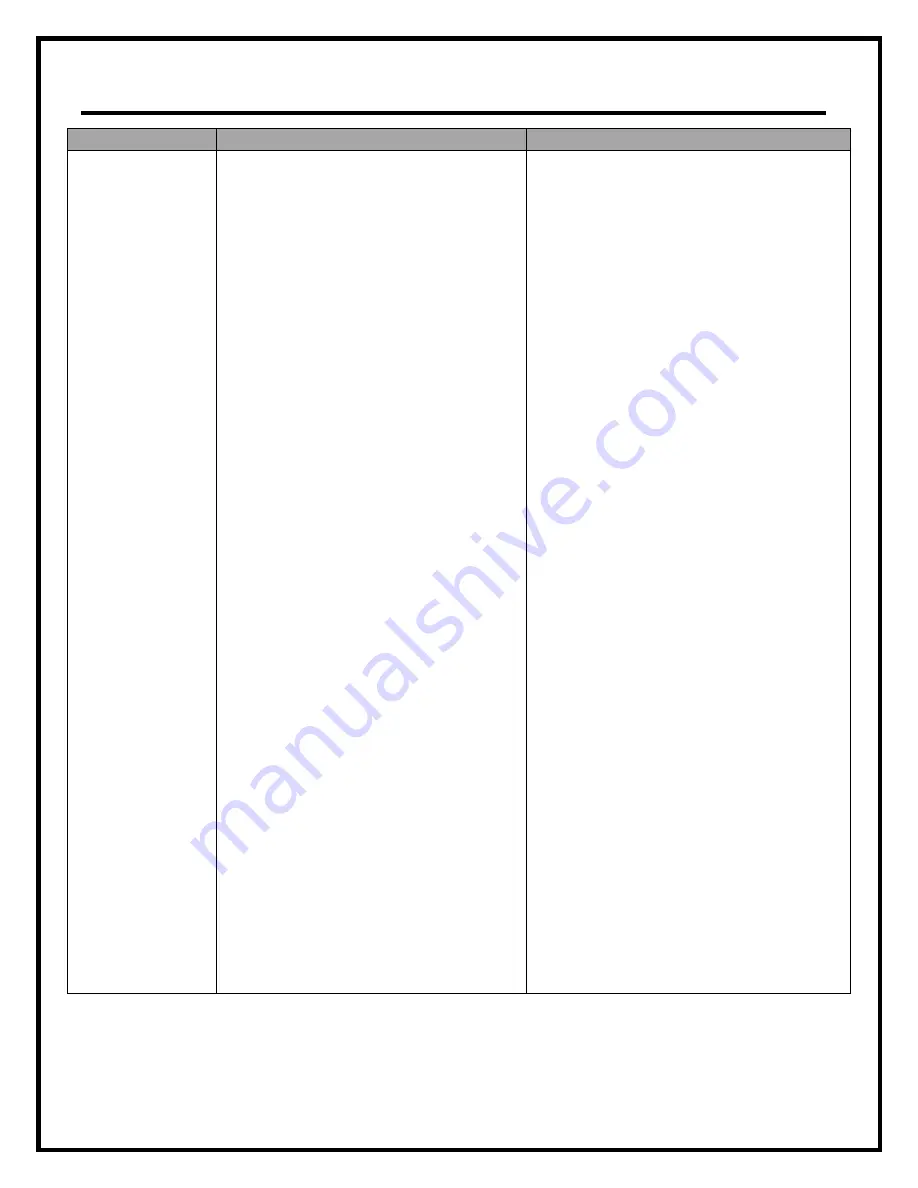
- 14 -
PROBLEM
POSSIBLE CAUSES
SOLUTION
Tool Won't Fire
1. No Klips in Magazine or last Klip on
Rack.
1. The Tool should NOT fire because
Sensor Shaft won’t allow the Safety to
disengage.
2. Door on Tool Nozzle is not fully closed
and locked.
2. Open and shut Door to make sure Door
Latch is locked.
3. Low air pressure at the Tool.
3. Check air supply to Tool. Make sure it is
at least 75 PSI (5.2 Bar) at the Tool.
Increase air pressure by 10 PSI (.69
Bar) increments up to a max of 110 PSI
(7.6 Bar).
4. O-Ring Seal on Tool's Piston is worn
or damaged.
4. Replace O-Ring on piston.
5. Trigger not functioning properly.
5. Inspect Trigger Assembly. Trigger may
not be functioning properly because of
dirt and debris in Assembly, wear to O-
rings [#205, #206, #209], or problems
with Secondary Trigger [#216]. Clean,
Repair or Replace.
6. Klips not feeding properly.
6. After checking that Klip Rack is full,
verify proper operation of Feeder.
Inspect for damage to Magazine [#445],
Hood [#446] or Stop Plate [#443] which
must be both working and in proper
position. Replace damaged parts.
7. Klips not in proper firing position.
Feeder not operating properly:
7. (a) Check air supply at Tool. Slow
recharge rate can be caused by
pressure drop. Make sure PSI is at least
75 PSI (5.2 Bar) at the Tool.
– OR –
(b) Inspect for defective / broken Feed
Spring [#441] or Push Spring [#437].
Replace damaged parts.
– OR –
(c) Sensor Shaft [#441] on Door not fully
dis-engaged. Check that Safety Unit is
functioning. Replace Safety Unit or
Sensor Shaft as required.
APPENDIX A: TROUBLESHOOTING
(con’t)
Summary of Contents for KTA-3 Series
Page 1: ...PN 10 00085 KTA 3 4 5 6 Series REBAR CONNECTOR TOOL OWNER OPERATOR MANUAL ...
Page 16: ... 16 APPENDIX B PARTS BREAKDOWN ...
Page 18: ... 18 ...
Page 20: ... 20 ...
Page 22: ... 22 ...
Page 24: ...PN 10 00085 ...