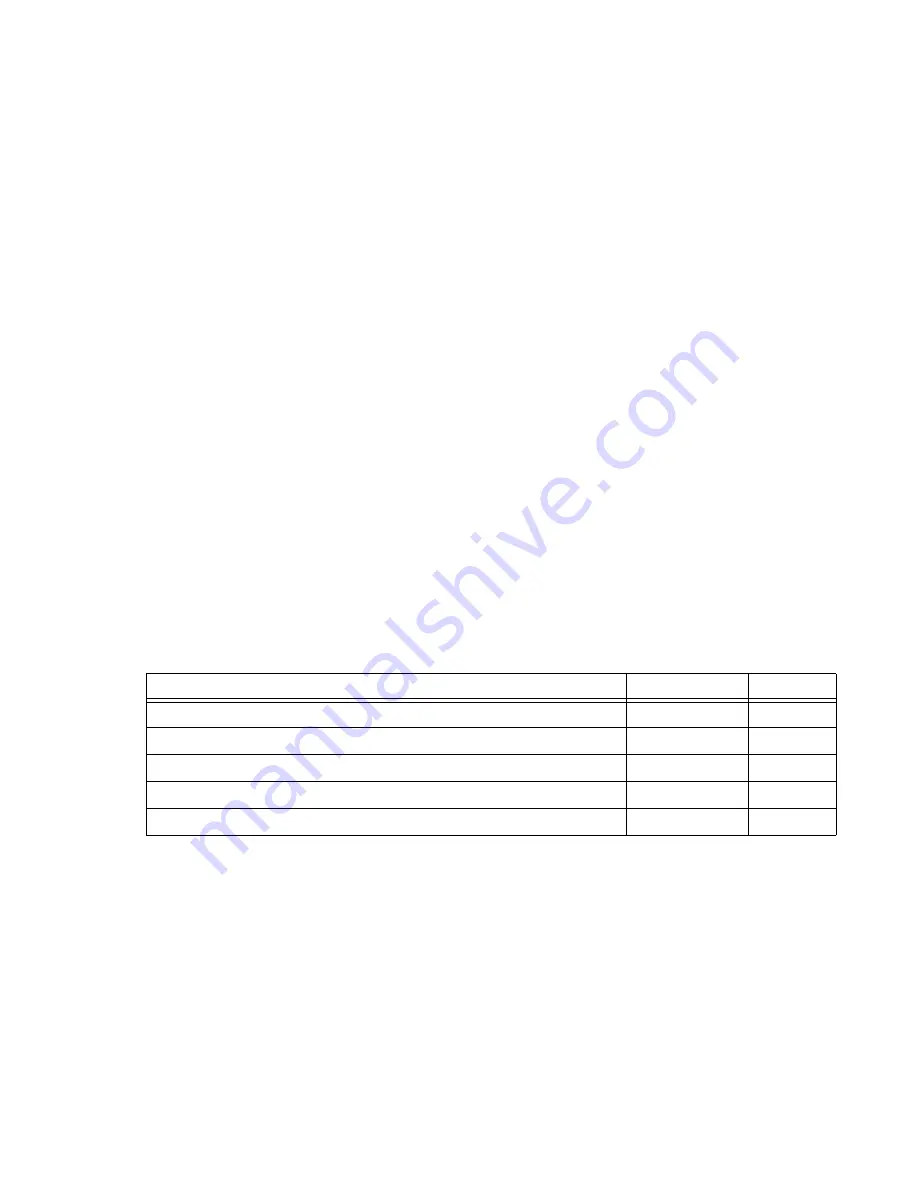
KLP 070312
1-11
c.
Fan failure (FAN).
Monitors all three internal cooling fans; trips if failure of any fan.
d.
Output Lead Fault (OLF)
. Monitors output power and sense leads; trips if any discontinuity
(open circuit) is detected in load connections.
e.
Source Power Loss (PWR).
Monitors internal d-c bus voltage at output of PFC; trips if low
a-c input or PFC failure occurs.
1.5.10
INTERNAL RELAY
An internal relay provides common, normally open and normally closed contacts available to the
user via the analog I/O connector. This relay is normally programmed (factory default) to ener-
gize upon detection of a system fault (FLT mode); see PAR. 1.5.9 for a list of faults. The relay
may also be programmed to be energized at the user’s discretion from the front panel (MAN
mode), or as part of a user-specified program using LIST commands (LIST mode). Refer to
PAR. 3.2.16.1 for details.)
1.5.11
MASTER/SLAVE CONTROL [STANDARD MODELS ONLY]
For applications that require the use of multiple standard KLP power supplies in either series
(for higher voltage) or parallel (for redundancy or higher current) the master/slave feature allows
a single power supply (the master) to automatically control both outputs to achieve the desired
output. Refer to PAR. 2.7.8 and 3.2.13 for details.
1.6
EQUIPMENT SUPPLIED
Equipment supplied with the unit is listed in Table 1-4.
1.7
ACCESSORIES
Accessories for the KLP Power Supply are listed in Table 1-5.
1.8
SAFETY
There are no operator serviceable parts inside the case. Service must be referred to authorized
personnel. Using the power supply in a manner not specified by Kepco. Inc. may impair the pro-
tection provided by the power supply. Observe all safety precautions noted throughout this man-
ual. Table 1-6 lists symbols used on the power supply or in this manual where applicable.
TABLE 1-4. EQUIPMENT SUPPLIED
ITEM
PART NUMBER
QUANTITY
Source power connector
142-0381
1
Jumper (24 AWG or larger bus wire) for local sensing connections
172-0585
2
Analog I/O port mating connector
142-0528
1
Quick Start Guide
228-1616
1
Nut, 1/4-20, with captive lockwasher (on output studs of 10V, 20V and 36V models only)
102-0175
2
Summary of Contents for KLP 10-150-2
Page 2: ......
Page 6: ......
Page 12: ...vi KLP070312 FIGURE 1 1 KLP SERIES POWER SUPPLY...
Page 19: ...KLP 070312 1 7 FIGURE 1 3 KLP SERIES POWER SUPPLY MECHANICAL OUTLINE DRAWING SHEET 1 OF 2...
Page 20: ...1 8 KLP 070312 FIGURE 1 3 KLP SERIES POWER SUPPLY MECHANICAL OUTLINE DRAWING SHEET 2 OF 2...
Page 27: ...KLP HV 070312 2 3 FIGURE 2 2 KLP SERIES REAR PANEL SWITCH AND CONNECTORS...
Page 40: ......
Page 78: ......
Page 90: ......