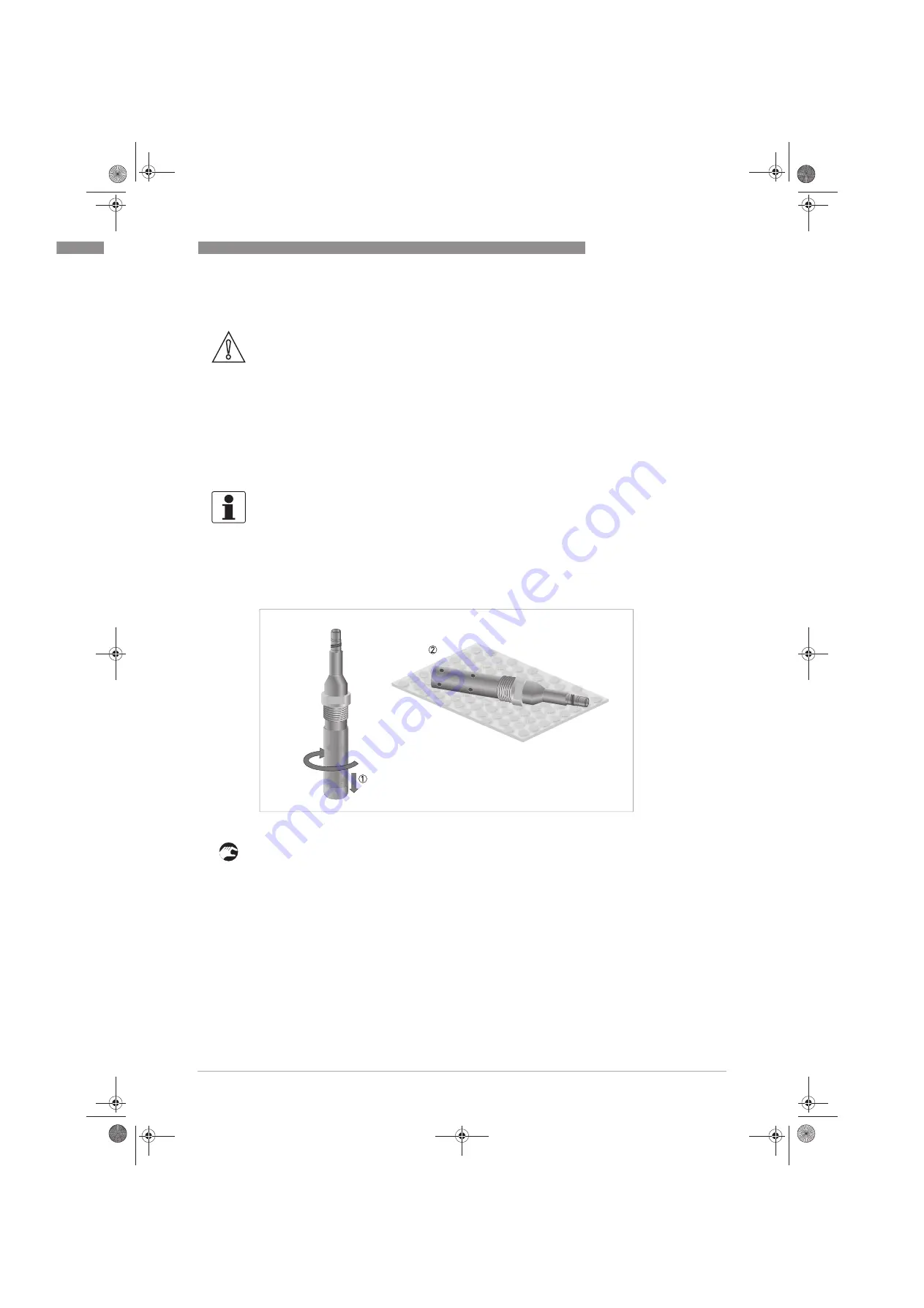
INSTALLATION
3
13
SMARTPAT COND 1200
www.krohne.com
09/2015 - 4003041501 - MA SMARTPAT COND1200 R01 en
3.3 Pre-installation requirements
The required steps are explained in the following sections.
Unpacking the sensor
•
Remove by gently twisting and pulling the protective cap from the sensor
1
.
•
Lay the sensor on a soft ESD mat or soft paper tissue
2
.
•
Leave the protection cap of the VP connector, as long as the sensor is not connected to the
cable.
CAUTION!
•
Do not drop the device! Handle the device with care!
•
Never touch or scratch the electrodes of the sensor.
•
Store the sensor in its original packaging in a dry, dust-free location. Keep it away from dirt. If
necessary, clean it. See cleaning procedure on page 29
.
•
Do not make any mechanical modifications to the sensor (electrodes shortened, drilled, bent
or scratched). This can result in the loss of proper functionality, as well as the rights under
the device warranty.
•
The sensor must be suitable for the temperature, pressure and medium conditions which are
specified (including chemical resistance).
INFORMATION!
A sensor specific DTM software for usage with PACTware
TM
FDT is available. The DTM software
is free of charge and available from CD (scope of delivery) or can be downloaded from the
KROHNE website (Downloadcenter).
Figure 3-1: Unpacking the sensor
MA_SMARTPAT_COND_1200_en_150902_4003041501_R01.book Page 13 Monday, September 21, 2015 4:33 PM