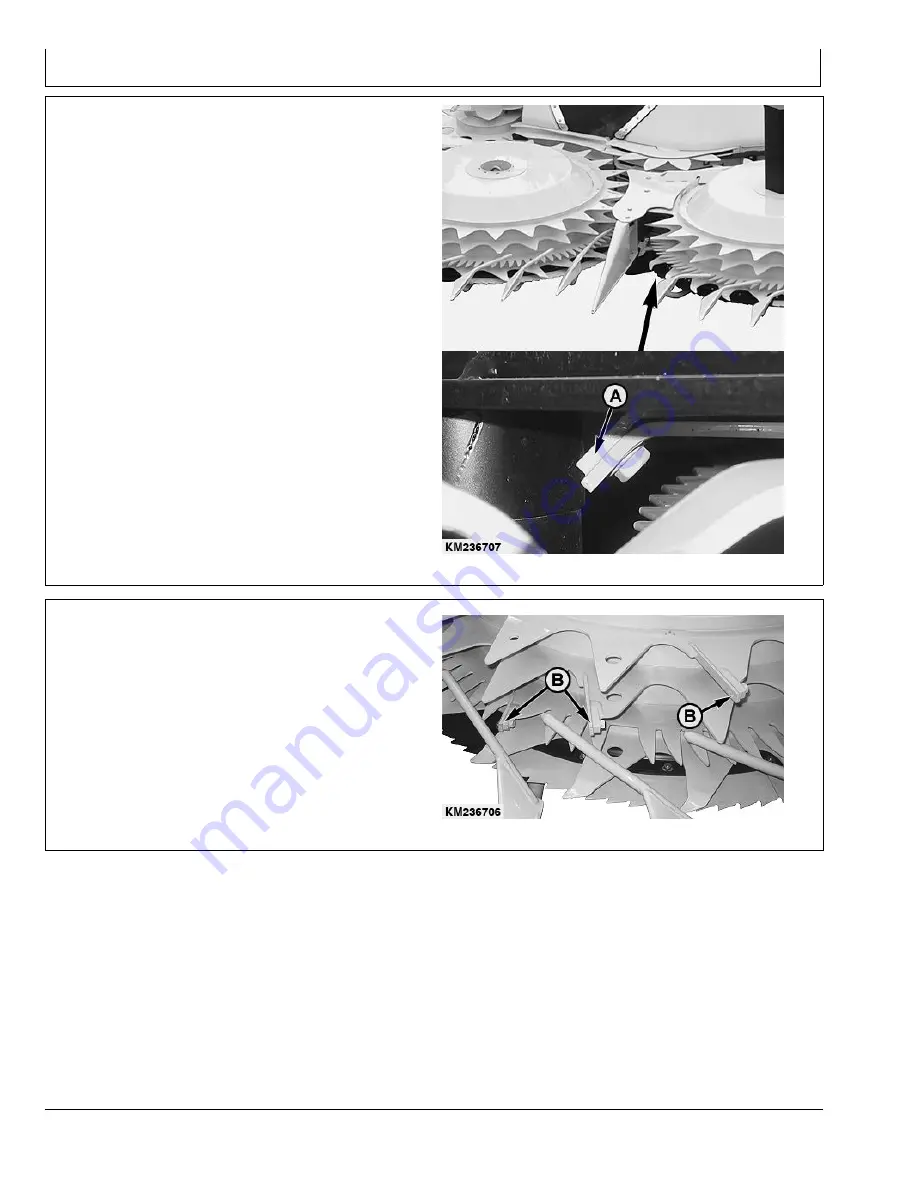
Service
KM00321,00003EB -19-16MAR15-1/2
KM00321,00003EB -19-16MAR15-2/2
Check Condition of Cleaners
Check condition of the cleaners (A) frequently. Replace
worn parts.
Damaged cleaners unnecessarily burden the drive and
may cause malfunction of the rotary harvesting unit.
A—Cleaner
KM236707
—UN—24FEB15
Check condition of the cleaners (B) frequently. Replace
worn parts.
B—Cleaners
KM236706
—UN—24FEB15
55-7
120519
PN=72