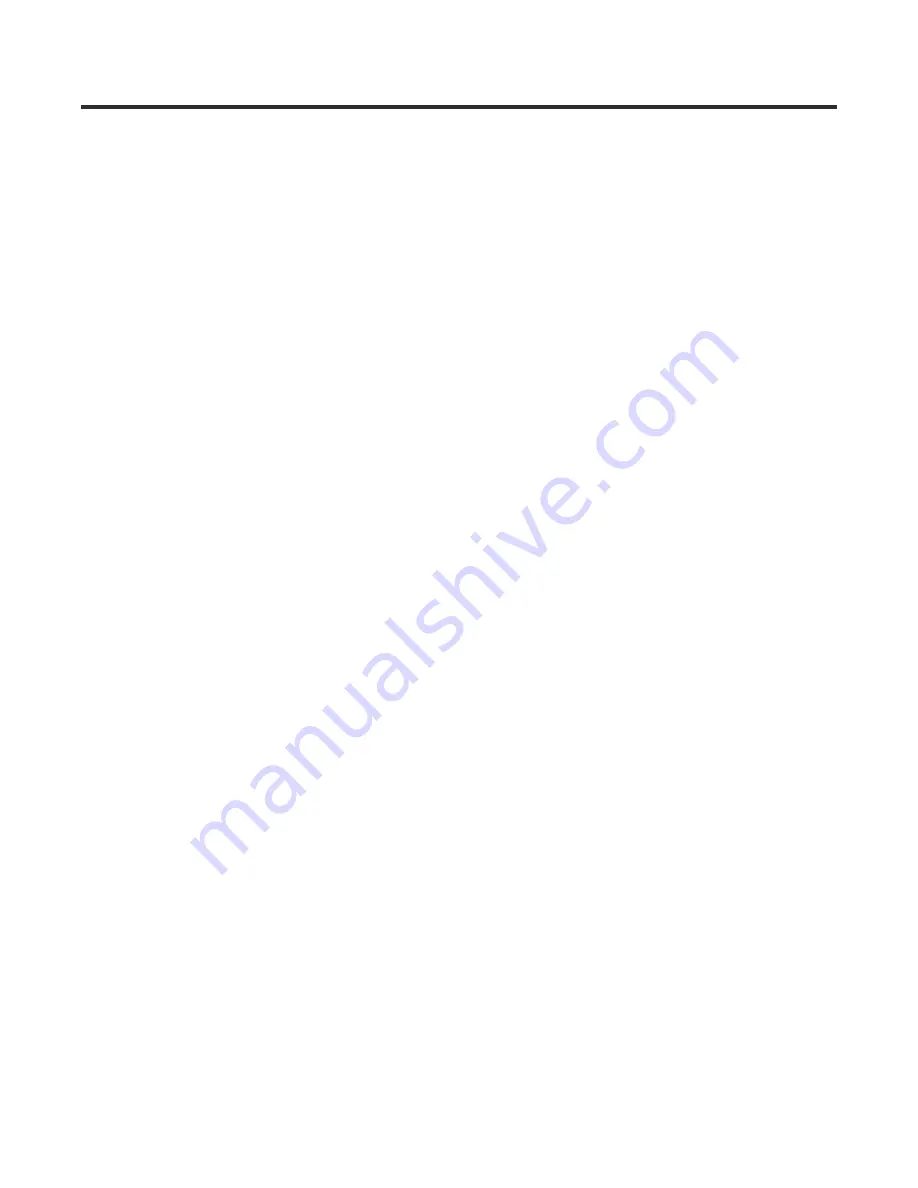
1. SPECIFICATIONS
1-1. DISCONNECT POWER CORD BEFORE SERVICING
IMPORTANT: Reconnect all grounding devices.
1-2. IMPORTANT NOTICE
1-3 ELECTRICAL SPECIFICATIONS
All parts of this appliance capable of conducting electrical current are grounded. If grounding wires, screws, straps, clips, nuts or
washers used to complete a path to ground are removed for service, they must be returned to their original position and properly
fastened.
This information is intended for use by individuals possessing adequate background of electrical, electronic and mechanical
experience.
Any attempt to repair a major appliance may result in personal injury and property damage. The manufacturer or seller cannot be
responsible for the interpretation of this information, nor can it assume any liability in connection with its use.
Freezer temperature control (Middle setting) ................................................................................................................ -6°F to +8°F
Defrost Control
Defrost Thermostat
Electrical Rating: 115VAC, 60Hz
Maximum Current Leakage
Maximum Ground Path Resistance
Energy Consumption
............................................................................................................................................................... Automatic
......................................................................................................................................................... 41°F (5°C)
............................................................................................................................................ 1 - 7 A
................................................................................................................................................... 0.5mA
.................................................................................................................................. 0.1Ohms
.................................................................................................................................... 26.09cu.ft. 715kWh/yr
And ambient of: ............................................................................ 70°F ................................................................................... 90°F
Fresh Food, °F ................................................................. 33°F to 41°F ....................................................................... 33°F to 41°F
Frozen Food, °F ................................................................ -4°F to +4°F ........................................................................ -4°F to+ 4°F
Percent Running Time ....................................................... 40% ~ 70% ......................................................................... 60% ~ 80%
1-4. NO LOAD PERFORMANCE
Control Position: MID/MID
1-5 REFRIGERATION SYSTEM
Minimum Compressor Capacity Vacuum .................................... 21 in
Minimum Equalized Pressure
@70°F .................................................................... 49 PSIG
@90°F .................................................................... 56 PSIG
Refrigerant R134a .................................................................. 6.17 oz
Compressor ...................................................................... 904BTU/hr
1-6 INSTALLATION
For proper air circulation, best cooling and energy
consumption results, maintain a minimum distance of 2
inches (5.08cm) from adjacent items and surfaces.
CLEARANCE
At Top............................................................................. 2 in
At Sides.......................................................................... 2 in
At Rear........................................................................... 2 in
4