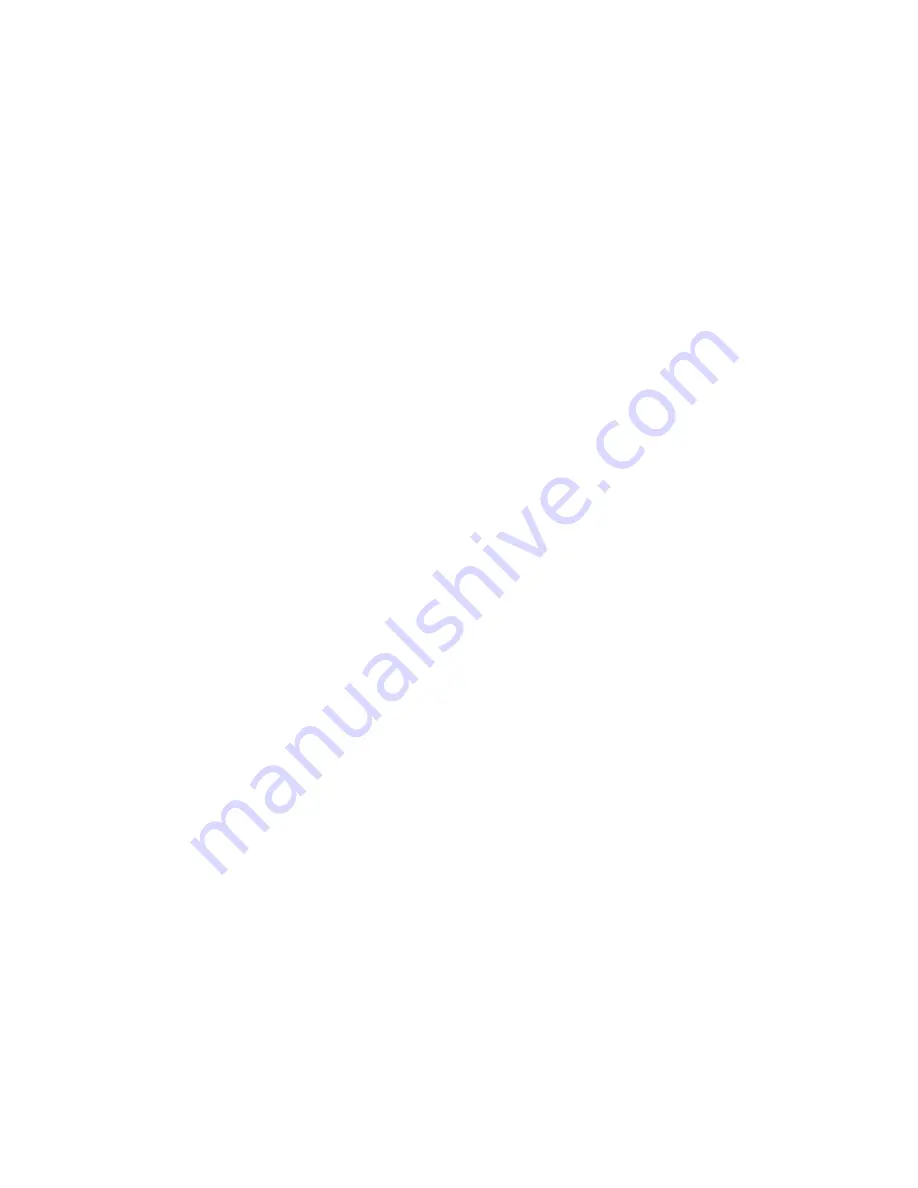
0506
.GB
12
10.2.1 Clamping ring tool
The clamping ring tool is used to push on a clamping ring to increase the contact pres-
sure of the hose connection on the plugs' hose couplings and to loosen it again.
10.3 Filter element
For safety reasons a filter element (ident no.: 50307282) can be fitted into the batte-
ry's main supply pipe for supplying battery water. This filter element has a maximum
passage cross-section of 100 to 300 µm and is designed as a bag filter.
10.4 Sealing coupler
The water is supplied to the water refilling systems (Aquamatic/BFS) through a cen-
tral supply pipe. This is connected to the water supply system at the battery charging
station by means of a sealing coupler system. On the battery side a closing nipple
(ident no.: 50219538) is mounted and the customer must place a sealing coupler
construction on the water supply side (obtainable under ident. no.: 50219537).
11. Functional data
PS - self-sealing pressure: Aquamatic > 1.2 bars
BFS system none
D - rate of flow in the opened valve when the pressure is 0.1 bars: 350 ml/min
D1 - maximum permissible leakage rate in the closed valve when the pressure is at
0.1 bars: 2 ml/min
T
- permissible temperature range: 0° C to a maximum of 65° C
Pa - operating pressure range: 0.2 to 0.6 bars in the Aquamatic system and
operating pressure range: 0.3 to 1.8 bars in the BFS system.
0506
.GB
12
10.2.1 Clamping ring tool
The clamping ring tool is used to push on a clamping ring to increase the contact pres-
sure of the hose connection on the plugs' hose couplings and to loosen it again.
10.3 Filter element
For safety reasons a filter element (ident no.: 50307282) can be fitted into the batte-
ry's main supply pipe for supplying battery water. This filter element has a maximum
passage cross-section of 100 to 300 µm and is designed as a bag filter.
10.4 Sealing coupler
The water is supplied to the water refilling systems (Aquamatic/BFS) through a cen-
tral supply pipe. This is connected to the water supply system at the battery charging
station by means of a sealing coupler system. On the battery side a closing nipple
(ident no.: 50219538) is mounted and the customer must place a sealing coupler
construction on the water supply side (obtainable under ident. no.: 50219537).
11. Functional data
PS - self-sealing pressure: Aquamatic > 1.2 bars
BFS system none
D - rate of flow in the opened valve when the pressure is 0.1 bars: 350 ml/min
D1 - maximum permissible leakage rate in the closed valve when the pressure is at
0.1 bars: 2 ml/min
T
- permissible temperature range: 0° C to a maximum of 65° C
Pa - operating pressure range: 0.2 to 0.6 bars in the Aquamatic system and
operating pressure range: 0.3 to 1.8 bars in the BFS system.
Summary of Contents for EKS 110
Page 1: ...03 09 03 09 51141993 EKS 110 Operating instructions G...
Page 7: ...03 09 DE 6...
Page 9: ...0506 GB 2...
Page 11: ...03 09 EN 8...
Page 33: ...03 09 EN 30...
Page 77: ...03 09 EN 74...
Page 121: ...0506 GB 18...