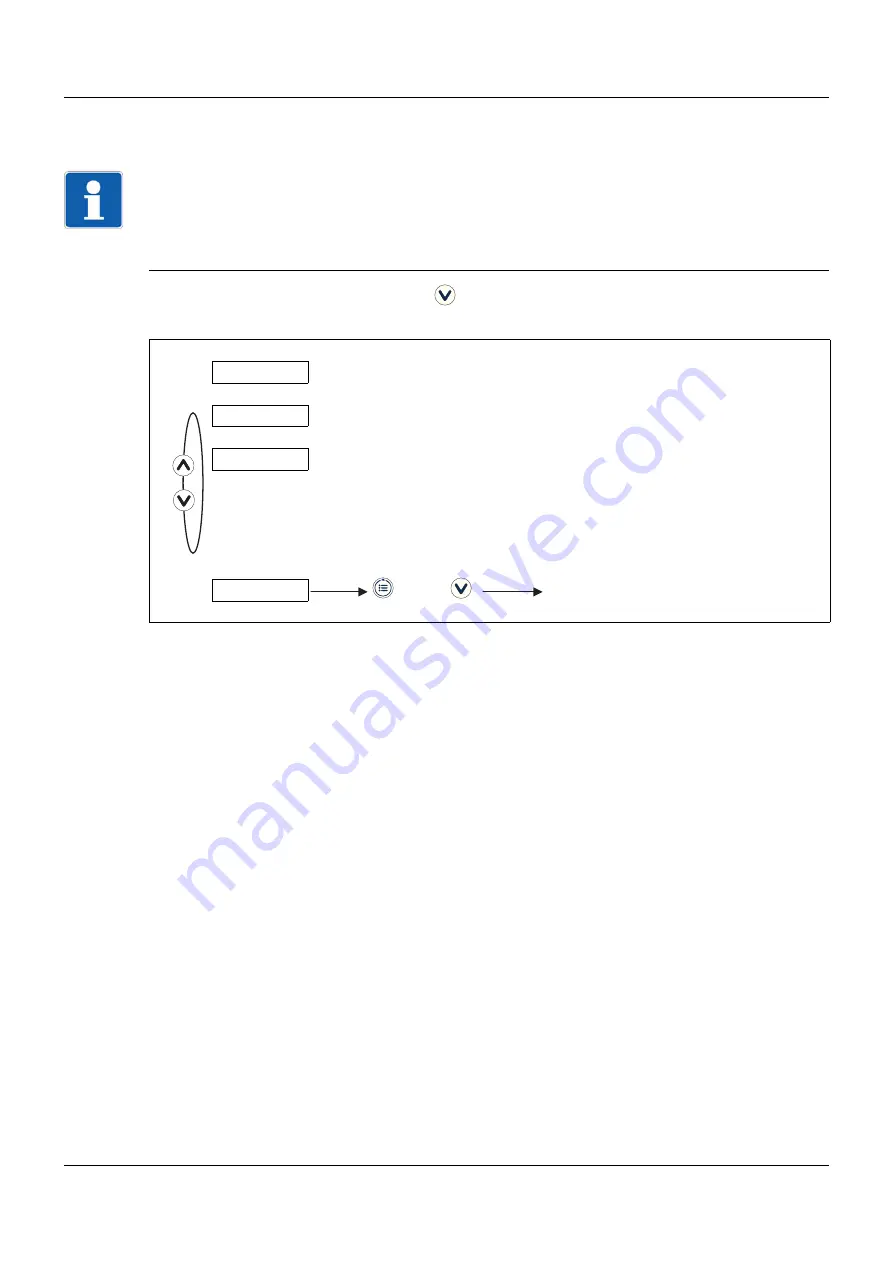
8 Startup and parameterization
72
8.8
Information menu details
To access the information menu, press the
key for longer than 2 seconds in the process level.
This menu can be used to read off warnings and error messages generated by the device.
NOTE!
This menu is only accessible when the device status LED is orange or red.
Meaning of a message
see chapter 9.5.4 "Solving a problem with a warning or error message with the
red device status LED", page 79 and chapter 9.5.5 "Solving a problem with a warning or error message
with the orange device status LED", page 80.
MESSAGE 1
MESSAGE 2
MESSAGE Z
.
.
.
END
a
or
a
When the CONFIRM key is unlocked
Process level