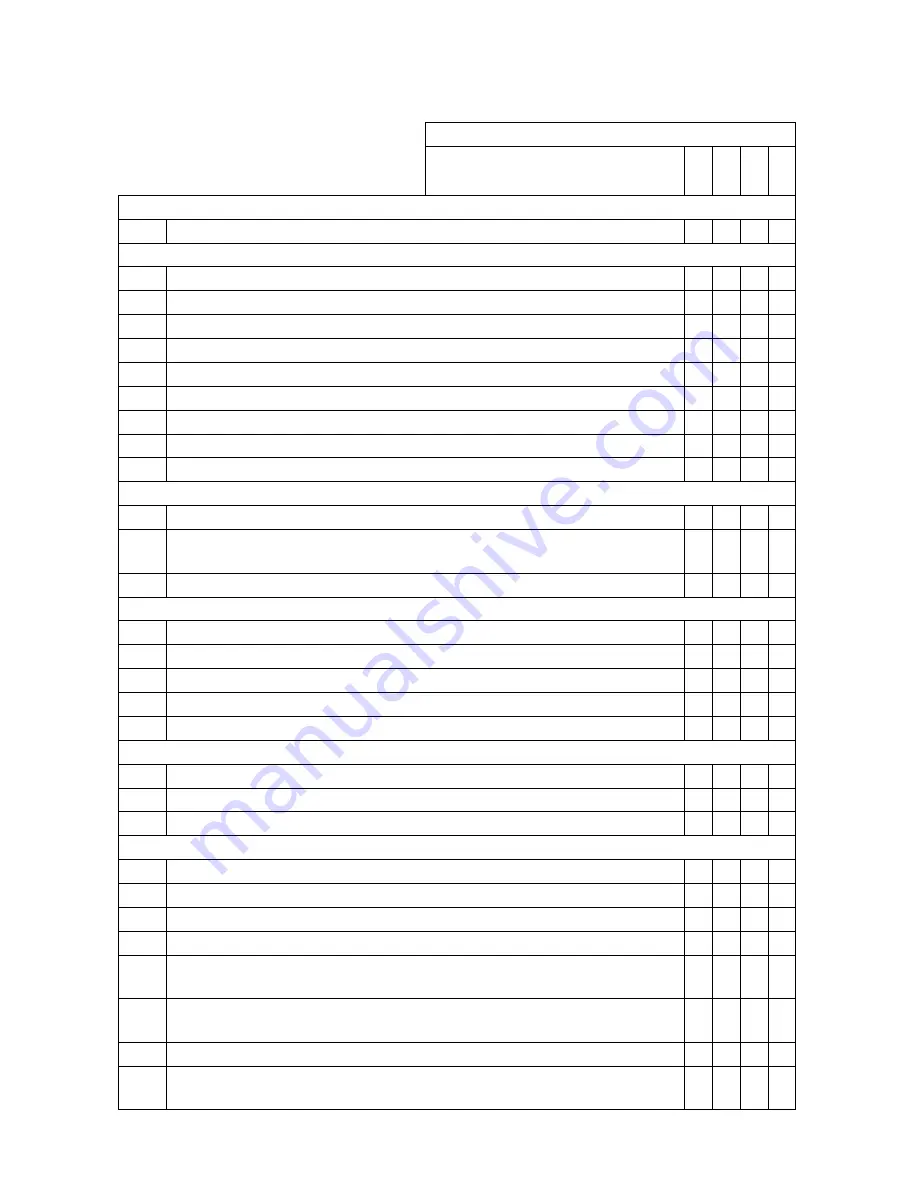
03
.0
9 EN
84
4
Maintenance checklist
Maintenance Intervals
Standard =
t
Cold store =
k
W A B C
Braking
1.1 Check magnetic brake air gap
t
Electrical system
2.1 Test instruments, displays and control switches.
t
2.2 Test warning and safety devices
k
t
2.3 Check fuse ratings.
t
2.4 Make sure wire connections are secure and check for damage.
t
2.5 Test micro switch settings
t
2.6 Check contactors and relays
t
2.7 Safety switch
t
2.8 Test cable and motor attachments
t
2.9 Check carbon brush wear, replace if necessary
k
t
Power supply
3.1 Visually inspect battery
k
t
3.2
Check battery cable connections are secure, grease terminals if nec-
essary
k
t
3.3 Check acid density, acid level and battery voltage
k
t
Travel
4.1 Check the transmission for noise and leakage
t
4.2 Replace gear oil if service life exceeded (10000 hours)
4.3 Check rail guide roller bedding and attachment
t
4.4 Check wheels (load wheels / drive wheel) for wear and damage
k
t
4.5 Check wheel suspension and attachment.
t
Chassis and superstructure
5.1 Test the operator platform and check for damage
t
5.2 Check chassis and screw connections for damage
t
5.3 Check labels
t
Hydraulic operation
6.1 Visually inspect rollers, slide pieces and stops.
t
6.2 Check operation, wear and setting.
t
6.3 Test hydraulic system.
k
t
6.4 Check the hydraulic auxiliary unit (not on EKS 110 LG).
t
6.5
Check that hose and pipe lines and their connections are secure,
check for leaks and damage.
k
t
6.6
Check cylinders and piston rods for damage and leaks, and make
sure they are secure.
k
t
6.7 Check hydraulic oil level.
k
t
6.8
Replace hydraulic oil. (This may have to be performed via a special-
ist environmental service truck)
k t
03
.0
9 EN
84
4
Maintenance checklist
Maintenance Intervals
Standard =
t
Cold store =
k
W A B C
Braking
1.1 Check magnetic brake air gap
t
Electrical system
2.1 Test instruments, displays and control switches.
t
2.2 Test warning and safety devices
k
t
2.3 Check fuse ratings.
t
2.4 Make sure wire connections are secure and check for damage.
t
2.5 Test micro switch settings
t
2.6 Check contactors and relays
t
2.7 Safety switch
t
2.8 Test cable and motor attachments
t
2.9 Check carbon brush wear, replace if necessary
k
t
Power supply
3.1 Visually inspect battery
k
t
3.2
Check battery cable connections are secure, grease terminals if nec-
essary
k
t
3.3 Check acid density, acid level and battery voltage
k
t
Travel
4.1 Check the transmission for noise and leakage
t
4.2 Replace gear oil if service life exceeded (10000 hours)
4.3 Check rail guide roller bedding and attachment
t
4.4 Check wheels (load wheels / drive wheel) for wear and damage
k
t
4.5 Check wheel suspension and attachment.
t
Chassis and superstructure
5.1 Test the operator platform and check for damage
t
5.2 Check chassis and screw connections for damage
t
5.3 Check labels
t
Hydraulic operation
6.1 Visually inspect rollers, slide pieces and stops.
t
6.2 Check operation, wear and setting.
t
6.3 Test hydraulic system.
k
t
6.4 Check the hydraulic auxiliary unit (not on EKS 110 LG).
t
6.5
Check that hose and pipe lines and their connections are secure,
check for leaks and damage.
k
t
6.6
Check cylinders and piston rods for damage and leaks, and make
sure they are secure.
k
t
6.7 Check hydraulic oil level.
k
t
6.8
Replace hydraulic oil. (This may have to be performed via a special-
ist environmental service truck)
k t
Summary of Contents for EKS 110
Page 1: ...03 09 03 09 51141993 EKS 110 Operating instructions G...
Page 7: ...03 09 DE 6...
Page 9: ...0506 GB 2...
Page 11: ...03 09 EN 8...
Page 33: ...03 09 EN 30...
Page 77: ...03 09 EN 74...
Page 121: ...0506 GB 18...