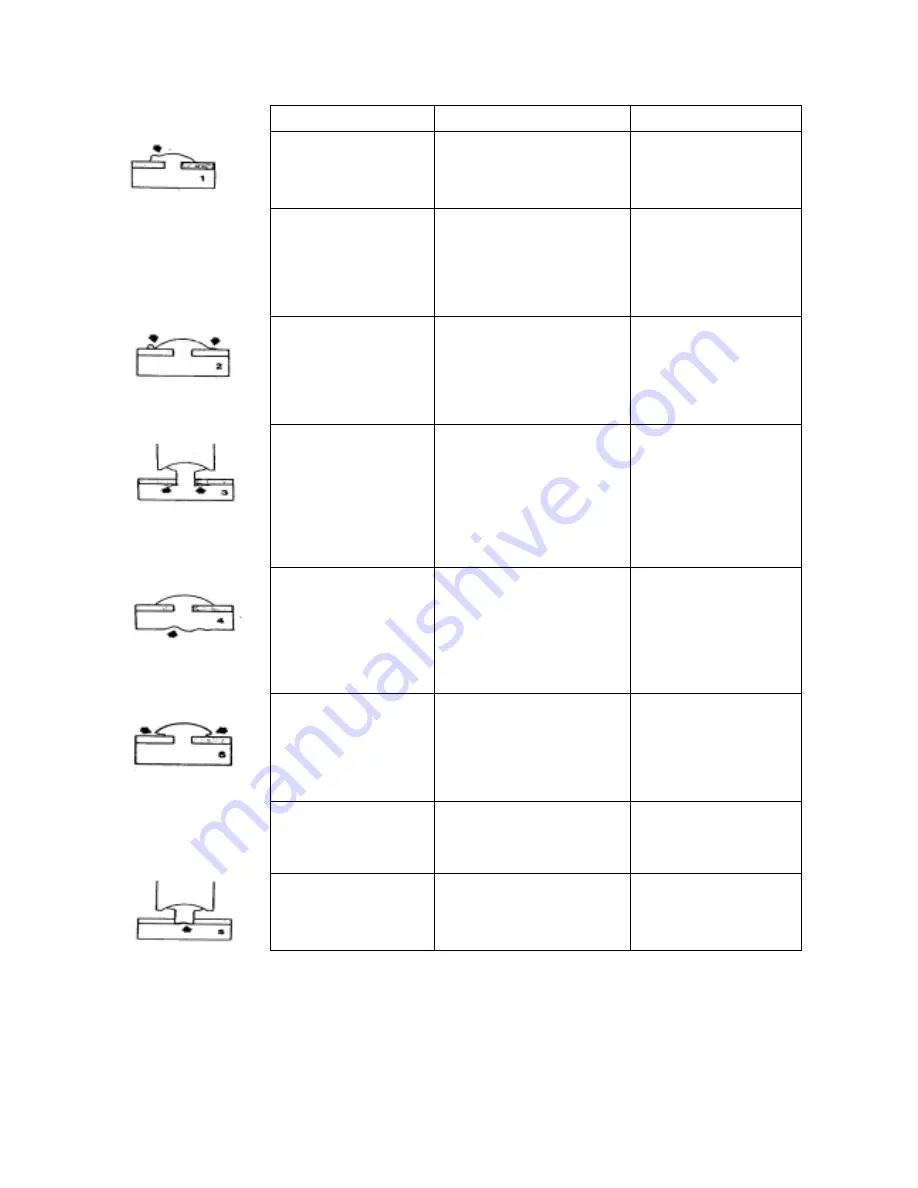
20
(2) Riveting
Problems Causes Solutions
The riveting point is
uneven and dented.
The rivet bore is too big or
the rivet is too small.
Reduce the size of the
rivet bore or increase the
height of the rivet.
Residual flash appears
around the riveting
point.
The rivet bore is too small or
the rivet is too big.
The rivet is not aligned with
the center of the rivet bore on
the welding head.
Increase the size of the
rivet bore or reduce the
height of the rivet.
Check alignment.
The top of the rivet is
slightly formed, but the
bottom of the rivet
starts melting and
collapsing
The pressure is too high or
the efficiency of the
amplitude is bad.
The drop rate of the welding
head is too high.
Reduce the pressure or
increase the amplitude.
Use a slower rate.
The backside of the
rivet bottom is
damaged.
The base has improper
supports.
The pressure is too high.
Try to use a metal
support for the base.
Reduce the pressure and
place a metal plate
between the rivet and
base to dissipate heat and
reduce the risk of danger.
After riveting, the
work-piece remains
loose.
The melted rivet does not
completely cure before the
pressure is removed.
The stroke of the welding
head is not long enough.
Extend the curing time
or use an additional
appliance for complete
curing.
Increase the stroke.
After riveting, the root
of the rivet is broken.
Stress is concentrated on the
root of the rivet due to the
sharp angle.
The welding head is not
vertical to the rivet.
Blunt or curve the root of
the rivet.
Check alignment.
The plastic slides
during welding.
The metal parts are not
properly placed on the
plastic.
Use an additional clamp.
The rivet is riveted
inappropriately.
Insufficient welding time.
Increase the welding
time.