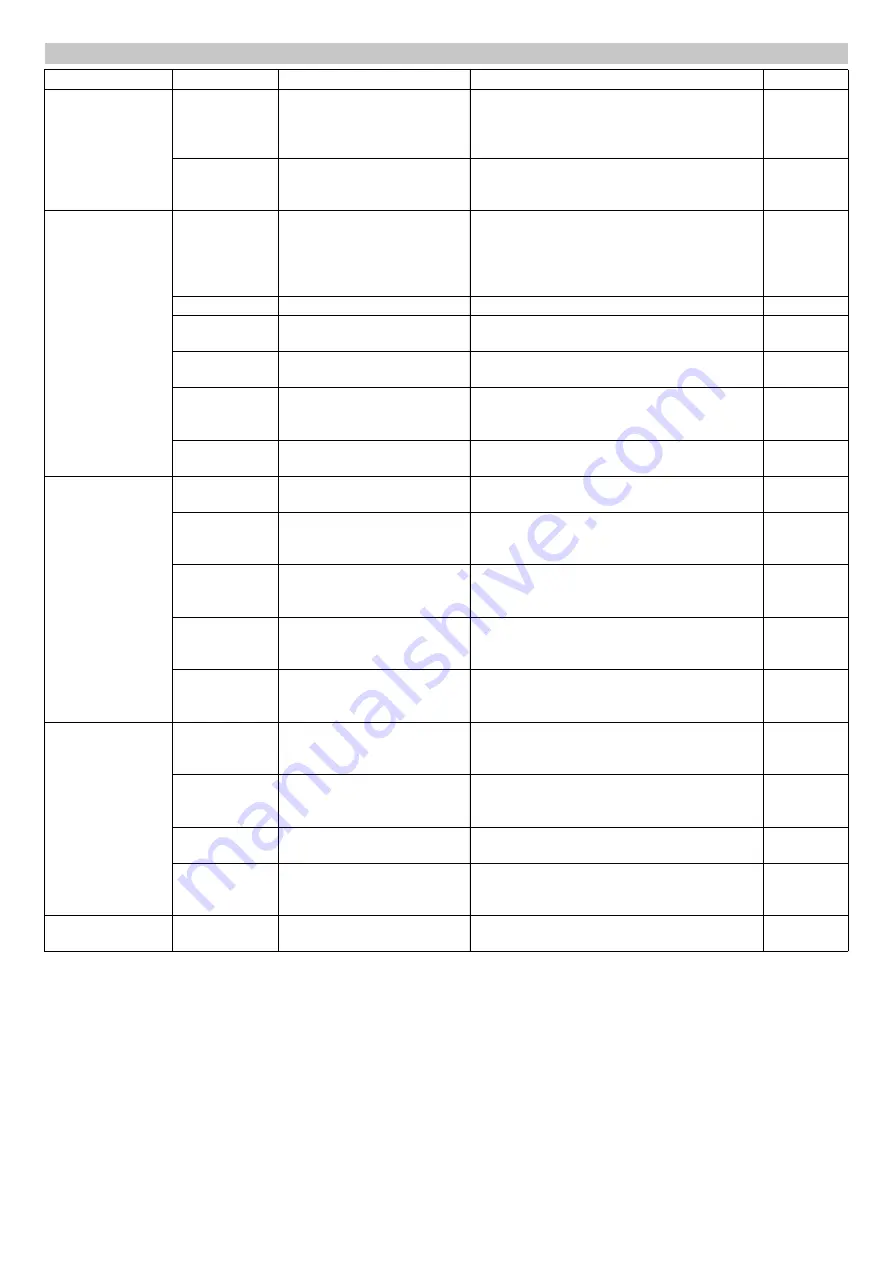
-
8
Maintenance schedule
Time
Activity
Assembly affected
Performance
of whom
daily
Check hand-
spray gun
Hand spray gun
Check whether the hand-spray gun closes tightly
without any leaks. Check the protection mecha-
nism against accidental switching. Replace de-
fective hand-spray guns.
Operator
Check high pres-
sure hoses
Outlets, hoses towards working
machine
Check hoses to see if there are damages. Re-
place defect hoses immediately. Danger of acci-
dent!
Operator
weekly or after 40
operating hours
Check the unit for
leaks
Entire plant
Check pumps, overflow valve and pipe system for
leaks. Inform Customer Service if there is oil be-
low the pump or if there is a leakage of more than
3 drops of water per minute. Keep the leakage
borings clear.
Operator/
Customer
Service
Check oil level
Oil level indicator on the pump If the oil is milky, it needs to be replaced.
Operator
Check oil level
Oil level indicator on the pump Check oil level of the pump. Refill oil if required
(Order no. 6.288-016)
Operator
Check working
pressure
Manometer
If the pressure is too high or too low, find the
cause and resolve it (see Help with Faults).
Operator
Check pressure
tank
High-pressure pump
A defective accumulator can be detected by an
increased vibration of the high pressure pump.
Replace defective accumulator.
Operator/
Customer
Service
Cleaning the
sieve
Dirt catcher
See section "Clean sieve".
Operator
monthly or after 200
operating hours
Check pump
High-pressure pump
Check the pump for leaks. If the leakage is more
than 3 drops per minute, call Customer Service.
Operator
Check water
scarcity fuse
Swimmer switch in the swimmer
tank
Press the swimmer of the low water fuse down for
about 5 seconds and control the error indicator on
the control board. Remove deposits if necessary.
Operator
Check the pres-
sure relief valve
Electro-pneumatic ball valve
combination for star delta start-
up
If it functions properly, the motor must reach full
throttle within 2 seconds. Remove deposits in the
valve if necessary.
Operator/
Customer
Service
Test swimmer
valve
Float tank
The water level must be 40 mm above the over-
flow. No water must exit while the swimmer valve
is closed.
Operator
Tighten hose
clips
All hose clips
Tighten the hose clips using a torque wrench.
Tightening torque up to a diameter of 28 mm =
2Nm, from 29 mm = 6 Nm.
Operator
half-yearly or after
1000 operating
hours
Oil change
High-pressure pump
Drain off oil. Fill in 1 l of fresh oil (order no. 6.288-
016.0). Check the oil level at the oil level indica-
tor.
Operator
Check the appli-
ance for calcium
deposits
entire water system
Improper functioning of valves or pumps can be
an indication of calcium deposits. If necessary
decalcify.
Operator
trained in de-
calcification
Tighten clamps Control board
Tighten all clamps for components in the main cir-
cuit.
Electricians
Test swimmer
valve
Float tank
The water level must be 40 mm above the over-
flow. No water must exit while the swimmer valve
is closed.
Customer
Service
annual
Safety check
Entire plant
Safety check according to the guidelines for fluid
spraying equipment.
Technical ex-
pert
24
EN
Summary of Contents for HDI 38/12
Page 2: ...2...
Page 159: ...3 60 C 0 3 0 6 bar 80 C 1 2 1 1 2 2 1 2 159 EL...
Page 161: ...5 34 35 36 37 A B A B 30 cm K rcher 0 A B A B 161 EL...
Page 163: ...7 A 1 1 2 B M30x1 5 C D Kaercher 1150 480 550 140 70 650 A B 100 D C 163 EL...
Page 164: ...8 40 3 6 288 016 200 3 5 2 40 mm 28 mm 2 Nm 29 mm 6 Nm 1000 1 6 288 016 0 40 mm 164 EL...
Page 165: ...9 K rcher 1 RM 100 6 287 008 RM 101 6 287 013 RM 100 pH 7 8 7 165 EL...
Page 166: ...10 Kaercher HWE 4000 166 EL...
Page 170: ...14 170 EL...
Page 187: ...3 60 C 0 3 0 6 80 C 1 1 1 2 2 1 2 187 RU...
Page 189: ...5 30 1 31 32 33 34 35 36 37 A B A B 30 Karcher A B A B 189 RU...
Page 191: ...7 A 1 1 2 B M30x1 5 C D K rcher 1150 480 550 140 70 650 A B 100 D C 191 RU...
Page 192: ...8 40 3 6 288 016 200 3 5 2 40 28 2 29 6 1000 1 6 288 016 0 40 192 RU...
Page 193: ...9 Karcher 1 RM 100 6 287 008 RM 101 6 287 013 RM 100 pH 7 8 7 193 RU...
Page 194: ...10 K rcher HWE 4000 194 RU...
Page 198: ...14 198 RU...
Page 313: ...3 60 C 0 3 0 6 bar 80 C 1 1 2 2 P1 P2 313 BG...
Page 315: ...5 30 1 31 32 33 34 35 36 37 A B A B 30 cm K rcher 0 A B A B 315 BG...
Page 317: ...7 A 1 1 2 B M30x1 5 C D Karcher 1150 480 550 140 70 650 A B 100 D C 317 BG...
Page 318: ...8 40 3 6 288 016 200 3 5 2 40 mm 28 2 Nm 29 6 Nm 1000 1 6 288 016 0 40 mm 318 BG...
Page 319: ...9 K rcher 1 RM 100 6 287 008 RM 101 6 287 013 100 pH 7 8 7 319 BG...
Page 320: ...10 Karcher HWE 4000 320 BG...
Page 324: ...14 324 BG...
Page 369: ...3 60 C 0 3 0 6 80 C 1 1 2 2 P1 P2 369 UK...
Page 371: ...5 31 32 33 34 35 36 37 A B A B 30 K rcher 0 A B A B 371 UK...
Page 373: ...7 A 1 1 2 B M30x1 5 C D K rcher 1150 480 550 140 70 650 A B 100 D C 373 UK...
Page 374: ...8 40 3 6 288 016 200 3 5 40 28 2 29 6 1000 1 6 288 016 0 40 374 UK...
Page 375: ...9 K rcher 1 RM 100 6 287 008 RM 101 6 287 013 RM 100 pH 7 8 7 375 UK...
Page 376: ...10 K rcher HWE 4000 376 UK...
Page 380: ...14 380 UK...
Page 381: ......
Page 382: ......
Page 383: ......
Page 384: ...http www kaercher com dealersearch...