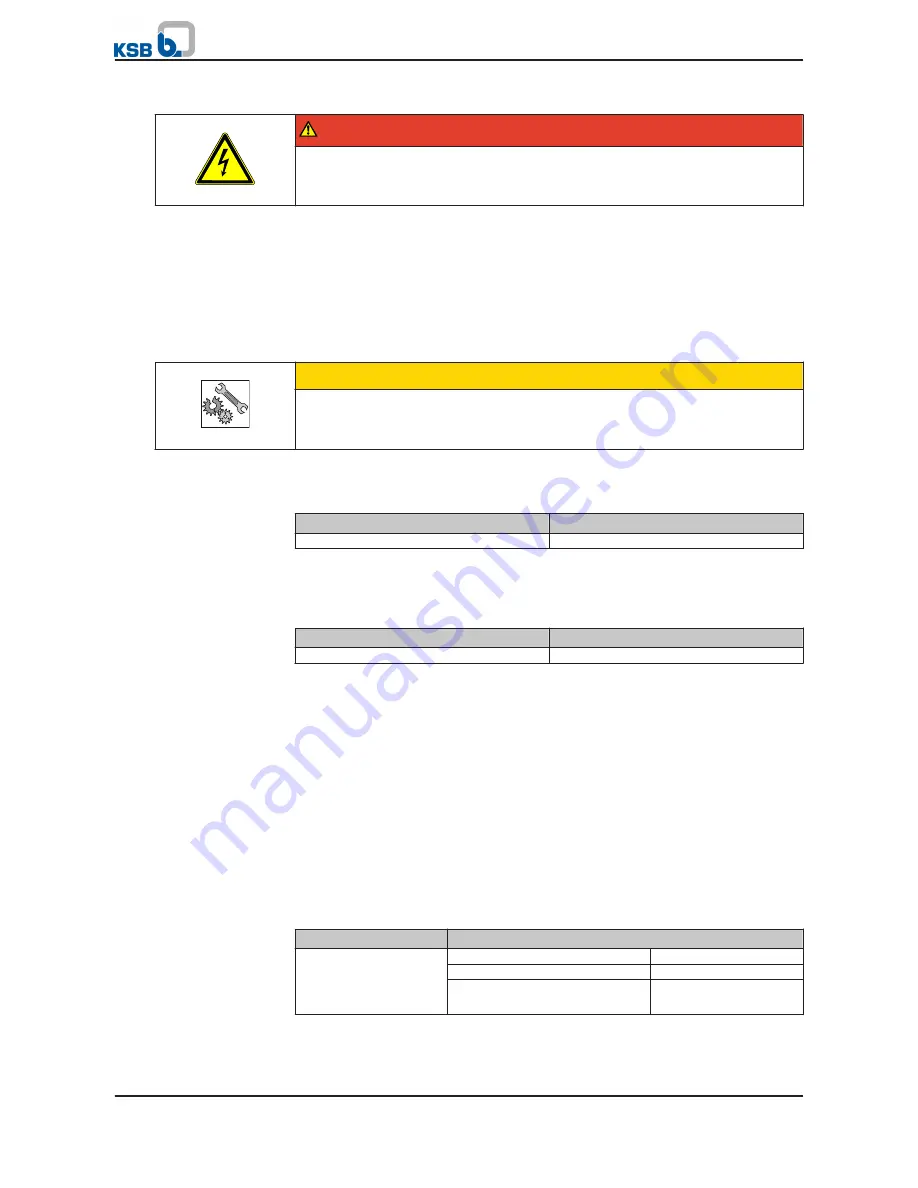
2.
Replace any damaged components by original spare parts.
DANGER
Defective ground conductor
Electric shock!
▷
Never switch on a submersible mixer with a defective ground conductor.
7.2.1.3
Checking the shackle/lifting rope
✓
The submersible mixer has been lifted out of the fluid handled and cleaned.
1.
Inspect the shackle/lifting rope and all fixing elements for visual damage.
2.
Replace damaged components by original spare parts.
7.2.1.4
Checking the sensors
CAUTION
Excessive test voltage
Damage to the sensors!
▷
Never test the sensors with voltages exceeding 30 V.
The tests described below measure the resistance at the core ends of the power
cable. The actual function of the sensors is not tested.
Table 8: Resistance measurement of the temperature sensors in the motor winding
Measurement between terminals ...
Resistance
10 and 11
100 Ω - 1000 Ω
If the tolerances indicated are exceeded, disconnect the power cable at the
submersible mixer and repeat the check inside the motor.
If tolerances are exceeded here, too, the winding will have to be replaced.
Table 9: Resistance measurement of the leakage sensors
Measurement between terminals ...
Resistance
9 and ground conductor (PE)
> 60 k
Ω
Lower resistance values suggest water ingress into the motor. In this case the motor
must be opened and overhauled.
If mechanical seal leakage is monitored, completely drain the oil chamber first, then
repeat the measuring procedure with the motor in horizontal position. If the
measured value is okay now, the motor is dry inside but the outboard mechanical
seal is defective.
7.2.1.5
Lubrication and lubricant change
7.2.1.5.1 Lubricant quality
The lubricant reservoir is filled at the factory with an environmentally friendly, non-
toxic lubricant of medical quality (unless otherwise required by the customer).
The following lubricants can be used to lubricate the mechanical seals:
Table 10: Oil quality
Description
Properties
Paraffin oil or white oil
Alternative: Motor oil
grades SAE 10W to SAE
20W
Kinematic viscosity at 40 °C
<20 mm/s
²
Flash point (to Cleveland)
+160 °C
Solidification point (pour point)
-15 °C
▪
Merkur WOP 40 PB, made by SASOL
▪
Merkur white oil Pharma 40, made by DEA
Visual inspection
Temperature sensors in
the motor winding
Leakage sensor in the
motor (also mechanical
seal leakage)
Recommended oil quality:
7 Servicing/Maintenance
Amamix
31 of 54