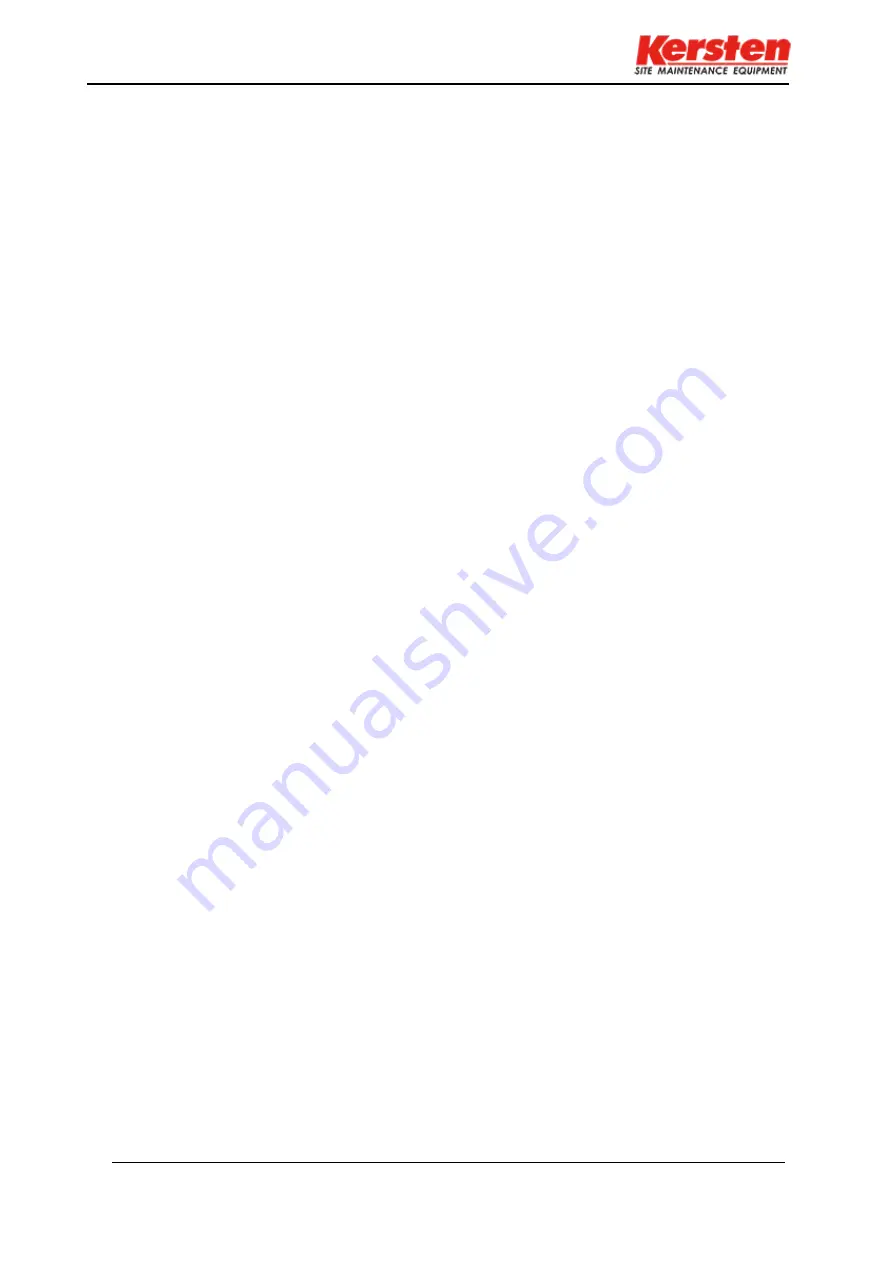
18
Maintenance
8.3 Maintenance after 20 operating hours or longer downtime
•
At regular intervals and at the beginning and end of the season, the moving parts of the unit
must be greased or oiled.
•
There is a grease nipple below the device receptacle on the basic unit, which it regularly
lubricates.
•
Regularly grease the mounting of the attachment or the pick-up tube of the self-propelled work
machine.
•
Lubricate or lubricate Bowden cables as required
•
Hydraulic oil and filter change for the first time after 20 operating hours, then every 100 operating
hours. Change the hydraulic oil filter at the same time interval as the oil change. (used oil type
see chapter for technical data)
8.4 Maintenance after 100 operating hours
•
Fan housing after every 100 operating hours or min. Take off once a year - preferably before the
season - and clean the cooling fins on the cylinder and cylinder head as well as the baffles,
cooling air strainer and oil cooler necessary for air circulation.
•
Hydraulic oil and filter change for the first time after 20 operating hours, then every 100 operating
hours. Change the hydraulic oil filter at the same time interval as the oil change. (used oil type
see chapter for technical data)
•
Cleaning the spark plug of soot deposits with a wire brush followed by checking the distance
between the electrodes. The electrode distance should be approx. 1 mm. Renew spark plugs
after 200 operating hours.
•
Clean the air filter cartridge at the latest after 100 hours of operation and in very dusty conditions
after a few hours
8.5 Storage
If the machine is not used for a long time, the following measures are recommended:
1.) Perform cleaning
2.) Preserve the motor (observe the instructions of the motor manufacturer)!
•
Completely drain fuel or top up fuel tank, add fuel stabilizer to fuel.
•
Run the engine for approx. 1 minute
•
Add one teaspoonful (approx. 0.03 ltr.) Of engine oil to the spark plug opening and
then slowly crank the engine.
•
Reinstall the spark plug and do not attach the spark plug connector. Pull on the
starter handle until the compression resistance is felt, thus the valves are closed.
•
Every two to three weeks, crank the engine slowly and pull it again until the
compression resistance is felt.
3.) Jack drive wheels
•
Using wooden blocks, jack up the machine so that the drive wheels are not resting
on the ground. Pay attention to stability!
4.) Subordinate the machine
•
To prevent corrosion, protect the machine from weathering. Do not store the
machine in damp rooms, fertilizer storage or stables.
5.) Cover the machine with a cloth or similar.