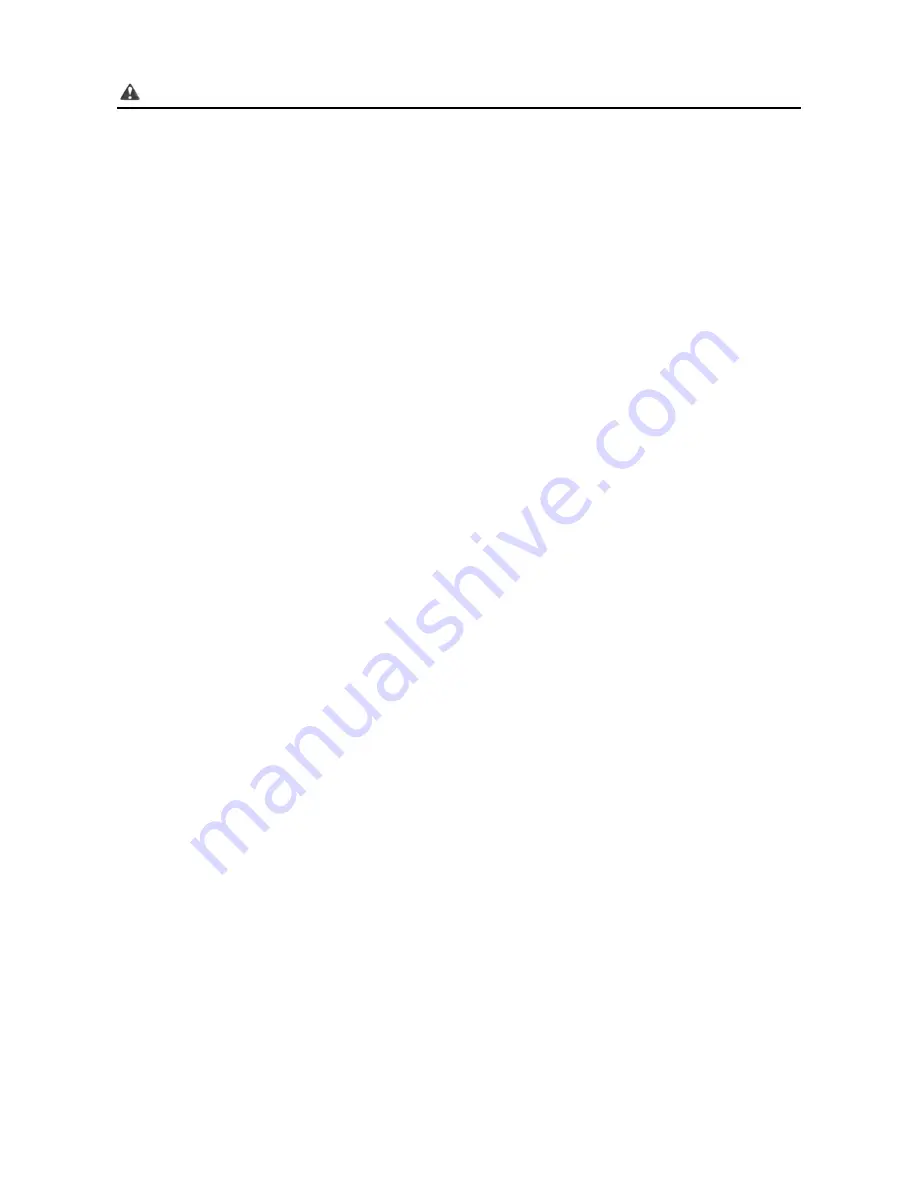
Please read the Operation Instructions carefully for safety.
1.4 Notes to post-operation
1) Park the loader on the flat ground. If loader
has to be parked on a slope, bucket shall fall
down to the ground. And place stop blocks
around wheels.
2) If driver leaves the cab,
·Bucket falls to the ground.
·Stop the engine and move operating lever to
release the pressure.
·Place operating lever of forward and backward
at the neutral position and lock the operating
lever of bucket at the neutral position.
·Take away the triggering key.
3) Before storage, cool the silencer and other hot
parts then close the protective hood. Otherwise
it may cause fire accident.
1.5 Notes to maintenance and service
1) Check and clean the loader and operating
parts. Stop the engine before each check,
adjustment and leave. It is dangerous to check
the running loader. Carry out any check at safe,
solid and flat ground.
2) During check and maintenance, identify the
serviced part with Label “In check and
maintenance” in order to avoid unessential
person from touching or operating the loader.
Place some warning marks around the loader.
3) Do not use materials that easily ignite fuel or
battery during mechanical maintenance and fuel
supply.
4) Ensure sufficient ventilation if maintenance is
done indoor or at place with poor ventilation
conditions. Local ventilation is a must when
exposure to waste gas, fuel, cleaning oil and
paint.
5) Use the approved service kits. Unapproved
service kits will not only reduce the working
efficiency but also cause injury.
6) Support and fix the engine hood and other
components before maintenance and check
around the engine.
7) Place the start button at Off position when
welding the loader. Do not place hazardous
materials between welding and earthing parts
because welding may generate heat and cause
the electrical spark. Otherwise energized cylinder,
sealing bearing and other devices may pose
danger.
8) Water in the electrical system can cause the
short circuit or abnormality. Keep battery,
sensor, connection and other electrical parts
away from water.
9) Wear goggles and position the oil leakage with
heavy board if leakage is found in a invisible small
aperture. If oil touches the skin, it may irritate skin
seriously. Seek for physicians immediately.
10) Cool the engine completely before check,
addition or change of cooling water in the radiator.
Silencer is hot just after engine stops. Touch can
cause the injury!
11) Lock the operating lever before check and
maintenance on the lifting bucket. Use the
support of lifting arm to prevent them from
descending.
12) Do not lift the loader with bucket before
service and maintenance. Do not allow persons
under lifted loader. If some persons have to
work under the lifted loader, place the safety mat
and support in advance to avoid unexpected
falling. And lock the operating lever.
13) Do not use any tyre with serious damage.
Otherwise it may burst.
14) Consult the distributor of tyre, inner tube and
wheel rim for replacement and repair.
(Replacement and repair shall be done by
specially trained expert if possible.)
4
Summary of Contents for KDD03
Page 2: ......