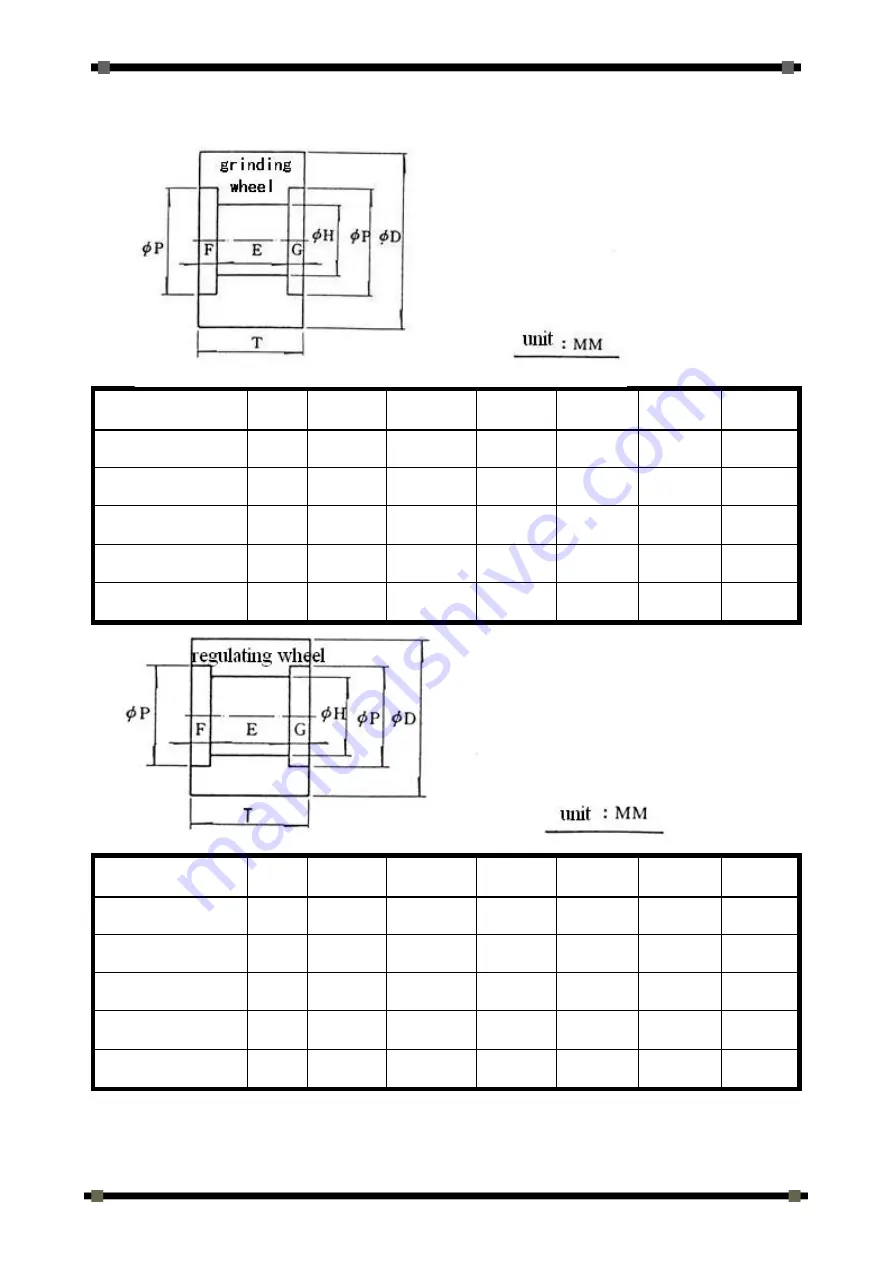
9 GRINDING APPLICATION
9-23
9.8
Size List of Grinding Wheel and Regulating Wheel
ψ
D
T
ψ
H
F
G
P
E
JHC-12 series
305
150
120
25
25
175
100
JHC-18 series
455
205
228.6
25
25
295
155
JHC-18A series 455
255
228.6
50
50
295
155
JHC-18B series 455
305
228.6
50
50
295
205
JHC-20 series
510
205
254
25
25
320
155
ψ
D
T
ψ
H
F
G
P
E
JHC-12 series
205
150
90
25
25
130
100
JHC-18 series
255
205
111.2
75
20
170
110
JHC-18A series 255
255
111.2
100
45
170
110
JHC-18B series 255
305
111.2
100
65
170
140
JHC-20 series
305
205
127
75
20
190
110
Property
of
Kent
Industrial
USA
Do
Not
Reproduce