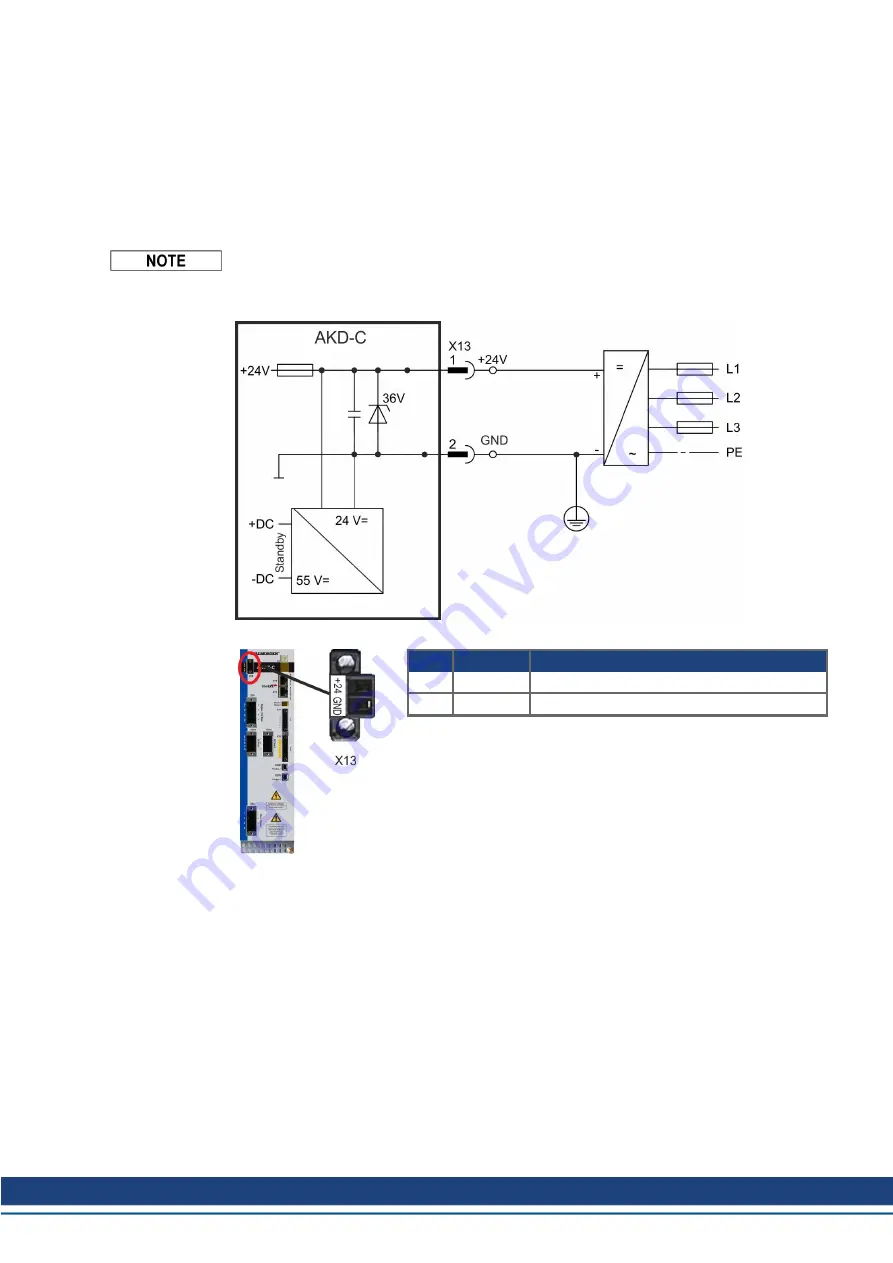
9.7.3 24 VDC supply voltage (X13)
The following diagram describes external 24 VDC power supply, electrically isolated, for
example, via an isolating transformer. The required current rating depends on the use of
motor brake and number of connected AKD-N drives.
The 24 VDC voltage is internally split into a control supply to power the AKD-C electronics
and a supply voltage to power the connected AKD-N drives in case of switched off AC mains
power.
Standby power is limited to 260 W at 24 V for both strings. This power must supply all AKD-
N ( 8 W each) and the remaining power can be used for motor holding brakes.
Pin
Signal
Description
1
+24
+24 VDC Auxiliary voltage
2
GND
24V Supply GND
AKD-C Installation | 9 Electrical Installation
Kollmorgen | kdn.kollmorgen.com | February 2018
63