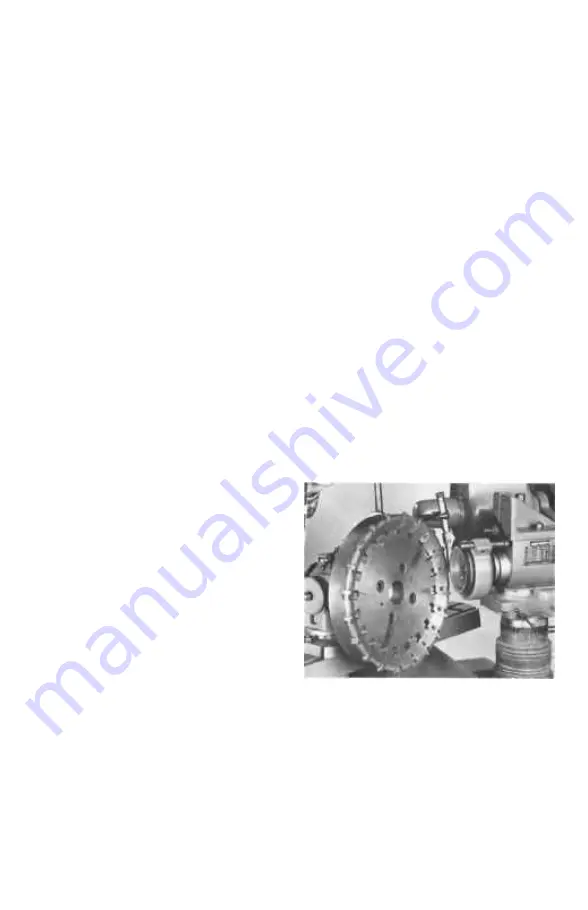
Instruction Manual
Section Five
2
Install the wheel guard in a position that will not contact the mill when
traversed for grinding and that allows visual observation.
3. When the toothrest is fixed on the column as in part B-3 above, traverse
the table in the same manner as in C-1. The cutter blade is passed over
it to the left for right) up to a fixed stop which keeps the cutter on
the toothrest, but past the wheel edge.
4 Advance the Crossfeed of the machine to a point where one of the blades
about
1
/
16
inch from the wheel edge and start the grinding wheel, being
certain that the wheel periphery is rotating in a direction that will drive
the cutter blade against the toothrest
5. Standing at the front of the machine (OR SIDE, IF THE MACHINE HAS
BACK OPERATED CONTROLS) and holding the cutter face against the
toothrest, continue to move the Crossfeed in slowly until the wheel has
just contacted the blade at some point on its clearance. Begin to tra
verse the table slowly to the left (or right) until the stop is reached;
then return until the blade has passed to the right of the wheel edge.
Rotate the mill so as to bring a new blade into contact with the tooth
rest (IN PHOTO 32. THIS IS COUNTERCLOCKWISE FACING THE
REAR OF THE CUTTER FROM THE MACHINE FRONT). Use a red
marking pencil and mark the tooth just ground. Continue the above opera
tion for each inserted blade When the red-marked tooth appears again
on the toothrest, examine all blades to see if the wheel has contacted all
of them equally. Advance the Crossfeed no more than .001 inch and pro
ceed to sharpen all the blades again, repeating process until the cutting
edges appear to be sharp. No light will reflect from a sharp edge.
II.
SHARPENING THE CHAMFER
(SEE PHOTO 36)
A. Set-up preparation assumes steps I,
1 and 2 are completed. Without
moving the face mill in the workhead
or the workhead relative to the table
and without changing the clearance
angle setting for the blade cutter
faces, swivel the upper table to the
desired chamfer angle (60 DECREES
IN THIS INSTANCE) relative to the
subtable. Tighten the center friction
lock screw on the swivel table.
B. Toothrest and Clearance Angle Setting;
1.
Non-tilthead grinders:
Re-adjust the toothrest so that the micrometer can
be used to obtain final clearance adjustments if desired. In most cases,
chamfer clearances can be producer by merely matching visually the exist
ing clearances with the vertical surface of the wheel edge. The clear
ance angle setting for the cutter faces will approximate this chamfer
clearance angle when new blades are being ground, by simply grinding at
the desired chamfer angle until the chamfer clearance surface meets the
cutter face and periphery clearance surfaces. If exact corner clearances
are necessary, see Table V, page 107.
PHOTO 36
--
46
--