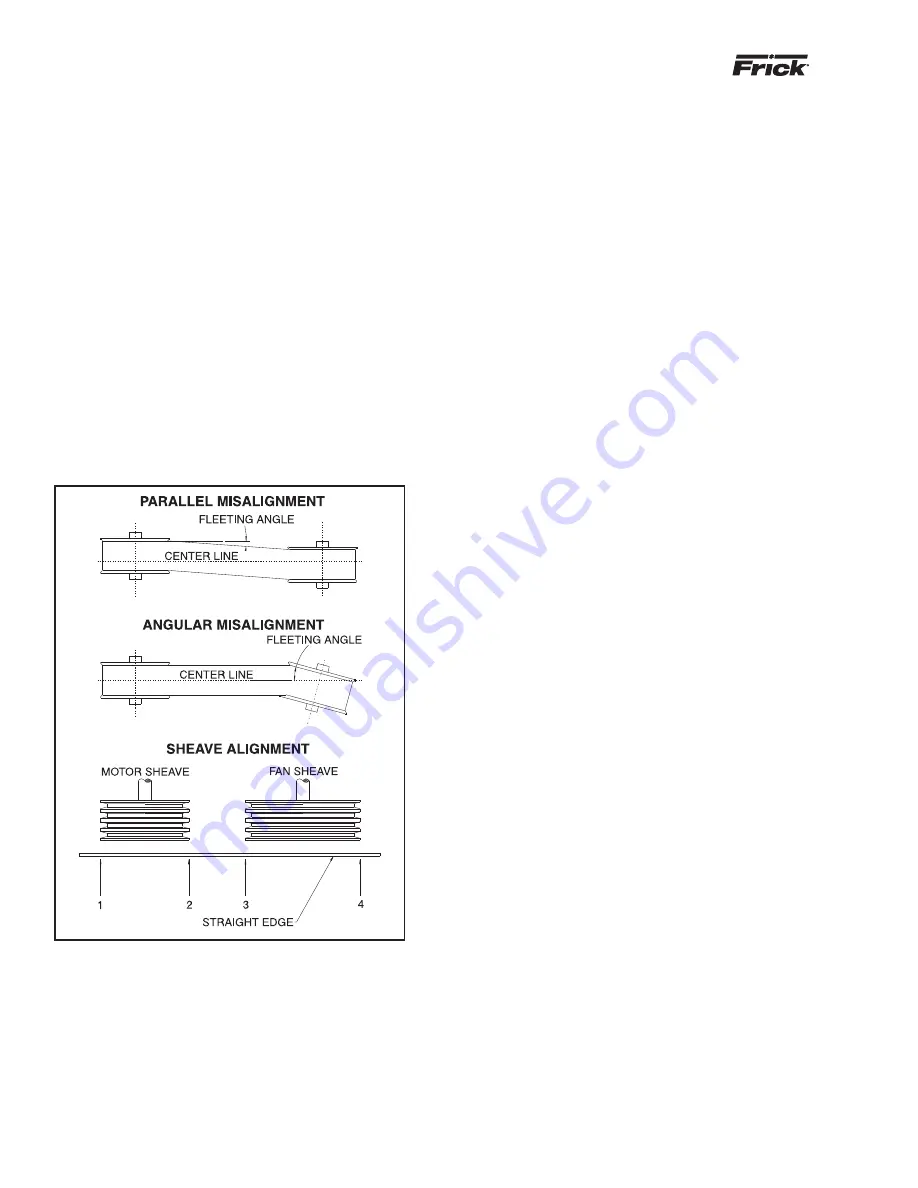
XL EVAPORATIVE COOLING PRODUCTS
MAINTENANCE
S140-600 IOM (NOV 07)
Page 14
will promote belt wear and increase turnover. Groove gauges
are also available to make it easy to see if the grooves are
worn. If more than 1/32” of wear can be seen, the sheave
should be replaced.
Alignment of sheaves is extremely important for proper belt
installation. The sheaves are aligned at the factory, but should
be rechecked when new belts are installed. Use a straight
edge to check alignment. Misalignment will show up as a gap
between the outside face and the straight edge. Two condi-
tions for misalignment exist, angular and parallel. To check
both parallel and angular alignment, refer to the Figure 14
below and follow these instructions:
1.
While placing a straight edge across the top of both motor
and fan sheaves, check for four points of contact.
2.
If a four-point contact is achieved, skip to the belt tension-
ing section.
3.
To adjust for parallel misalignment, adjust the motor or
fan shaft sheave.
4.
To adjust for angular misalignment, adjust the motor mount
adjustment nuts. This should also be done when tensioning
the belt.
Figure 14 - Sheave Alignment
Belt Replacement
When the decision is made to replace the belt, follow these
steps:
1.
Lock and tag out the starter.
2.
After the power has been turned off and the motor guard
removed, loosen the motor mount adjustment nuts.
3.
Move the motor until there is enough slack in the belt so
it can be removed without prying.
4.
Remove the old belts and inspect for unusual wear. Exces-
sive wear may indicate problems with alignment or sheave
damage.
5.
Order replacement belts from the factory to ensure a
proper belt equivalent.
6.
Inspect other drive components such as bearings and
sheaves for alignment, wear, lubrication, etc.
7.
Clean the sheaves of debris before installing the new
belt.
8
. Install the new belts, align the drive, and tension the belts
according to the procedures outlined here.
Belt Tensioning
Proper tension of a belt is very important to ensure maximum
belt life. If too little tension is applied, the belt will slip. Too
much tension can reduce belt and bearing life. It is not recom-
mended that belt dressing is used when belt slippage occurs
as this will damage the belt and cause premature failure.
1.
Decrease the center distance between the sheaves so
that the sheaves are somewhat loose.
2.
Arrange the belts so the top and bottom spans have the
same amount of sag. On vertical drives, arrange the belts so
that each side has about the same amount of slack.
3.
Apply tension to the belts by increasing the center distance
between the sheaves until the belts are snug.
4.
Operate the drive a few minutes to seat the belts in the
sheave grooves. Observe the operation of the drive during
start-up. A slight bowing of the slack side of the drive indi-
cates proper tension. If the slack side remains taut during the
peak load, the drive is to tight. Excessive bowing or slippage
indicates insuffi cient tension. If the belts squeal as the motor
comes on, they are not tight enough. The drive should be
stopped and the belts tightened.
NOTE: Do not overtighten the drive.
If the above procedure
still results in the belts squealing, but the belts are still taut
on the slack side, a more precise method of testing the belt
tension must be used. In this case, use a belt tensioning gage
available from V-belt drive manufacturers or from factory.
New Belt Run-In
During initial startup of new belts, a belt run-in procedure is
recommended. During start-up, follow these instructions:
1.
During start-up, look and listen for unusual noise or vibra-
tion.
2.
After shutting down and locking out the starter, check the
bearings and motor. If they feel hot, the belt tension may be
too tight.
3.
Run the drive under full load for 24 hours of continuous
operation. Running the belts under full load allows them to
seat themselves into the grooves.
4.
After running the drive, check the tension of the belts.
Retension to the recommended values.
This run-in procedure will reduce the future need for re-ten-
sioning and will help extend the life of the belts.