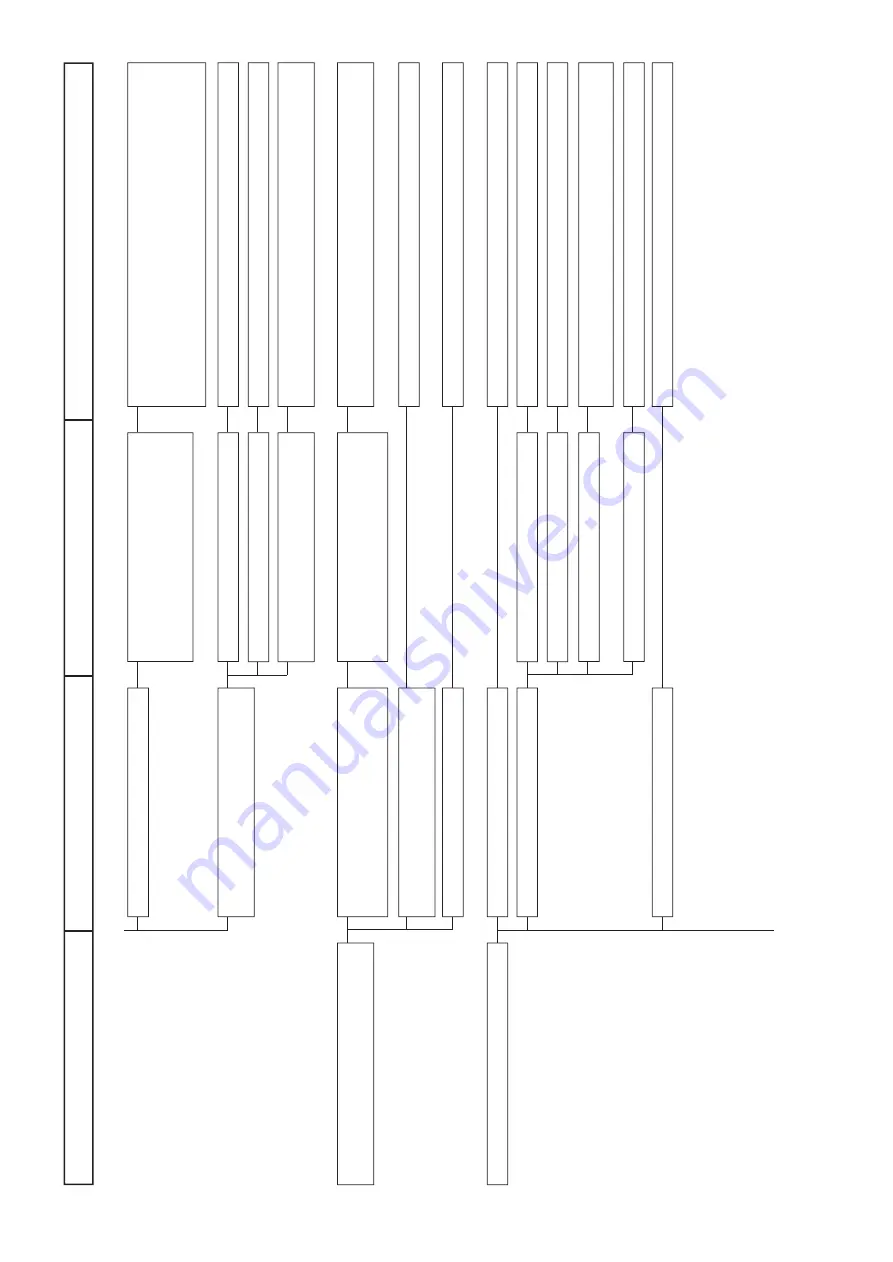
−
57
−
Troubles
Cause (1)
Cause (2)
Checking orders and corrective measures
From the previous page
Thread breaks when performing idle stitching
or jump stitching.
Uneven stitches
Hook timing is delayed.
Thread take-up spring is improperly
adjusted.
Same cause as [Thread breaks when
performing reverse feed stitching or back-
tack stitching]
Position of the knife thread guide is
improper.
Needle bar is positioned low.
Needle thread tension is too high.
Needle is defective.
Number of revolution is too high.
If the hook timing is delayed, needle thread
loop becomes too big and is deformed. As
a result, thread breakage occurs since the
blade point catches thread twice.
Stroke is too large or too small.
Tension is too high or too low.
Selection of the spring is improper for the
kind of thread.
Same cause as [Thread breaks when
performing reverse feed stitching or back-
tack stitching]
Needle is bent.
Top end of the needle is blunt.
Needle is too thin.
Needle is too long.
Adjust the hook in the state that the timing is earlier by 0.2 mm
than the lower marker line of needle bar.
Or, change the needle bar to needle bar of 22886907. Interval of
the marker lines of needle bar of 22886907 is narrower by o.2
mm than that of the standard.
Adjust the stroke.
Adjust the tension.
In case of A type thread tension, replace the spring with the
standard one. (In case of thick thread of #60 or more)
Same adjustment as [Thread breaks when performing reverse
feed stitching or back-tack stitching]
Adjust so that needle drops in the center of the hole.
Raise the needle bar.
Decrease the tension.
Replace the needle.
Replace the needle.
Use a thick needle. Use the double-step needle in case of KN
needle (one step needle).
Use a short needle. Or, use a needle with long shank. (DAX1)
Decrease the number of revolution.
To the next page
▼