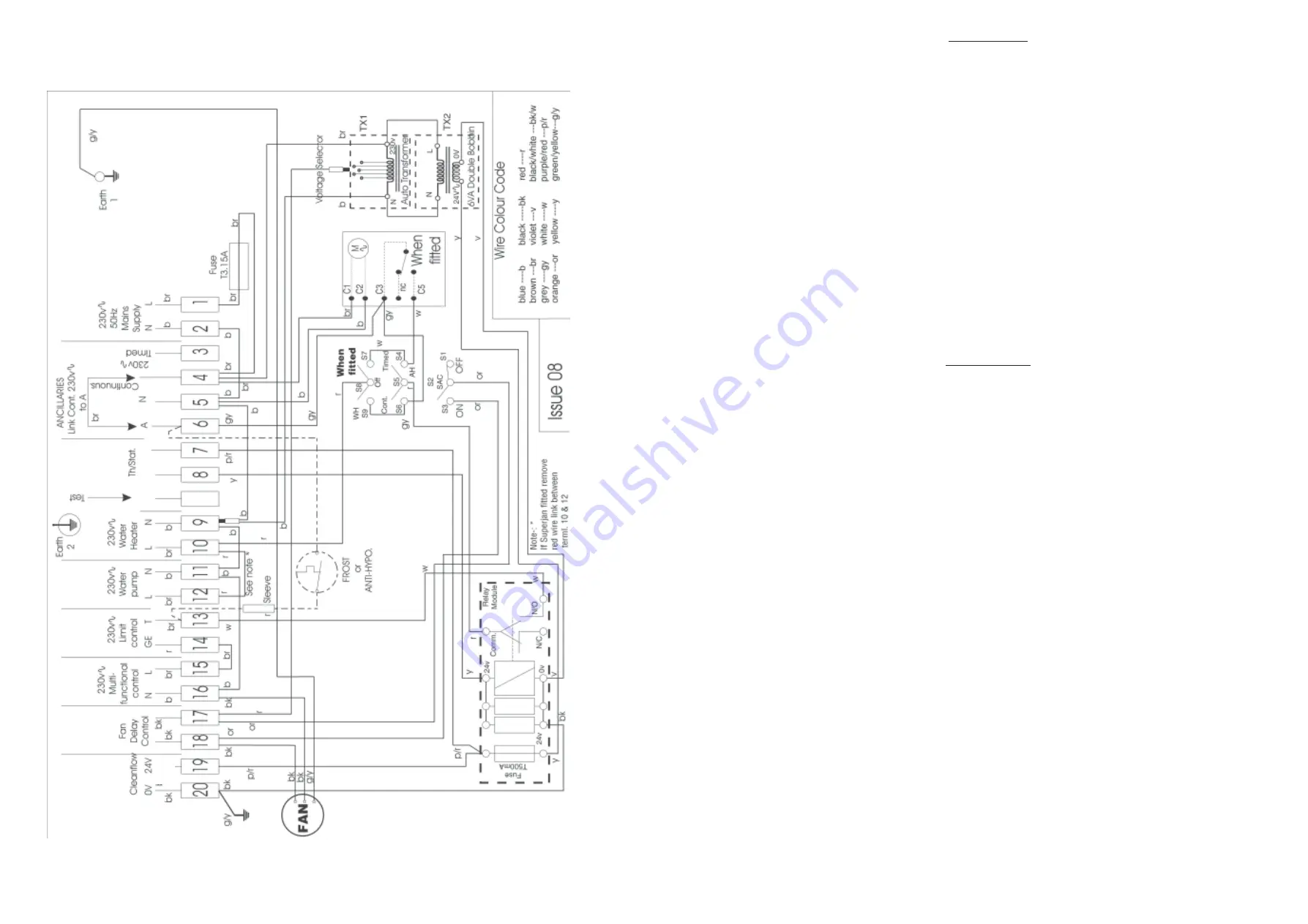
22
4.
DUCT SYSTEM
All ductwork
MUST
be mechanically secured and sealed with good quality ducting tape.
4.1
RETURN AIR
4.1.1
Room-sealed appliances may be installed without return air ducting provided that the path between the return air
grille and the appliance return air inlet is protected in such a manner that the required airflow will be maintained at
all times. The return air grille should have a free area of not less than 0.06m
2
(93 in
2
).
4.1.2
An adequate and unobstructed return air path is essential from areas served by a directly ducted return and to
which warm air is delivered. All such rooms should be fitted with relief grilles which have a free area of
0.0088m
2
/kW (1 in
2
/250Btu/h) of heat supplied to the room. The only exceptions are kitchens, bathrooms and
w.c’s.
4.2
WARM DELIVERED AIR
4.2.1
All ductwork, including riser ducts, should be fully insulated with 50m (2 in.) of fibreglass or similar. If short
extended duct runs are taken below floor level, these should be similarly insulated and in addition, wrapped with a
sound vapour proof barrier and protected from crushing.
4.2.2
The duct system should be carefully designed to suit the needs of its specific heating requirements and building
layout. The type of duct system, i.e., radial/extended plenum/stepped, should be installed using the least number of
fittings to minimise the resistance to air flow.
4.2.3
The base duct, which equalises the air pressure to supply ducts, shall be constructed to support the weight of the
heater, which shall be secured to the plenum with screws on at least two sides, and sealed using self-adhesive
foam strip, ducting tape or sealing compound. All ducting and blanking plates shall be mechanically secured and
sealed.
5.
INSTALLATION
5.1
SIDE RETURN AIR
If return air is to be introduced via the side of the appliance, it will be necessary to prepare it prior to installation. Return
air ducting may be connected to either side of the heater as follows:
5.1.1
Remove the air filter, front cover and the air circulation fan.
5.1.2
Cut a hole in the chosen side of the fan compartment. The knock outs will determine the size and position.
5.1.3
Remove and the filter frame retaining screws and remove the filter frame.
5.1.4
Position the filter frame centrally over the prepared hole so that the front of the frame is flush with the front of
the heater.
5.1.5
Using the frame as a template, mark and drill the 6 x 3.2mm dia. frame fixing holes.
5.1.6
Secure the filter frame to the side of the heater using the screws previously removed.
5.1.7
Refit the air circulation fan, front cover and air filter.
5.1.8
Using suitable material, manufacture a plate to cover the original return air opening in the top of the air heater, and
secure with self tapping screws (not provided).
5.2
SE-DUCT PREPARATION
5.2.1
Ensure that the existing air heater has first been removed.
IMPORTANT: Many SE-ducts are constructed from asbestos-based materials, and due to dimensional
variations between Johnson & Starley and other manufacturers appliances, a certain amount of rework
will be required on the SE-duct by REGISTERED CONTRACTORS.
5.2.2
In some circumstances, the SE-duct may be completely exposed and special components needed to complete the
installation. Consult Johnson & Starley Service Department if this situation is encountered.
5.2.3
Referring to Fig. 2, NOTE THE DATUM POINTS INDICATED before proceeding.
A Sealing
Template Kit (ST25) is available for cutting the holes in the SE-duct.
5.2.4
Thoroughly clean and replace the sealing material from the top of the existing base duct.
5.2.5
The holes in the SE-duct
MUST
correspond with the positions ‘
A
’ and ‘
B
’ as shown in Fig. 2, 138mm (5.5 in.)
minimum diameter, 152mm (6.0in.) maximum diameter, and clear the duct of all resulting debris. Should the
original heater be a SUGG Type 22/WH ‘Halcyon’, the existing bottom hole is suitable for use.
5.2.6
Seal the redundant hole/s in the SE-duct using a suitable cement or blanking material, to ensure a good flat surface
on both the inner and outer faces of the duct wall.
IMPORTANT:
Any debris which falls into the SE-duct MUST BE REMOVED.
3
Fig. 7b, BASIC CONTROL CIRCUIT DIAGRAM
r