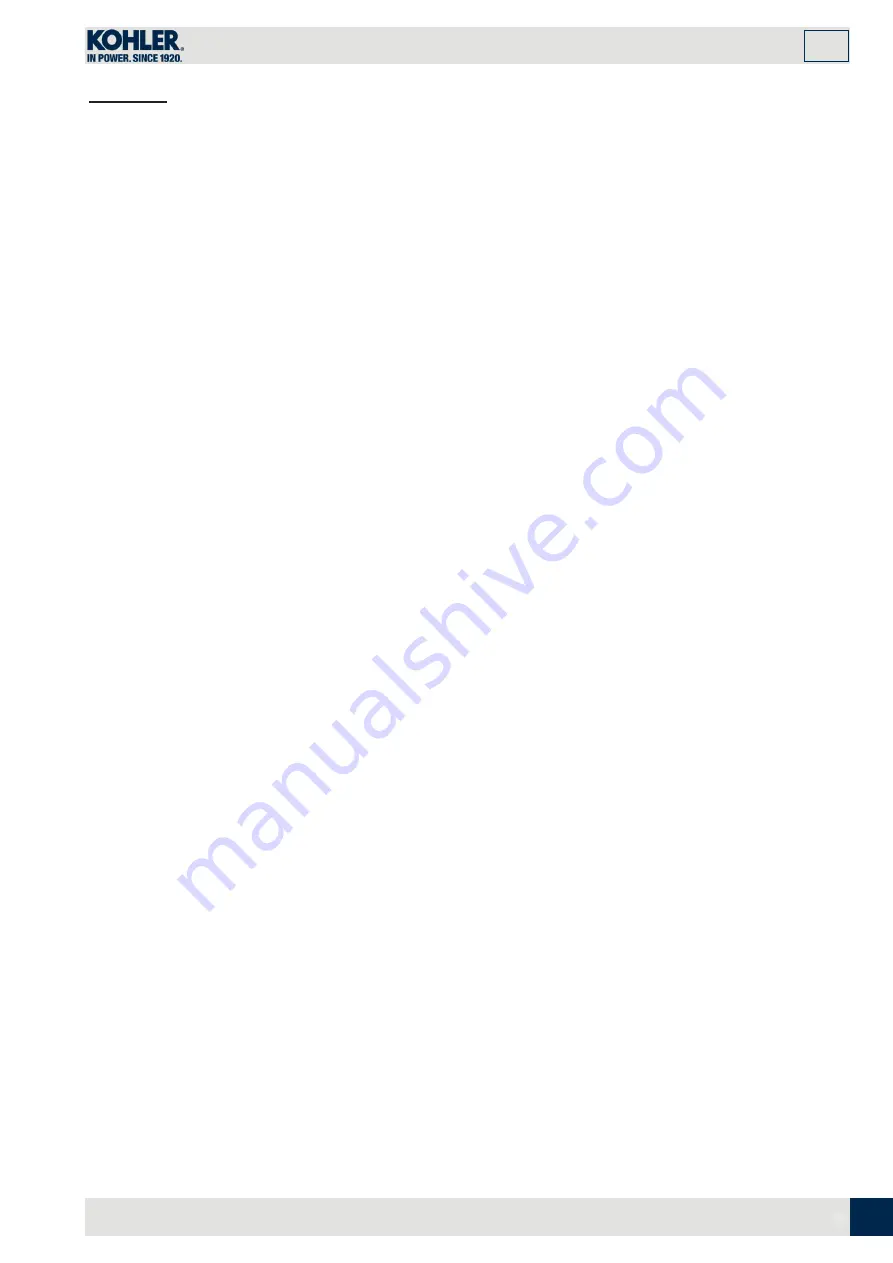
8
41
EN
INFORMATION ABOUT WARRANTY
COVERAGE
Kohler Co. will repair or replace emission control system parts, components and sub-assemblies found to be defective with
respect to materials or workmanship at no cost to you including engine exhaust system related diagnosis, labor and parts.
The choice and responsibility of the decision to repair or replace an emission control system defect will be solely that of Kohler
Co. Emission control system parts/ components covered by the Federal and California Emission Control Systems Limited
Warranty are listed below
-
Fuel injector(s)
-
Electronic control unit (ECU) if equipped
-
Injection pump(s)
-
Sensors associated with ECU operation
-
Exhaust manifold
-
Emission control information labels
-
Intake manifold
-
Turbocharger (if equipped)
-
Exhaust gas recirculation (EGR) tube
-
Fuel limiting device
-
Crankcase ventilation valve
Parts/components that are scheduled to be replaced as part of the required maintenance schedule will be covered under
the warranty provisions for a period of time up to the first scheduled replacement point for the subject parts/ components.
Subsequent damage to other engine components as a direct result of a warrantable failure an exhaust emission part/ component
will be covered under the warranty provisions described herein.
As the heavy-duty off-road engine owner, you should however be aware that Kohler may deny you warranty coverage if your
heavy-duty off-road engine or a part has failed due to abuse, neglect, improper maintenance or unapproved modifications.
Only due to the above reasons, the manufacturer may deny the warranty coverage.
Summary of Contents for KDI-2504TCR
Page 1: ...KDI 2504 TCR MGWI TP 7110 4 18 OWNER MANUAL...
Page 17: ...17 2 TECHNICAL INFORMATION EN...
Page 45: ..._01 45 EN NOTES...
Page 46: ..._01 46 EN NOTES...
Page 47: ..._01 47 EN NOTES...