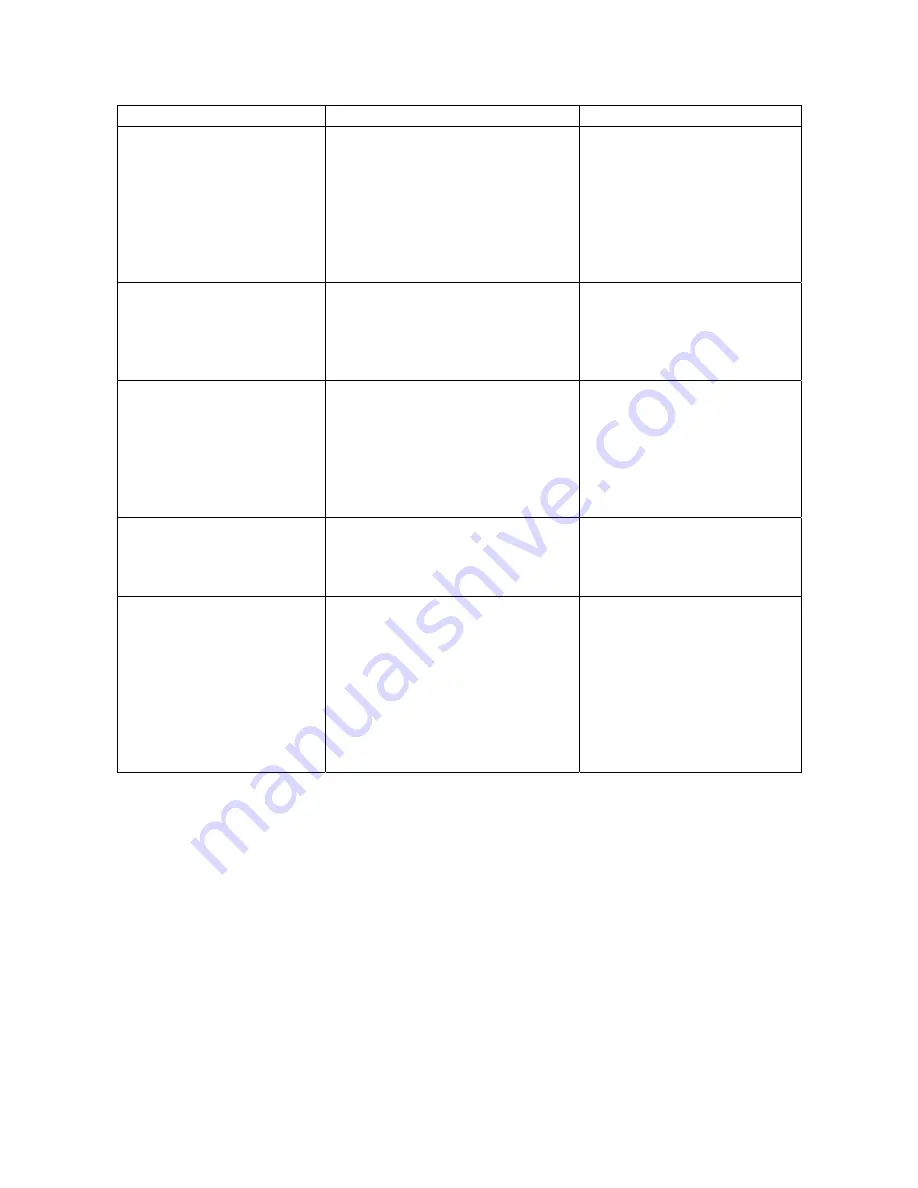
22
Problems Causes Solutions
Inappropriate embedded
depth.
The time of the ultrasonic
transmission is insufficient. The
drop rate is faster than the plastic
melting rate.
The embedded object is too long.
The pressure or energy efficiency is
bad.
The height is inappropriate.
Increase the welding time.
Decrease the drop rate.
It takes a relative long time
to embed in a normal
position.
The power of the ultrasonic
equipment is insufficient.
The unmber of hole too many.
The bore is too narrow.
The drop rate is too slow.
Use a model with higher
power.
Shorten the embedded object.
Increase the drop rate.
It takes a relative long time
to embed in a normal
position.
The embedded object is blocked in
the bore.
The lower part of the embedded
object is inappropriately supported
and the ultrasonic energy cannot be
distributed over the plastic around
the embedded object.
Reduce the pressure or
delay-on time
The base should be firm and
rigid and directly support the
lower part of the bore.
The plastic fills up the nut
bore.
The length of the embedded object
is greater than the depth of the
bore; i.e., the bore is too shallow.
After a short operation, an
indentation is found on the
ultrasonic welding head.
The material of the embedded
object is softer than that of the
welding head.
The amplitude of the ultrasonic
wave is too high.
Too many conditions affecting the
embedding.
It is difficult to fuse the plastic.
Use a harder material for the
welding head.
Reduce the amplitude.