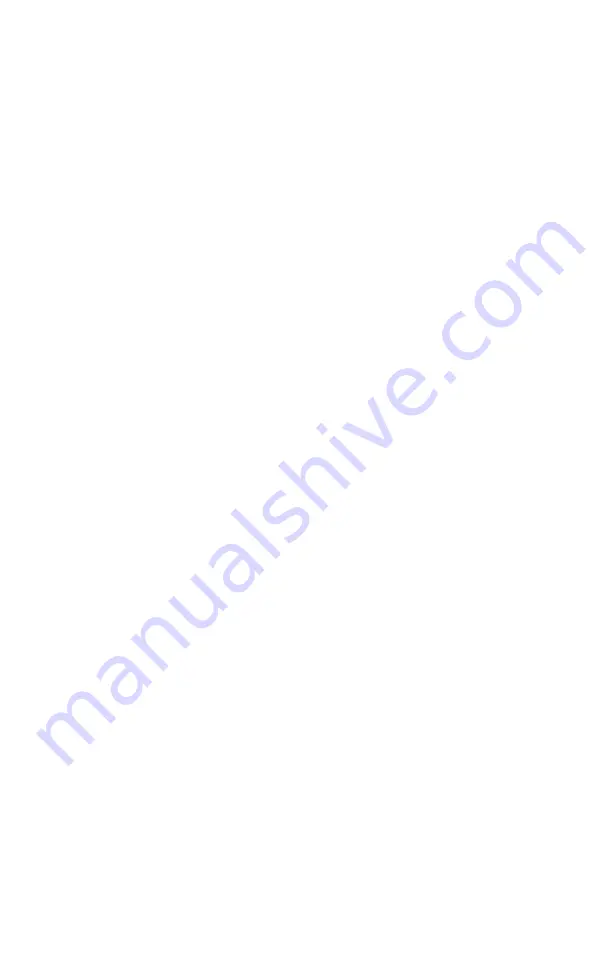
Instruction Manual
Section Five
cylindrically to the exact size desired, and then "back off" the teeth so
as to leave practically a sharp cutting edge, the land being no more than
a few thousandths of an inch wide. A few light strokes along the cutting
edges (FACES) with an oilstone will remove any slight burr produced in
grinding.
If the reamer is provided with a front pilot and is ground between centers,
the center supporting the expansion plug end should be adjustable so that
the pilot surface can be centered with an indicator before grinding.
Hand reamers are always ground with a taper or lead at the front portion
of the blades to allow it to enter the hole freely and without chattering
The amount of lead depends on the amount of material to be removed and
is generally about
1
/
16
inch per foot (OBTAINED BY ADJUSTING THE
SWIVEL TABLE OF THE GRINDING MACHINE) and approximately
½
inch in length for reamers up to 2 inches in diameter, and
¾
inch in length
for larger sizes.
10.
TAPER REAMERS
(SEE PAGE 67 FOR ILLUSTRATION AND DESCRIP
TION OF A SPECIFIC SET-UP.)
Taper reamers must be ground with great care in order to maintain the
correct taper and the diameter. The toothrest is fastened to the wheel-
head and the finger is adjusted to support the tooth being ground. The
swivel table is adjusted to the required taper per foot, as indicated on the
graduated scale at the end of the grinder table.
The relief angle will depend on the material to be cut and the size of the
reamer. Tables for relief of reamers are given in Section Seven of the
manual and should be taken as only approximations for most reamers. On
the tilting Wheelhead cutter grinder, the relief setting is made by simply
tipping the Wheelhead to the angle desired. Trial cuts should be taken
with a sharpened taper reamer, and the reamer hole tested for truth with
a standard plug before using the reamer.
In some tool rooms, taper reamers are sharpened by grinding cylindrically
and then "backing off" the teeth, leaving a land a few thousandths of an
inch wide, as in grinding straight reamers. This method insures uniform
tooth height, which is important if the reamer is to cut without chattering
and leave a smooth finish.
B. The second general group consists of cutters which are sharpened by grinding
the front, radial cutting faces of the teeth so as not to alter their profile. This
group includes formed cutters. Fellows, and Involute gear cutters, hobs, and
forming tools.
I.
FORMED CUTTERS
(SEE PAGE 48 FOR ILLUSTRATION AND DESCRIP
TION OF A SPECIFIC SET-UP )
Formed cutters are ground radially on the cutting face with a saucer wheel.
Various methods are employed for controlling the spacing of the teeth.
For most set-ups, the cutter is revolved until the face of a tooth just touches
the cutting face of the grinding wheel. Previously, the wheel face and the
center of the radial tooth cutter must have been brought into the same ver
tical plane. The toothrest is then adjusted against the back of the tooth
to be ground.
Some form cutters are made with a forward rake or undercut tooth. In
sharpening these, care must be taken to offset the wheel face so as to
maintain the original rake angle. The amount of this offset, measured on
-30—