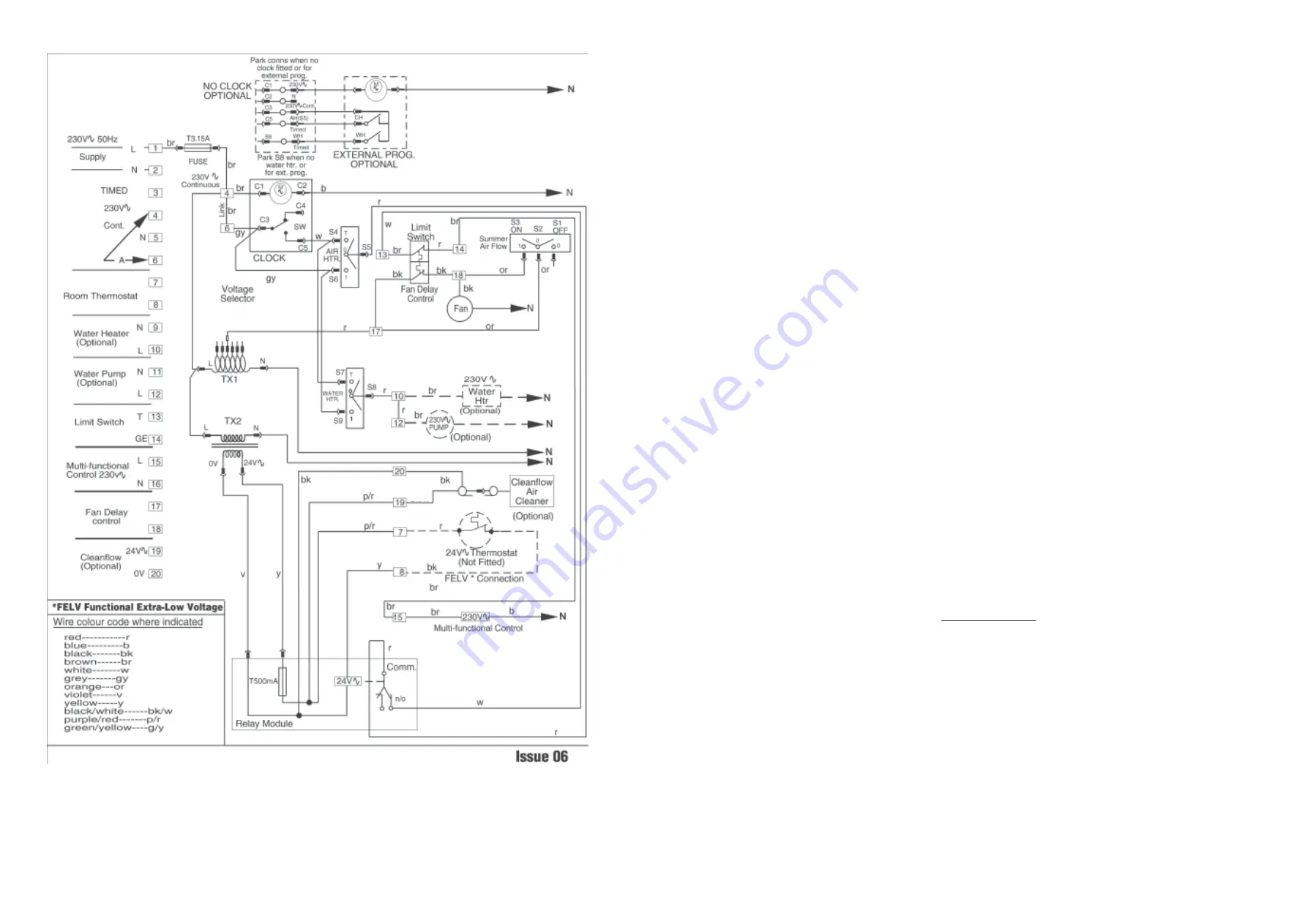
20
5
5.5
ELECTRICAL
5.5.1
Mains.
a.
The heater is supplied with mains cable (PVC sheathed, heat resisting to 85
o
C), 3-core Brown-Blue-
Green/Yellow, 6A, 0.75mm
2
), connected to a terminal block and exiting through the heater at the top left
hand front. The cable is suitable for a 230V 50Hz supply and shall be connected to the fixed wiring
using a double pole switched, fused spur, incorporating a protective earth link. The fuse fitted shall be
rated 5A to BS1362. Connections shall be in accordance with the current edition of I.E.E Regulations BS
7671.
b.
SYSTEM E-T MODELS
: An electronic controller (Thermista-stat) is supplied which acts as a room
thermostat.
c.
BASIC CONTROL MODELS
: A 24V room thermostat (not supplied), that complies with BS800,
BS3955 and BS4201 is essential to ensure close control of comfort conditions. An anticipator is located
within the thermostat and is graded in amps. The anticipator should be checked and adjusted to 0.3.
d.
To gain access to the control panel to make the Thermista-stat/Room Thermostat connections, remove the
air filter and the front cover from the air heater, release the 2 x securing screws and hinge down the
electrical panel.
5.5.2
Thermista-stat/Room Thermostat and its location.
a.
The Thermista-stat/Room Thermostat should be located where there is free air circulation approx. 1.5m
(5ft) from the floor.
b.
Avoid the following locations:-
i.
In a room where temperature is greatly affected by the sun or any other heat source, e.g. radiant
fire, wall light fittings or TV set.
ii.
Near an outside door or windows, or on an outside wall.
iii.
Where affected by warm air ducts, diffusers, waste pipes or the heater itself.
iv.
Where subject to vibration.
c.
Connect Thermista-stat/Room thermostat wires to control panel terminals ‘7’ and ‘8’ (see Fig. 6a/b
or 7a/b).
5.3
GAS
(See BS5864 and BS6891)
5.3.1
An independent gas supply pipe from the meter is to be preferred wherever possible. When this is not possible,
the pipe must be capable of taking the complete input of the heater and all other gas appliances being served by
this same pipe. This supply should be suitably sized to conform to British Standards requirements of no more than
1.0 mbar (0.4in wg) pressure drop (See table of discharge in BS6891).
5.3.2
The 1/2in union gas cock (supplied) must be fitted to the gas inlet of the heater for easy isolation during
servicing. The gas pipe should be so fitted and installed as to be durable, substantial and gas tight. To assist in
determining where a gas connection may not be tight, a leak detection fluid should be applied around the
connection. Under no circumstances should a flame be used to locate a gas leak. Gas entry to the air heater is
through either side to a Rc1/2 (1/2in BSP. external [taper] thread).
6.
COMMISSIONING
6.1
PREPARATION:
6.1.1
Ensure that:
a.
Gas and Electrical supplies are
OFF
.
b.
Filter, fan and fan compartments are free from obstructions.
c.
All registers or grilles are open and conform to design specifications.
d.
Return, relief and ventilation air installations are adequate.
6.2
SETTING OF FAN SPEED:
6.2.1
Remove air filter and air heater front door.
SYSTEM E-T MODELS:
On the electronic control module, set:
6.2.2
Rate Switch to ‘
MAX
’,
6.2.3
Cleanflow switch to ‘
0
’. (If not fitted)
Fig. 6b, BASIC CONTROL FUNCTIONAL DIAGRAM
r