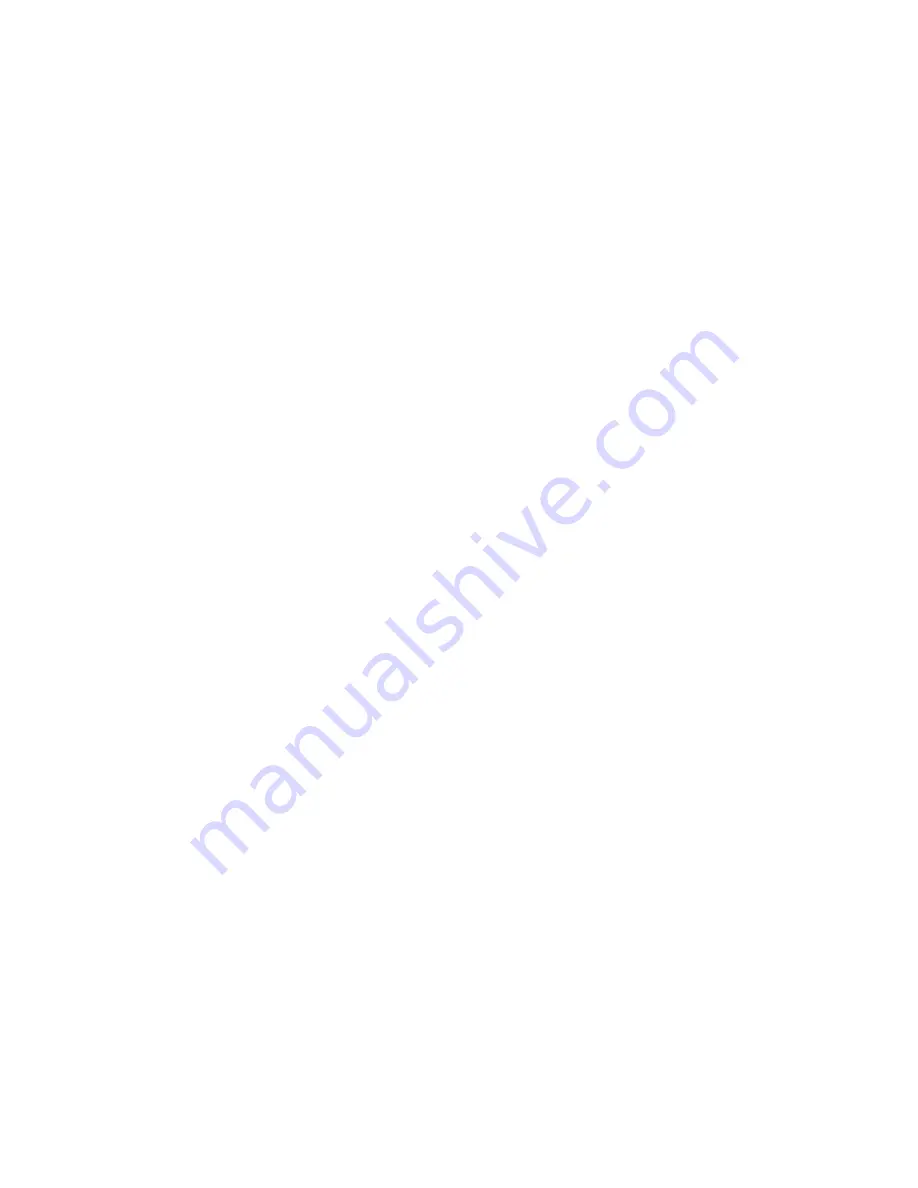
CAN RANGER III INSTALLATION
15
Center feature can be Enabled
or Disabled for that actuator.
This feature is generally
enabled if the valve spring is
weak.
ACTUATOR 1 CALIBRATION
If this is the first time
calibrating the actuators, start
with ACTUATOR 1 SETUP and
the controller will walk you
through all Enabled actuators
in turn (normally 4). Once you
have selected the actuator
you want to calibrate push
<SET> and follow the
instructions on the screen.
There are several settings for
each actuator. See the Option
Setup section. If you are
setting up a new actuator,
make sure to configure each
setting to match your
machine.
In each setting screen both
the stored value and the
current actuator position are
shown on the display.
Push <SET> to store the
current position into this
parameter or press
→
arrow
button to keep stored value.
The receiver will automatically
move to the next setting.
For example, if you selected
ACTUATOR 1, the first screen
will be for the center position.
Before pressing <SET>, move
the ACTUATOR 1 Handle back
and forth. The displayed
position, shown in inch,
should change. If not, the
wrong actuator is connected
to this connection, or the