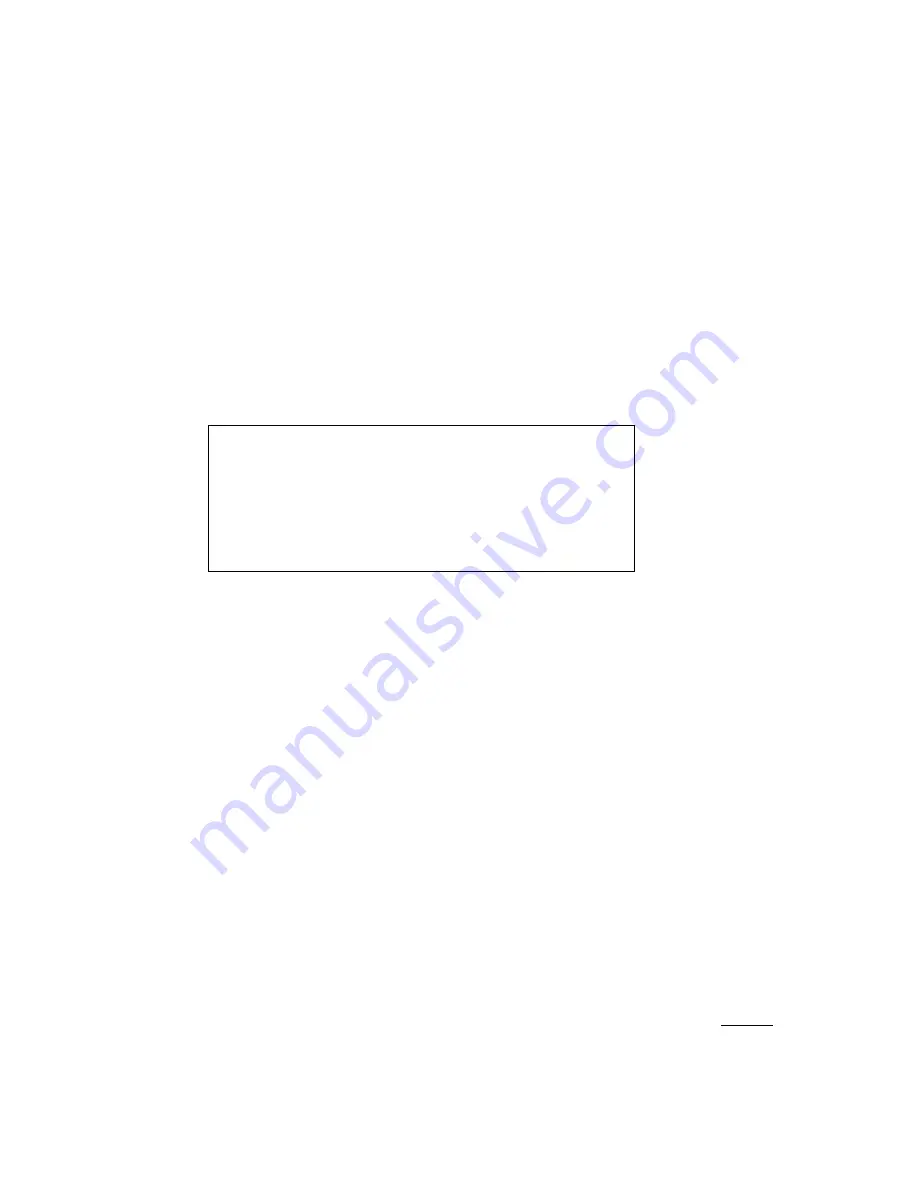
6
5. ELECTRICAL
INSTALLATION
5.1 INSTALLER
The electric service and connections to the GRD must be installed by a
licensed certified electrician.
5.2 POWER
HOOKUP
WARNING!
Do not apply power to the unit until the GI-2000 is completely
full of water. Install this unit as any GRD would normally be installed with
the exception to provide a 220/208VAC, single phase, Ground Fault
Circuit Interrupter (do not apply power to the unit at this point), 4 wire
connection hard wired to the main power box side of the GI-2000 per
code. The electrical installation must conform to NEMA-4 standards. The
main power wire cannot be run through a wall and must be wired to the
main breaker panel so that it can be viewed from the GI-2000 area.
Model
Voltage
Heating
Watts
GFI
Breaker
60306A 220/208 VAC 5000 Watts 25 AMP
60307A 220/208
VAC
7000 Watts 40 AMP
60308A 220/208
VAC
7000 Watts 40 AMP
60309A 220/208
VAC
7000 Watts 40 AMP
60310A 220/208
VAC
9000 Watts 50 AMP
For special order models not listed consult Josam Company for power
requirements.
5.3 NEMA-4
BOX
Red:
.
120VAC (L1)
Black:
.
120VAC (L2)
White:
.
Neutral
Green:
.
Ground
Wire
Type:
.
(Type MTW) 10 Awg min.
Conduit
Description:
.
1” Liquid-Tight Flexible Nonmetallic Conduit
Conduit Part #:
.
7581K44
WARNING!
System power should be secured into the power inlet box
(access via heater element port as shown in Diagram A) in a method that
conforms to NEMA-4 standards. Wire nuts are used to connect the power
wires behind the power conduit port.
5.4
INITIAL POWER TEST
After confirming that the unit is level, fill the GI-2000 with water before
applying power to the unit. Verify with a current probe that L1 and L2 are
below 1 amp. Once confirmed, remove power from the unit.