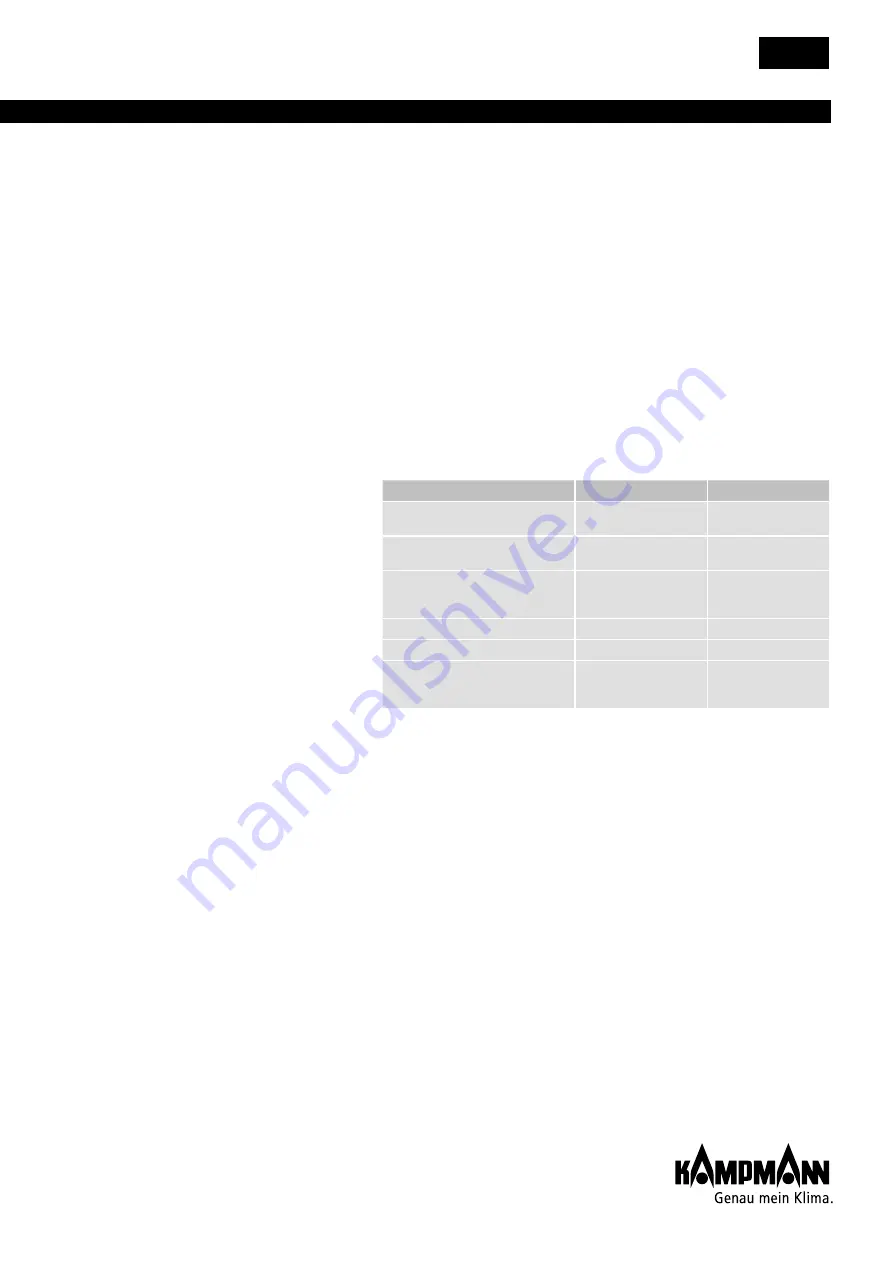
27
KaDeck
3.26
Versatile air conditioning for offices and administration buildings
Installation and operating instructions
6.4 Wet and dry cooling model
Distinction
A distinction is made between two basic models of KaDeck –
dry and wet cooling.
Never connect dry cooling units to an on-site water system in
which the temperature could fall below the dew point!
KaDeck dry cooling models configured for KaControl can be
fitted with a factory-fitted dewpoint monitor, which monitors
the heat exchanger. If the temperature falls below the dew
point on the heat exchanger, the dew point monitor switches
off the cooling valve.
The dew point monitor does not act as a controller and even if
a dew point sensor is used, the on-site water network has to be
operated above the dew point!
The following table provides an
overview of the equipment on the
KaDeck units depending on the
model.
KaDeck
Dry cooling
Wet cooling
Heat exchanger optimised for
dry cooling mode
yes
no
Heat exchanger optimised for
wet cooling mode
no
yes
Dewpoint monitor, factory-
fitted
optionally available
with KaControl
configuration
no
Condensation tray
no
yes
Condensation pump
no
yes
Housing vapour-tightly
insulated against condensation
no
yes
Summary of Contents for KaDeck
Page 95: ......