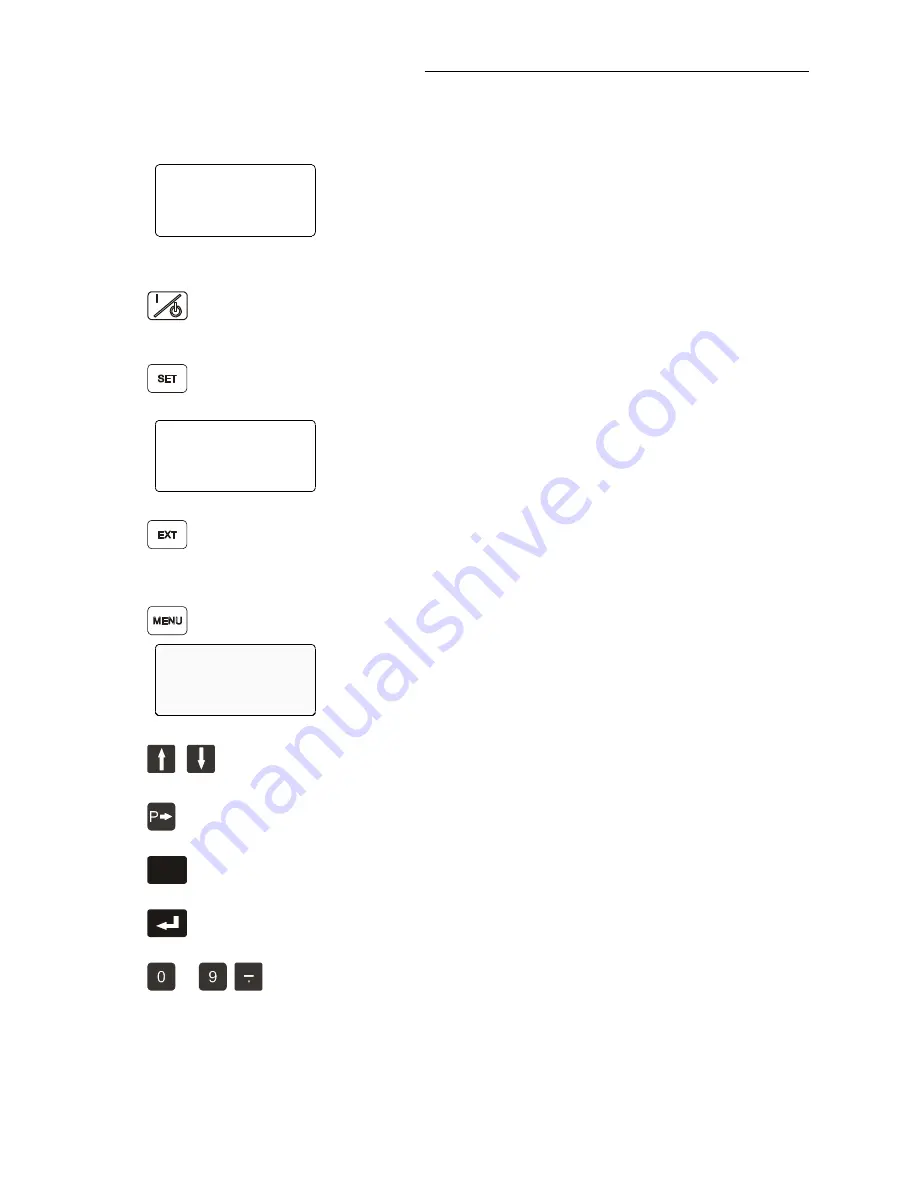
Temperature System Magnum 91
13
2
Operating board 1
2.0
Setp: 120.00°C
IntAct 21.00°C
ExtAct: 20.00°C
Control: Intern
DIALOG-DISPLAY (LCD)
Standard indication
Line 1:
Setpoint
in °C
Line 2:
Internal actual value
in °C
Line 3:
External actual value
in °C
Line 4:
Control type: internal / external control
Indicating messages (e. g. warnings)
2.1
Start / stop key
To switch the circulation pump, heating element and cooling unit.
2.2
>Setp.: 120.00°C
Overt.:255.00°C
Subtmp:-55.00°C
St.Pump: 2
SET Menu Key - Indicating and setting setpoint values
Set the following values:
in Line 1:
the working temperature
Setp.:
Line 2:
the high temperature limit
Overt.:
Line 3:
the low temperature limit
Subtmp:
Line 4:
the pump pressure stage
St.Pump:
2.3
Control type: internal / external control
To swap, the unit has to be in the STOP MODE.
Indicated in line 4 on the DIALOG-DISPLAY (LCD)
2.4
>Configuration
Control param.
Profile Start
Int. Programmer
MENU key - for selecting the menu functions
(Menu see page 36)
2.5
Cursor keys - Select menu items
2.6
P-key Selecting
parameters
2.7
ESC
Escape key
1) Cancel entries
2) Return to a higher menu level
2.8
Enter key
1) Store value / parameter
2) Next lower menu level
2.9
....
Numeric keypad: numerals 0 to 9; minus / decimal point