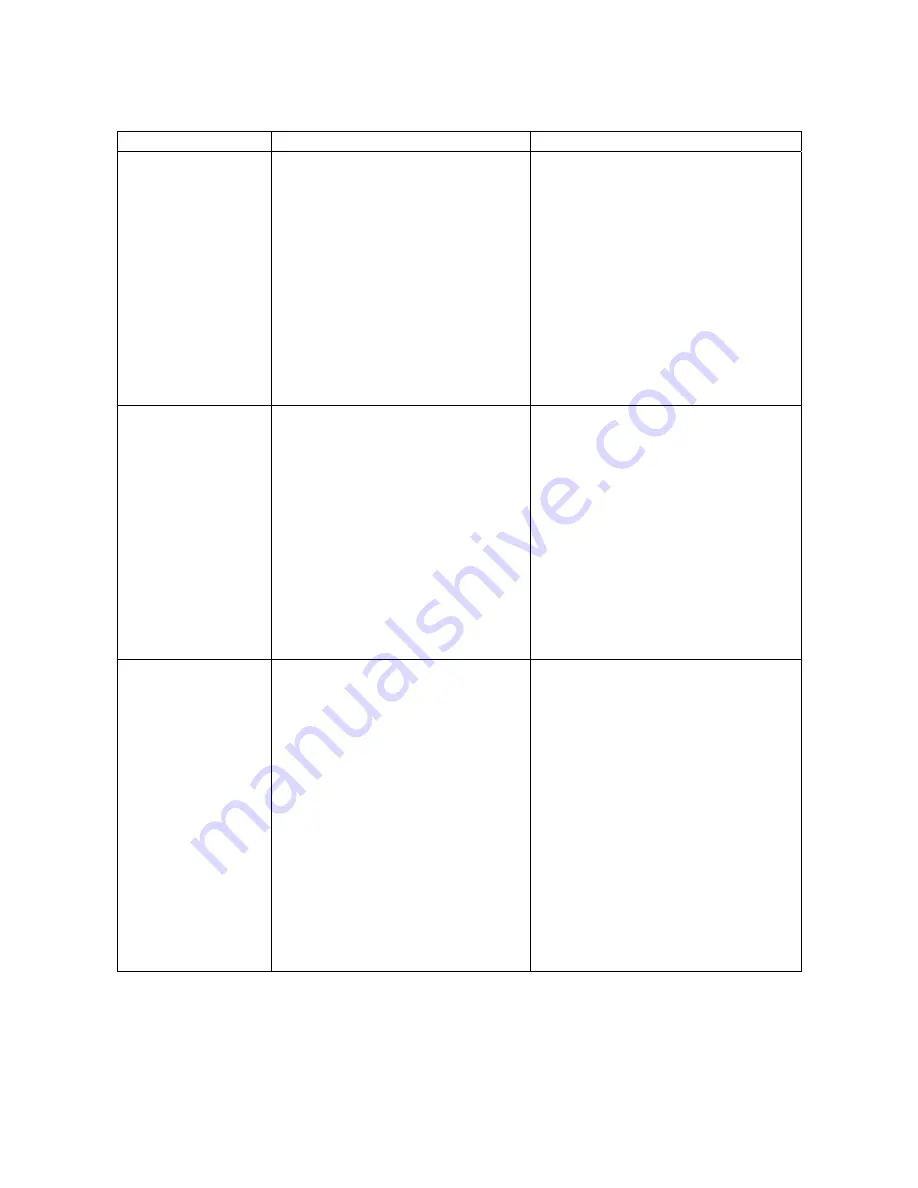
18
V (Welding problems and solutions)
(1) Welding
Problems Causes
Solutions
Surface damage
The shape of the welding head is
damaged.
The welding time is too long.
Bad bonding between the contact
surfaces of the welding head,
work-piece, and base.
Check the work-piece size.
Check the variation of the work-piece
between the molds.
Increase the pressure or amplitude to
reduce the welding time.
Adjust the buffer pressure.
Check if the welding head and base
are parallel.
Check the bonding between the
welding head and work-piece.
Check the bonding between the base
and work-piece.
Underlay the base, if required.
Burrs and flashes
over the joint face
The energy conducting point is too
big.
Deformation of the work-piece may
have a great effect.
The welding time is too long.
The thickness of the joint face is not
even.
The work-piece is too tight.
Reduce the size of the energy
conducting point.
Decrease the welding time.
Decrease the pressure.
Decrease the effect of the
deformation.
Decrease the welding time.
Re-design the joint face.
Check the operation conditions.
Reduce the bonding of the
work-piece.
Reduce The tolerance of the
work-piece.
The work-piece can’t
be aligned after
welding.
When assembling, the work-piece is
not aligned.
The base has improper support.
The sidewall bends.
Bad design of the energy conducting
point.
Tolerance of the work-piece is too
high.
Add a stud between two work-pieces.
If possible, design a new gauge for
correction.
Re-design an appropriate support.
Underlay the base.
Add hard supports if the bakelite plate
tilts.
Add ribs to the sidewall of the
work-piece.
Add hard supports if the bakelite plate
tilts.
Re-design the energy conducting
point.
Reduce the tolerance of the
work-piece.
Check the operation conditions.