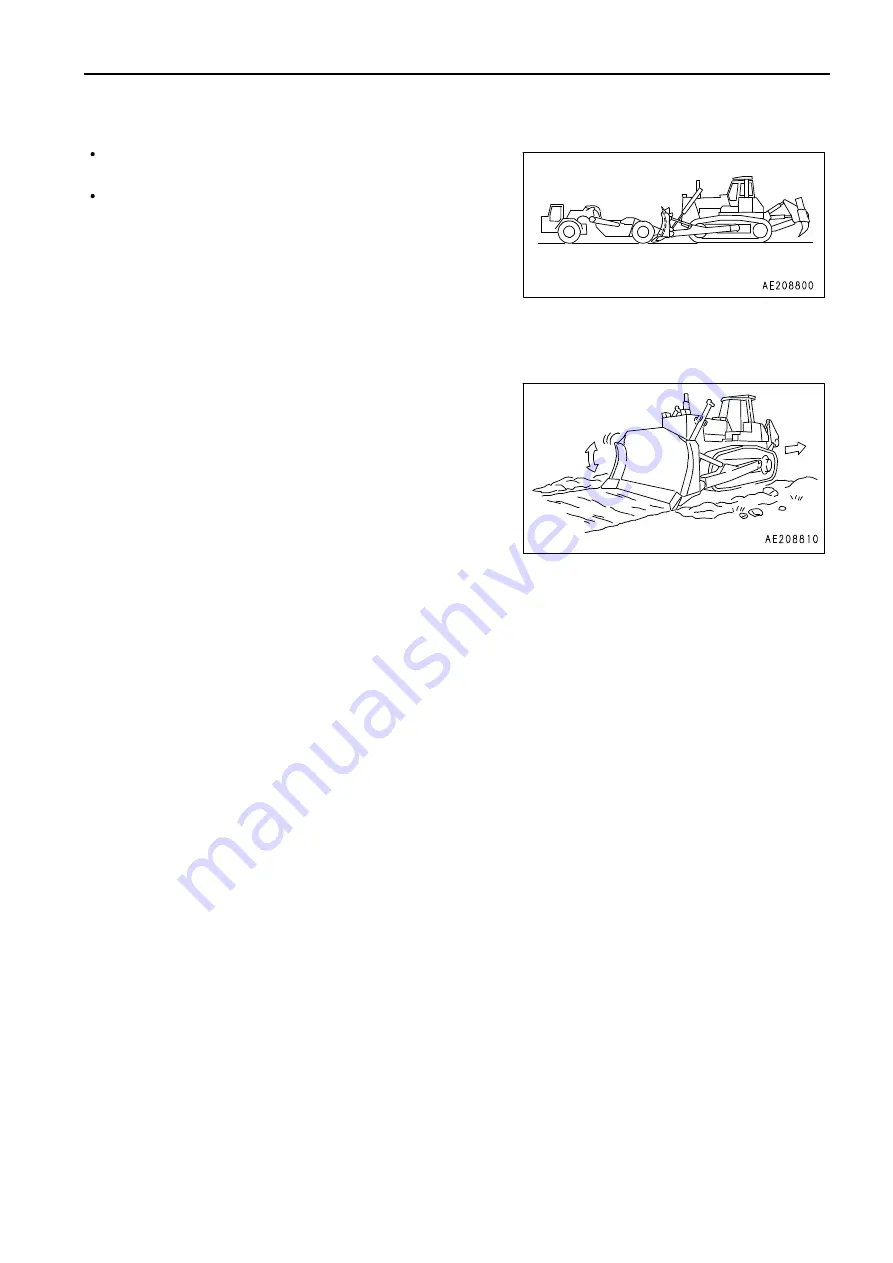
.
OPERATION
OPERATION
PUSHER OPERATIONS
When performing pusher operations, always install a pusher
plate.
When approaching the other machine, depress the decelerator
pedal to reduce the engine speed and approach slowly. After
coming into contact, raise the travel speed slowly and push with
full power.
SMOOTHING
NOTICE
Avoid smoothing on rocky or stony ground. It can damage the blade.
When finishing the ground surface to a smooth finish after digging or filling operations, keep a full load of soil in the
blade and operate the blade up or down in small movements while traveling forward. When leveling windrows or ruts
left by the tracks, set the blade to FLOAT position, travel at low speed in reverse and drag the blade over the ground
surface.
3 - 145
Summary of Contents for D475A-5E0
Page 2: ... 1 1 ...
Page 14: ... 2 1 ...
Page 53: ... ...
Page 54: ... 3 1 ...
Page 243: ... ...
Page 244: ... 4 1 ...
Page 301: ... MAINTENANCE SERVICE PROCEDURE MAINTENANCE SERVICE PROCEDURE A Right of machine 4 58 ...
Page 338: ... 5 1 ...
Page 340: ... 6 1 ...
Page 401: ... ...