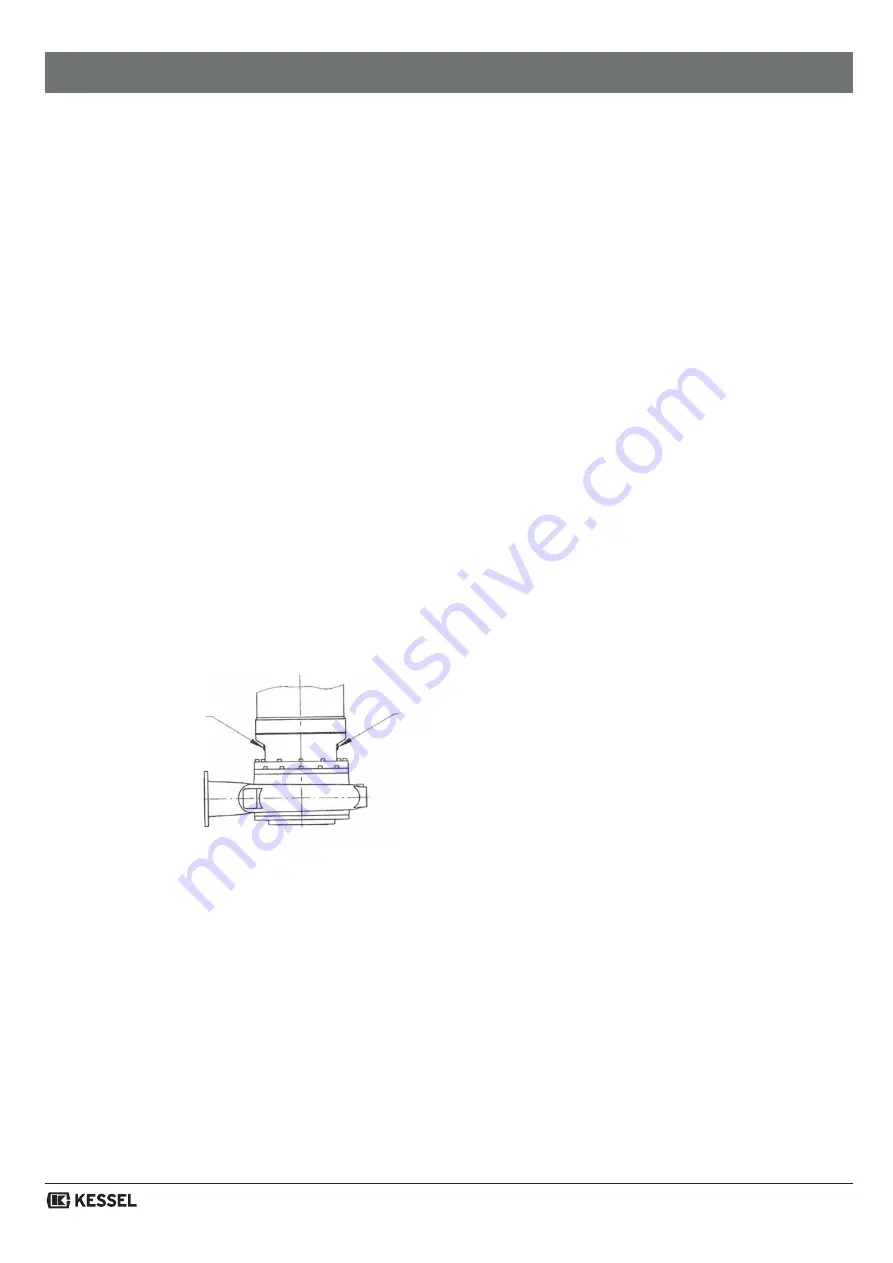
40 / 72
Regular maintenance
V 1.0
6
Regular maintenance
6.1
General points
The entire system must be checked and serviced at regular intervals.
The following points must be taken into account:
• The operating instructions must be available to the maintenance staff and be heeded. Only maintenance work
and measures described here may be carried out.
• All maintenance, inspection and cleaning work on the machine and system must be carried out with the greatest
care, at a safe workplace and by trained specialists. The necessary personal protective equipment must be
worn. The machine must be disconnected from the mains power supply for all work. Unintentional switch-
on must be prevented. In addition, all work in reservoirs and/or tanks must observe the respective protective
measures in accordance with BGV/GUV.
• Electrical work on the machine and the system must be carried out by specialists.
• Make sure that the required tools and material are available. Tidiness and cleanness guarantee safe and perfect
work at the machine. Always remove used cleaning materials and tools from the machine after work. Store all
materials and tools in the designated place.
• Operating media (e. g. oils, lubricants etc.) must be collected in suitable tanks and disposed of according to the
regulations (in accordance with directive 75/439/EEC and decrees in accordance with §§5a, 5b AbfG [German
Waste Law]). Appropriate protective clothing must be worn during cleaning and maintenance work. This must be
disposed of according to waste key TA 524 02 and EC directive 91/689/EEC. Only the lubricants recommended
by the manufacturer may be used. Oils and lubricants must not be mixed. Only use genuine spare parts from
the manufacturer.
A test run or functional test on the machine may only take place under the general operating conditions.
6.2
Maintenance dates
Once a month:
Check current consumption and voltage
Check the control units used, seal chamber check etc.
Every six months:
Visual inspection of the power supply cables
Visual inspection of accessories
3,000 operating hours: Visual check of pumps with oil boom chamber
8,000 operating hours or after 2 years at the latest:
Check on insulation resistance
Changing the operating fluid in seal chamber
Functional check on all safety and monitoring devices
In addition, the normative specifications concerning the inspection and maintenance of lifting stations must be
heeded.
Oil screw
Oil screw
Summary of Contents for Aqualift F XXL 400 litres 50 Hz Series
Page 49: ...KESSEL Aqualift F XXL 400 KESSEL Aqualift F XXL 800 50 Hz 2016 11 010 985 SDS 100...
Page 53: ...53 72 V 1 0 1 2 KESSEL 1 3 KESSEL 1 4 www kessel de 1 4 1 1 4 2 KESSEL 1 4 3 KESSEL KESSEL...
Page 55: ...55 72 V 1 0 2 2 1 DIN ANSI 2 2 CE EC EC VDE CE 2 3...
Page 56: ...56 72 V 1 0 2 4 2 5 2 5 1 EMC 2 5 2 IP 68 2 6...
Page 57: ...57 72 V 1 0 2 7 2 8 2 9 kW 40dB A 70dB A...
Page 59: ...59 72 V 1 0 4 4 1 4 2 4 3...
Page 61: ...61 72 V 1 0 1 1 5 3 5 4...
Page 63: ...63 72 V 1 0 5 9 5 2 5 1...
Page 64: ...64 72 V 1 0 6 6 1 BGV GUV 75 439 EWG AbfG 5a 5B TA 524 02 EC 91 689 EEC 6 2 3000 8000 2...
Page 65: ...65 72 V 1 0 6 3 3 KESSEL KESSEL 0 1 3 4...
Page 67: ...67 72 V 1 0...
Page 68: ...68 72 V 1 0 8 8 1 5 8 2 40 8 3...
Page 69: ...69 72 V 1 0 9...
Page 70: ...70 72 V 1 0 2 2 KESSEL...