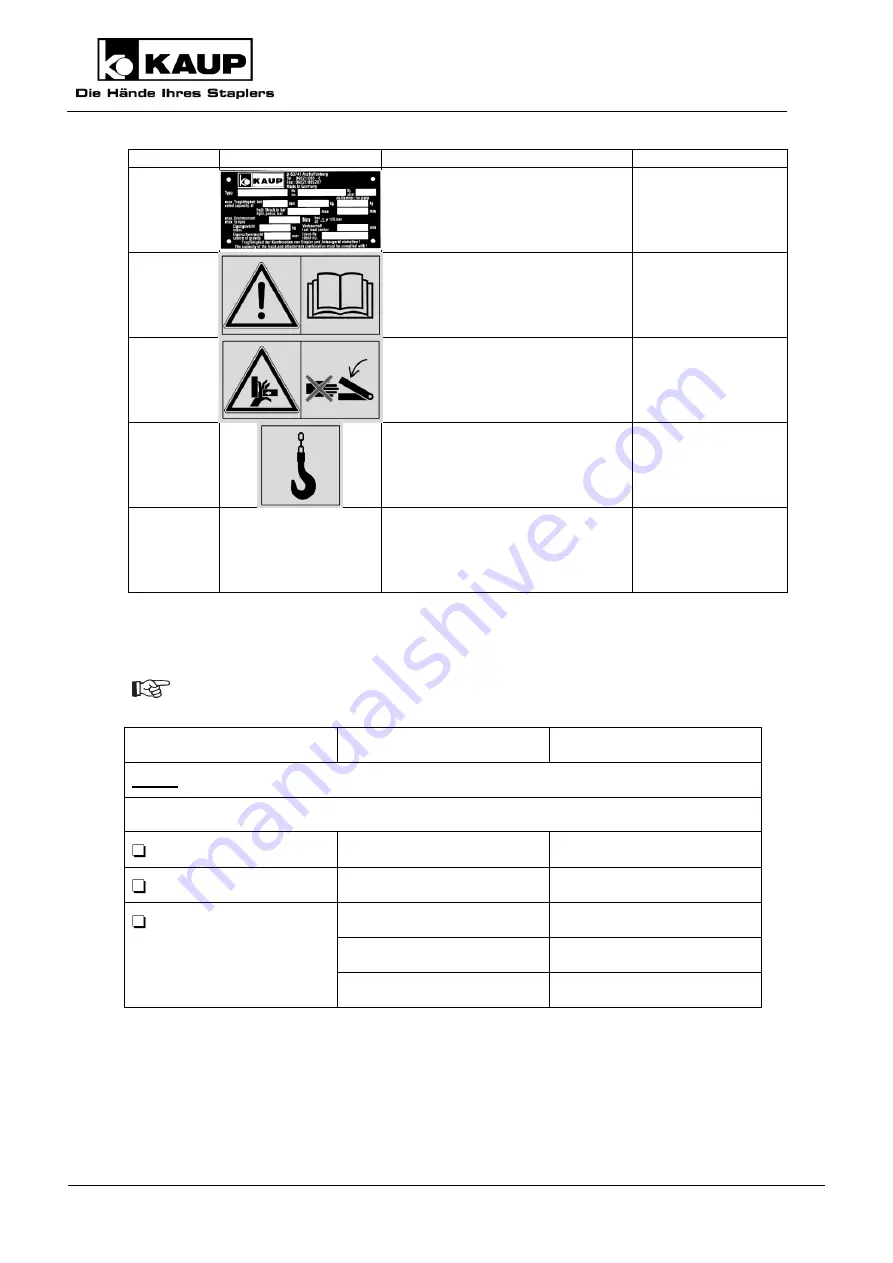
Operating Manual
22
Original Operating Manual
Number
Description
KAUP order number
1
Identification plate without
CE-Mark
only by Quality
department
2
Before putting into operation
carefully read and take note of the
operating and security instructions.
0100016401
3
Never reach into the unit as long
as parts could still be moving due
to the danger of squashing or
shearing.
0100016601
4
Use suspension point!
0100015001
5
ko xxxxxx
KAUP
– order number
without, engraved in
the material
7.
Troubleshooting
Troubleshooting should only be performed by qualified and authorised personnel.
Fault
Possible cause
Correction
Clamp
Opening and closing
No synchronism
WE throttles on the cylinder
unequally adjusted
Adjust the WE throttles on
the cylinder
Movement too slow
Insufficient fluid flow from
truck's hydraulics
Increase flow rate of truck's
hydraulics
Load not holding
Pressure too low
Increase the pressure from
the lift truck
Pressure too low on pressure
relief valve
Increase pressure on the
pressure relief valve
Cylinders have internal leaks
Replace sealing kits